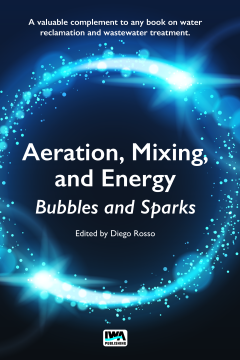
Additional Information
Book Details
Abstract
Aeration, Mixing, and Energy: Bubbles and Sparks is the first book on bubbles and sparks, presenting the state-of-the-art on aeration and mixing technology for water and wastewater treatment systems.
Aeration and mixing are the heart of wastewater treatment and must be performed well and at high efficiency for successful treatment. After reviewing the most current aeration systems, this book presents the best ways of measuring aeration system performance and to use those measurements for design, control, and sustainable operations. A team of experts in the field were assembled to help write this book, which is the product of several years of work and decades of combined experience.
Aeration, Mixing, and Energy: Bubbles and Sparks is a valuable complement to any book on water reclamation and wastewater treatment.
Table of Contents
Section Title | Page | Action | Price |
---|---|---|---|
Cover | Cover | ||
Contents | v | ||
About the Editor | ix | ||
List of Contributors | xi | ||
Preface | xiii | ||
Chapter 1: Aeration equipment | 1 | ||
1.1 INTRODUCTION | 1 | ||
1.2 THE BLOWER HOUSE | 1 | ||
1.2.1 Types of blowers | 3 | ||
1.2.1.1 Positive displacement blowers | 4 | ||
Rotary lobe | 5 | ||
Rotary screw | 6 | ||
1.2.1.2 Centrifugal blowers | 6 | ||
Multi-stage centrifugal blowers | 7 | ||
Single-Stage Centrifugal Blowers | 9 | ||
Direct-drive or high-speed rurbo | 11 | ||
Integrally geared | 11 | ||
1.2.2 Airflow control | 11 | ||
1.2.3 Application and selection | 13 | ||
1.2.4 Blower testing | 16 | ||
1.2.5 Blower upgrades and recommendations | 16 | ||
1.3 THE AERATION TANK | 18 | ||
1.3.1 Mechanical aeration | 18 | ||
1.3.1.1 Surface aerators | 18 | ||
1.3.2 Bubble aeration | 23 | ||
1.3.2.1 Coarse-bubble systems | 23 | ||
1.3.2.2 Fine-bubble systems | 25 | ||
1.3.3 Comparative performance summary | 28 | ||
1.4 REFERENCES | 29 | ||
Chapter 2: Aeration fundamentals, performance and monitoring | 31 | ||
2.1 FUNDAMENTALS OF OXYGEN TRANSFER | 31 | ||
2.1.1 Clean water | 32 | ||
2.1.2 In process water | 35 | ||
2.1.3 The mysterious alpha factor | 37 | ||
2.1.3.1 Surfactant effects | 38 | ||
2.1.4 Fine bubbles, coarse bubbles, and droplets | 41 | ||
2.1.4.1 Technologies for bubbles and droplets generation | 41 | ||
2.1.4.2 Bubble formation | 41 | ||
2.1.4.3 Limitations in assessing oxygen transfer rate | 42 | ||
2.1.4.4 Interfacial velocities | 42 | ||
2.1.4.5 Understanding differences in interfacial regimes | 43 | ||
2.2 FACTORS AFFECTING OXYGEN TRANSFER | 45 | ||
2.2.1 The impact of sludge retention time | 45 | ||
2.2.2 Role of selectors | 47 | ||
2.2.3 Reactor characteristics | 50 | ||
2.2.3.1 Airflow rate | 50 | ||
2.2.3.2 Diffuser density | 51 | ||
2.2.3.3 Flow regime | 51 | ||
2.2.3.4 Depth of the aerobic reactor | 52 | ||
2.2.4 Diffuser fouling, scaling, and cleaning | 52 | ||
2.2.5 Mixed liquor concentrations | 55 | ||
2.2.6 Extracellular polymeric substances | 57 | ||
