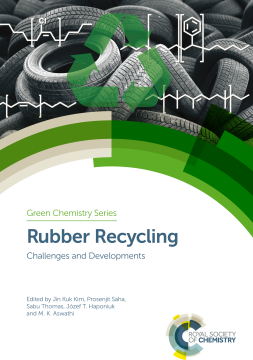
BOOK
Rubber Recycling
Jin Kuk Kim | Prosenjit Saha | Sabu Thomas | Józef T Haponiuk | M K Aswathi
(2018)
Additional Information
Book Details
Abstract
Rubber is used in a vast number of products, from tyres on vehicles to disposable surgical gloves. Increasingly both manufacturers and legislators are realising that recycling is essential for environmental sustainability and can improve the cost of manufacture. The volume of rubber waste produced globally makes it difficult to manage as accumulated waste rubber, especially in the form of tyres, can pose a significant fire risk. Recycling rubber not only prevents this problem but can produce new materials with desirable properties that virgin rubbers lack.
This book presents an up-to-date overview of the fundamental and applied aspects of renewability and recyclability of rubber materials, emphasising existing recycling technologies with significant potential for future applications along with a detailed outline of new technology based processing of rubber to reuse and recycle. This book will be of interest to researchers in both academia and industry as well as postgraduate students working in polymer chemistry, materials processing, materials science and engineering.
Table of Contents
Section Title | Page | Action | Price |
---|---|---|---|
Cover | Cover | ||
Rubber Recycling: Challenges and Developments | i | ||
Preface | vii | ||
Contents | ix | ||
Chapter 1 - Grinding of Waste Rubber | 1 | ||
1.1 Introduction | 1 | ||
1.2 Sources of Waste Rubbers | 3 | ||
1.3 Waste Rubber Grinding Routes | 3 | ||
1.4 Different Grinding Conditions | 5 | ||
1.4.1 Ambient Grinding | 6 | ||
1.4.2 Cryogenic Grinding | 8 | ||
1.4.2.1 Comparative Property Evaluation Between Ambient Grinding and Cryogenic Grinding | 9 | ||
1.4.3 Solution Grinding | 10 | ||
1.4.4 Grinding by Ozone Cracking | 10 | ||
1.4.5 Elastic Deformation Grinding | 12 | ||
1.5 Devulcanization Methods of Rubber | 17 | ||
1.5.1 Chemical | 17 | ||
1.5.2 Ultrasonic Devulcanization | 17 | ||
1.5.3 Microwave Devulcanization Method | 18 | ||
1.5.4 Biological Devulcanization Technique | 18 | ||
1.5.5 Other Devulcanization Techniques | 19 | ||
1.6 Relationship Between Energy and Particle Size for Grinding Routes | 19 | ||
1.7 Classification of Powdered Rubber | 20 | ||
1.8 Conclusion | 21 | ||
References | 21 | ||
Chapter 2 - Surface Treatment of Rubber Waste | 24 | ||
2.1 Introduction | 24 | ||
2.2 Experimental | 29 | ||
2.2.1 Materials | 29 | ||
2.2.2 Equipment | 30 | ||
2.2.2.1 Mechanical Testing | 30 | ||
2.2.2.2 Attenuated Total Reflectance FTIR Spectroscopy | 30 | ||
2.2.2.3 Scanning Electron Microscopy Analysis | 30 | ||
2.3 Surface Oxidation of the Rubber Waste Particles | 30 | ||
2.3.1 Results and Discussion | 33 | ||
2.3.1.1 Tensile Properties | 33 | ||
2.3.1.2 Scanning Electron Microscopy | 36 | ||
2.3.1.3 Spectroscopy Study of Surface Treatment (FTIR-ATR) | 37 | ||
2.3.2 Treatment of Gtr Using Oxidation Acids | 38 | ||
2.4 Coupling Agent and Chlorination Treatment on Rubber Waste Particle Surface | 39 | ||
2.4.1 Surface Treatment of GTR by TCI and Silane A-174 | 40 | ||
2.4.2 Results and Discussion | 40 | ||
2.4.2.1 Tensile Properties | 40 | ||
2.4.2.2 Scanning Electron Microscopy | 41 | ||
2.4.2.3 Spectroscopy Study of Surface Treatment (FTIR-ATR) | 41 | ||