2.2.7 The impact of environmental factors | 58 | ||
2.2.7.1 Temperature | 58 | ||
2.2.7.2 Barometric pressure | 58 | ||
2.2.7.3 Saturation concentration of oxygen in water | 59 | ||
2.2.8 Impact of hydrodynamics | 59 | ||
2.3 TESTING AERATION SYSTEMS | 60 | ||
2.3.1 Why we need testing standards | 60 | ||
2.3.2 Clean water tests | 61 | ||
2.3.3 Process water tests | 61 | ||
2.3.3.1 The evolution of the off-gas | 63 | ||
2.3.3.2 Off-gas advantages | 64 | ||
2.3.4 Testing pitfalls | 65 | ||
2.3.4.1 Dissolved oxygen probe response time | 65 | ||
2.4 REFERENCES | 66 | ||
Chapter 3: Mixing in activated sludge systems | 73 | ||
3.1 INTRODUCTION | 73 | ||
3.1.1 Mixing and aeration: either, both or neither? | 75 | ||
3.1.2 Conservative approach: a typical headache | 76 | ||
3.1.3 Mixing and flocculation | 77 | ||
3.2 QUANTIFYING THE DEGREE OF MIXING | 78 | ||
3.2.1 Quantifying mixing: traditional methods | 78 | ||
3.2.1.1 Coefficient of Variation (CoV) | 79 | ||
3.2.1.2 Maximum variations of solids | 80 | ||
3.2.1.3 Height of the cloud | 80 | ||
3.2.1.4 Reaction rates improvement/Biological activity indicators | 81 | ||
DO and ORP mapping | 81 | ||
OUR mapping | 82 | ||
Temperature | 85 | ||
3.2.2 New generation: methods for mixing quantification | 85 | ||
3.3 DESIGN CRITERIA | 86 | ||
3.3.1 Comparison criteria for mixing methods | 86 | ||
3.3.2 Mixing design criteria: rules of thumb | 87 | ||
3.3.3 Mixing efficiency and power requirements | 89 | ||
3.4 MIXING EQUIPMENT | 93 | ||
3.4.1 Rotating impellers | 94 | ||
3.4.2 Pump mixers | 95 | ||
3.4.2.1 Case study: pump mixer in sequencing batch reactor | 96 | ||
3.4.3 Air-powered mixing | 99 | ||
3.4.3.1 Air for unaerated zones | 100 | ||
3.4.3.2 Hydraulic mixing: using only flow energy | 101 | ||
3.4.3.3 Case study: mixing without a mixer? | 101 | ||
3.5 REFERENCES | 105 | ||
Chapter 4: Aeration control – fundamentals | 109 | ||
4.1 MOTIVES FOR CONTROL | 109 | ||
4.1.1 The significance of dynamics | 111 | ||
4.1.2 The concept of feedback | 112 | ||
4.1.2.1 Design of DO control – concepts to consider | 116 | ||
4.1.2.2 Driving forces – demand pull and technology push | 116 | ||
4.1.2.3 Some historical notes – the early years of aeration control | 117 | ||
4.2 PROCESS DYNAMICS | 119 | ||
4.2.1 Dynamics of the aeration supply system | 120 | ||
4.2.2 Dynamics of microbial processes in nitrogen removal | 120 | ||
4.2.2.1 Advanced reading – microorganisms in the bioreactor | 116 | ||
4.3 CONTROL STRUCTURES AND ALGORITHMS | 123 | ||
4.3.1 Control structures | 123 | ||
4.3.1.1 Cascade control | 124 | ||
4.3.1.2 Feedforward control | 125 | ||
4.3.1.3 Advanced reading – multiple-input–multiple-output controllers | 117 | ||
4.3.2 Control algorithms | 127 | ||
4.3.2.1 On–off control | 127 | ||
4.3.2.2 The proportional-integral-derivative (PID) control | 128 | ||
4.3.2.3 Advanced reading – model-based control | 129 | ||
4.3.2.4 Advanced reading – gain scheduling | 130 | ||
4.3.3 Defining the control goal | 131 | ||