2.4.3 Treatment of GTR Using TCI and Silane | 42 | ||
2.5 Effect of Surface Modification of Rubber Waste Grafted with EPDM | 43 | ||
2.5.1 Results and Discussion | 45 | ||
2.5.1.1 Tensile Properties | 47 | ||
2.5.1.2 Scanning Electron Microscopy | 49 | ||
2.5.1.3 Atenuatted Total Reflectance-FTIR | 50 | ||
2.5.2 Surface Modification of GTR Grafted with EPDM | 51 | ||
2.6 Global Conclusions | 52 | ||
References | 53 | ||
Chapter 3 - Thermoplastic Elastomers Filled With GTR | 56 | ||
3.1 Introduction | 56 | ||
3.2 Thermodynamics of Polymer Blends Containing GTR | 60 | ||
3.3 Preparation of Thermoplastics/GTR Blends in Variable Conditions | 61 | ||
3.3.1 Statistical Methods Used in Extrusion | 61 | ||
3.3.2 Importance of Extrusion Temperature | 62 | ||
3.3.3 Effect of Extrusion Settings | 64 | ||
3.3.4 Combined Impact of Thermoplastic Matrix Type and Screw Configuration | 65 | ||
3.4 Routes for Compatibilization of Thermoplastics/GTR Blends | 66 | ||
3.4.1 Cross-linking | 67 | ||
3.4.2 Oxidization or Reclamation of GTR | 68 | ||
3.4.3 Application of Additional Elastomer Phase | 68 | ||
3.4.4 Grafted Polymers | 70 | ||
3.4.5 Other Possibilities | 72 | ||
3.5 Conclusions | 73 | ||
References | 73 | ||
Chapter 4 - Waste Rubber Based Composite Foams | 83 | ||
4.1 Introduction | 83 | ||
4.2 Processing of Rubber Foam Composites | 85 | ||
4.2.1 Processing of Foamed Composites with GTR | 85 | ||
4.3 Properties of Foamed/GTR Composites | 87 | ||
4.3.1 Morphological Properties | 87 | ||
4.3.2 Physical Properties | 90 | ||
4.3.3 Mechanical Properties | 90 | ||
4.3.4 Damping Properties | 91 | ||
4.3.5 Thermal Properties | 93 | ||
4.4 Studies of Waste Rubber Foams | 93 | ||
4.5 Applications of Waste Rubber Foam Composites | 96 | ||
4.5.1 Non-structural Applications | 96 | ||
4.5.2 Lightweight Applications | 97 | ||
4.5.3 Sound and Vibration Absorption | 97 | ||
4.5.4 Insulation and Impact Isolation | 97 | ||
4.5.5 Drainage Systems | 97 | ||
4.6 Concluding Remarks | 97 | ||
References | 98 | ||
Chapter 5 - Recycling of Tire Rubbers and Their Re-usability | 102 | ||
5.1 Introduction | 102 | ||
5.2 Tire Composition, Tire Parts and End-of-life Tires | 104 | ||
5.3 Why Recycle Tire Rubbers | 106 | ||
5.4 Recycling of Waste/Used Tire Rubbers | 107 | ||
5.4.1 Chemical De-vulcanization Method | 109 | ||
5.4.2 Mechanical Method | 111 | ||
5.4.2.1 Mechanochemical Method | 112 | ||
5.4.2.2 Thermo-mechanical Method with De-vulcanizing Agents | 113 | ||
5.4.3 Energy Recovery Method | 114 | ||
5.4.3.1 Incineration | 115 | ||
5.4.3.2 Gasification | 115 | ||
5.4.3.3 Pyrolysis | 115 | ||
5.4.4 Microwave Method | 117 | ||
5.4.5 Ultrasonic Method | 118 | ||
5.4.6 Biological Method | 120 | ||
5.5 Reusability and Application of Tire Rubbers | 121 | ||
5.5.1 Civil Engineering Applications | 121 | ||
5.5.2 Commercial Application of De-vulcanized/Reclaimed Rubber | 122 | ||
5.5.3 Energy Production and Zinc Fertilizer | 122 | ||
5.5.4 Sound-proof Barriers | 123 | ||
5.6 Advantages of Reclaimed/De-vulcanized Rubber | 123 | ||
5.7 Disadvantages of Reclaimed/De-vulcanized Rubber | 124 | ||
5.8 Conclusion | 124 | ||
References | 124 | ||
Chapter 6 - Testing and Industrial Characterization of Waste Rubber | 128 | ||
6.1 Introduction | 128 | ||
6.2 What is Rubber | 130 | ||
6.2.1 Natural Rubber | 130 | ||
6.2.2 Synthetic Rubber | 130 | ||
6.2.3 Some Specific Elastomers | 131 | ||