4.3.4 Controller tuning | 132 | ||
4.3.4.1 Advanced reading – lambda tuning | 133 | ||
4.3.4.2 Autotuning | 134 | ||
4.3.4.3 Integral windup | 135 | ||
4.3.4.4 Prevention of integral windup | 137 | ||
4.3.4.5 Prevention of integral windup in cascade control | 137 | ||
4.3.4.6 Example of cascade wind-up | 138 | ||
4.4 SUMMARY | 139 | ||
4.5 REFERENCES | 139 | ||
Chapter 5: Aeration control – implementation | 143 | ||
5.1 INTRODUCTION | 143 | ||
5.2 COMPONENTS OF A CONTROL SYSTEM | 144 | ||
5.2.1 Sensors in aeration control | 144 | ||
5.2.1.1 Airflow measurement | 150 | ||
5.2.1.2 Installation, configuration, initialization, and base calibration | 150 | ||
5.2.1.3 Maintenance | 151 | ||
5.2.1.4 Quality control | 152 | ||
5.2.2 The air supply system: actuators | 152 | ||
5.2.2.1 Blower air supply | 152 | ||
5.2.2.2 Air distribution control | 153 | ||
5.2.2.3 How frequently should you change the airflow? | 154 | ||
5.3 IMPLEMENTING AERATION CONTROL | 154 | ||
5.3.1 Definition of control goals and constraints | 155 | ||
5.3.1.1 Definition of control goals | 155 | ||
5.3.1.2 Definition of constraints | 156 | ||
5.3.1.3 Prioritization of control goals | 156 | ||
5.3.1.4 Time plan and budget | 158 | ||
5.3.2 Data collection and analysis | 158 | ||
5.3.2.1 Data collection | 158 | ||
5.3.2.2 Discuss plant specifics | 158 | ||
5.3.3 Design and preparations | 159 | ||
5.3.3.1 Control structure and algorithms | 159 | ||
Consideration on ammonia control loops | 163 | ||
Considerations on the use of PID controllers | 163 | ||
5.3.3.2 Preliminary controller tuning | 164 | ||
5.3.3.3 Decide on instrumentation and actuators | 165 | ||
5.3.3.4 Develop safety nets and fallback strategies | 165 | ||
5.3.4 Implementation | 166 | ||
5.3.4.1 Upgrade instrumentation and actuators | 166 | ||
5.3.4.2 Controller maintenance | 166 | ||
5.3.4.3 Poor control performance during operation | 167 | ||
5.3.4.4 Sensor and actuator maintenance | 167 | ||
5.3.4.5 Implementation of control solution in control system | 168 | ||
5.3.4.6 Aeration control case study | 169 | ||
5.3.4.7 Final controller tuning | 171 | ||
5.3.4.8 Example of lambda tuning of airflow controller | 171 | ||
5.3.5 Operation and maintenance | 172 | ||
5.3.5.1 Maintenance of controllers, actuators and instrumentation | 172 | ||
5.3.5.2 Oscillations in DO cascade control | 172 | ||
5.3.5.3 Updates and improvements | 173 | ||
5.3.5.4 Operator training and education | 173 | ||
5.3.5.5 Develop and calculate performance metrics | 173 | ||
5.3.5.6 Compare to objectives and criteria | 176 | ||
5.4 OUTLOOK | 177 | ||
5.5 REFERENCES | 177 | ||
Chapter 6: Energy intensity of aeration | 179 | ||
6.1 THE ROLE OF AERATION ENERGY | 179 | ||
6.1.1 Aeration in biological wastewater treatment | 181 | ||
6.1.1.1 Energy requirements in the aeration process | 182 | ||
6.2 POWER DEMAND, ENERGY CONSUMPTION, AND TARIFFS | 183 | ||
6.2.1 Peak shaving strategies | 184 | ||
6.2.1.1 Energy conservation | 185 | ||
Equalization tanks | 185 | ||
Aeration control | 185 | ||