6.3 Rubber Testing and Techniques | 131 | ||
6.3.1 Instrumentation | 131 | ||
6.3.1.1 Mills and Internal Milling Machines | 131 | ||
6.3.1.2 Extruders | 132 | ||
6.3.1.3 Calendars | 132 | ||
6.3.1.4 Curing Equipment | 132 | ||
6.3.2 Physical Testing | 133 | ||
6.3.2.1 Electrical | 133 | ||
6.3.2.2 Thermal Properties | 135 | ||
6.3.2.3 Permeability | 136 | ||
6.3.2.4 Adhesion | 136 | ||
6.4 Disposal of Waste Rubber: A Serious Threat to Ecology | 137 | ||
6.5 Possible Explorations of Waste Rubber | 139 | ||
6.5.1 Rubber–Rubber Blends | 139 | ||
6.5.2 Concrete Modified by Waste Rubber | 139 | ||
6.5.3 Asphalt Binders | 139 | ||
6.6 Recycling of Rubber | 139 | ||
6.6.1 Thermo-mechanical Recycling of Rubber | 140 | ||
6.6.1.1 Characterization | 141 | ||
6.6.2 Waste Rubber Recycling by Microwave Devulcanization | 143 | ||
6.6.2.1 Characterization | 143 | ||
6.6.3 Devulcanization of Natural Rubber by Mechanochemical Means | 145 | ||
6.7 Characterizing Recycled Rubber Products | 148 | ||
6.7.1 Characterizing Cross-link Density in Rubber–Rubber Blends | 148 | ||
6.7.1.1 Swollen State NMR Spectroscopy | 149 | ||
6.7.1.2 Solid State NMR Spectroscopy | 149 | ||
6.7.2 Morphological Characterizations for Rubber–Rubber Composites | 149 | ||
6.7.2.1 Scanning Electron Microscopy | 149 | ||
6.7.2.2 Transmission Electron Microscopy | 150 | ||
6.7.2.3 Scanning Probe Microscopy | 151 | ||
6.7.2.4 Chemical Staining | 152 | ||
6.7.3 Characterizing the Mechanical and Thermal Properties of Devulcanized Rubber/Polypropylene Blends | 152 | ||
6.7.4 Concrete Modified by Waste Rubber | 154 | ||
6.8 Rheological Properties of Asphalt Binders Modified with Devulcanized Rubber | 155 | ||
6.8.1 Apparent Viscosity | 155 | ||
6.8.2 Performance Grade Critical Temperature | 156 | ||
6.8.3 Rutting Resistance Factor | 156 | ||
6.8.4 Phase Angle | 156 | ||
6.9 Conclusion | 156 | ||
References | 157 | ||
Chapter 7 - High Performance Flooring Materials from Recycled Rubber | 160 | ||
7.1 Introduction | 160 | ||
7.2 Types of Flooring Materials | 162 | ||
7.3 Recycled Rubber as Flooring Materials | 167 | ||
7.4 Recycling and Processing of Scrap Rubber | 171 | ||
7.4.1 Mechanical Reclaiming Process | 173 | ||
7.4.2 Thermo-mechanical Reclaiming Process | 173 | ||
7.4.3 Cryomechanical Reclaiming Process | 174 | ||
7.4.4 Wet or Solution Grinding | 174 | ||
7.4.5 Microwave Method | 174 | ||
7.4.6 Ultrasonic Method | 174 | ||
7.4.7 Chemical Reclaiming Processes | 174 | ||
7.5 High Performance Flooring Applications of Recycled Rubber | 175 | ||
7.6 Advantages and Disadvantages of Rubber Flooring | 178 | ||
7.6.1 Advantages | 178 | ||
7.6.1.1 Durability | 178 | ||
7.6.1.2 Water Resistance | 178 | ||
7.6.1.3 Fire and Burn Resistance | 178 | ||
7.6.1.4 Sound/Acoustic Properties | 179 | ||
7.6.1.5 Colour Choices | 179 | ||
7.6.1.6 Textures | 179 | ||
7.6.1.7 Low Maintenance | 179 | ||
7.6.1.8 Softness | 179 | ||
7.6.2 Disadvantages of Rubber Tile Floorings | 180 | ||
7.6.2.1 Expensive | 180 | ||
7.6.2.2 Slippage | 180 | ||
7.6.2.3 Above Grade | 180 | ||
7.6.2.4 Staining | 180 | ||
7.7 Conclusions | 180 | ||
References | 181 | ||
Chapter 8 - Recycling of Individual Waste Rubbers | 186 | ||
8.1 Introduction | 186 | ||
8.2 Theoretical Background | 188 | ||
8.2.1 Agents for Selective Scission of Sulfur Crosslinks | 188 | ||
8.2.2 Radical Scavengers | 190 | ||