Energy storage | 185 | ||
6.2.2 Energy tariff structures | 187 | ||
6.2.2.1 Energy pricing structures | 187 | ||
6.2.2.2 Flat-rate structure (also called constant or fixed rate) | 187 | ||
6.2.2.3 Time-of-use rate structure (TOU) | 188 | ||
6.2.2.4 Tiered rate structure | 188 | ||
6.2.3 Billing terms: understanding the electrical bill | 189 | ||
6.2.3.1 Fixed charges | 189 | ||
6.2.3.2 Fixed power charges | 190 | ||
6.2.3.3 Energy usage charges | 191 | ||
6.2.3.4 Peak power demand charges | 191 | ||
6.2.3.5 Reactive energy charges | 191 | ||
6.2.3.6 Taxes | 192 | ||
6.2.4 Benefits of understanding energy tariff structures | 192 | ||
6.3 DYNAMICS OF AERATION ENERGY | 192 | ||
6.3.1 Circadian amplification of air requirements | 193 | ||
6.3.2 Circadian amplification of energy-associated GHG emissions | 194 | ||
6.4 ENERGY CONSEQUENCES OF INEFFICIENT OR FOULED EQUIPMENT | 196 | ||
6.4.1 From efficient to inefficient fine-pore diffusers | 196 | ||
6.4.2 Understanding fouling | 197 | ||
6.4.2.1 Linking aeration efficiency and molecular biology | 198 | ||
6.4.3 Influence of the organic load in biofouling | 201 | ||
6.4.4 Breaking down the aggregate fouling factor | 204 | ||
6.5 THE LINK BETWEEN PROCESS BIOLOGY AND POWER BILL | 205 | ||
6.5.1 Relationship between energy requirements and microbial growth | 205 | ||
6.5.2 Translating the biofouling to energy costs | 207 | ||
6.6 REFERENCES | 210 | ||
Chapter 7: Modelling aeration and energy | 215 | ||
7.1 WHY DYNAMIC MODELLING | 215 | ||
7.2 THE ART AND SCIENCE OF SPECIFYING ALPHA FACTORS | 216 | ||
7.2.1 Alpha accuracy during design and specification of aeration systems | 217 | ||
7.2.1.1 Dangers of using an α for coarse-bubbles when using jets or turbines | 221 | ||
7.2.2 Daily dynamics and α | 221 | ||
7.2.2.1 Developing a model to narrow the uncertainty on α | 223 | ||
7.2.2.2 Mathematical formulations of dynamic α | 224 | ||
7.2.3 Modelling α profiles | 227 | ||
7.3 ENERGY MODELLING OF AERATION PERFORMANCE | 232 | ||
7.3.1 SOTE curves vs. the 2%/ft assumption | 232 | ||
7.3.2 Constant vs. dynamic α | 240 | ||
7.3.3 Finding the optimal DO setpoint | 242 | ||
7.3.3.1 Further optimization options evaluated through dynamic modelling of aeration system | 244 | ||
7.3.3.2 Simulation of low-cost, high-return modifications to aeration system | 246 | ||
7.4 FUTURE OUTLOOK OF MODELLING AERATION AND ENERGY | 249 | ||
7.5 REFERENCES | 251 | ||
Chapter 8: Sustainable aeration practice: Design and diagnostics | 255 | ||
8.1 INTRODUCTION | 255 | ||
8.2 EQUIPMENT SPECIFICATION: IN SITU DATA COLLECTION | 255 | ||
8.3 EQUIPMENT PERFORMANCE MONITORING AND MAINTENANCE | 257 | ||
8.4 ROLES AND TERM DEFINITIONS: WHO IS DOING WHAT | 264 | ||
8.5 AERATION DIAGNOSTICS: WALKING AROUND THE PLANT | 266 | ||
8.6 PROCESS STABILITY BENEFITS OF GOOD AERATION PRACTICES | 268 | ||
8.7 MECHANICALLY SIMPLE AERATION SYSTEMS | 268 | ||
8.8 THE ELEPHANT IN THE ROOM: HPO PROCESSES | 270 | ||
8.9 REFERENCES | 273 | ||
Epilogue | 275 | ||
Index | 277 |