8.2.3 Model for Analysis of De-vulcanization Efficiency | 194 | ||
8.2.3.1 Sol-Gel Analysis | 194 | ||
8.2.3.1.1\rNetwork Formation by Crosslinking7.According to Charlesby polymers can be classified into two groups, according to their respons... | 194 | ||
8.2.3.1.2\rNetwork Breakdown (Horikx).Assuming that network breakdown leads to a Poisson distribution of molecular fragments, Horikx used C... | 197 | ||
8.2.3.1.3\rIntermediate Stages Between Crosslink Breakage and Main-chain Scission (Yashin and Isayev).The disadvantage of the Horikx treatm... | 200 | ||
8.2.3.2 Chemorheology | 201 | ||
8.3 De-vulcanization of SBR | 203 | ||
8.3.1 Thermal De-vulcanization of SBR | 203 | ||
8.3.2 Thermo-chemical De-vulcanization of SBR | 206 | ||
8.3.3 Chemical De-vulcanization of SBR with the Aid of Stabilizers | 211 | ||
8.4 De-vulcanization of BR | 216 | ||
8.5 De-vulcanization of NR | 218 | ||
8.6 De-vulcanization of CIIR | 219 | ||
8.7 De-vulcanization of EPDM | 223 | ||
8.7.1 Example of the Re-use of De-vulcanized Rubber: EPDM Roofing Foil | 226 | ||
8.8 Concluding Remarks | 229 | ||
References | 230 | ||
Chapter 9 - Recycling of Latex Waste and Latex Products | 233 | ||
9.1 Introduction | 233 | ||
9.2 Latex Waste | 234 | ||
9.3 Recycling of Liquid Latex Waste | 235 | ||
9.3.1 Laminated Mould Cleaning | 235 | ||
9.3.2 Outdoor Cleaning | 242 | ||
9.3.3 Former Cleaning | 246 | ||
9.3.4 Blending of Waste NR Latex | 249 | ||
9.3.5 Recycling of Latex Paint | 250 | ||
9.4 Recycling of Latex Products | 251 | ||
9.4.1 Reclaiming of Latex Waste Products | 251 | ||
9.4.2 Latex Waste Products as Filler | 253 | ||
9.5 Conclusions | 255 | ||
References | 255 | ||
Chapter 10 - Recycling of Rubber Blends for Durable Construction | 259 | ||
10.1 Introduction | 259 | ||
10.2 Recycling of Rubber Based Blends for Durable Construction | 261 | ||
10.3 Conclusion | 271 | ||
References | 271 | ||
Chapter 11 - Recycling of Rubber Composites and Nanocomposites | 275 | ||
11.1 Introduction | 275 | ||
11.2 Various Nanofillers | 277 | ||
11.3 Recycling of Rubber Nanocomposites | 278 | ||
11.4 Reclamation of Rubber Composites/Waste Tires | 281 | ||
11.5 Application of Rubber in Construction | 298 | ||
11.6 Conclusion | 304 | ||
References | 305 | ||
Chapter 12 - Hybrid Nano-filler for Value Added Rubber Compounds for Recycling | 310 | ||
12.1 Introduction | 310 | ||
12.2 Fabrication of Hybrid Nanofillers/Rubber Nanocomposites | 314 | ||
12.2.1 Intercalation Method | 315 | ||
12.2.2 In situ Polymerization | 315 | ||
12.2.3 Mechanical Mixing Method | 315 | ||
12.2.4 Sol–Gel Method | 316 | ||
12.2.5 Melt Compounding Method | 317 | ||
12.2.6 Solution Blending Method | 318 | ||
12.2.7 Latex Compounding Method | 318 | ||
12.3 Methods of Recycling | 318 | ||
12.3.1 Biological Method | 319 | ||
12.3.2 Ambient Mechanical Recycling Method | 319 | ||
12.3.3 Thermal Process of Recycling | 321 | ||
12.3.4 Pan Technique | 321 | ||
12.3.5 Digester Technique | 321 | ||
12.3.6 Alkaline Technique | 321 | ||
12.3.7 High-pressure Steam Technique | 322 | ||
12.3.8 Thermo-mechanical Recycling Process | 322 | ||
12.3.9 Cryogenic Grinding Process | 322 | ||
12.3.10 Pyrolysis Process | 323 | ||
12.3.11 Microwave Recycling Technique | 323 | ||
12.4 Effect of Nano-fillers on Rubber Recycling | 324 | ||
12.5 Conclusion | 325 | ||
References | 326 | ||
Subject Index | 330 |