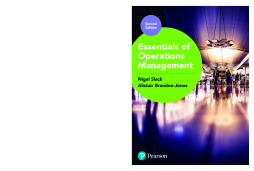
Additional Information
Book Details
Abstract
Based on the market-leading Operations Management text, this is the ideal book for those wanting a more concise introduction to the subject, focusing on essential core topics, without compromising on the authoritative, clear and highly practical approach that has become the trademark of the authors.
Revised and updated to reflect the ever-changing world of operations management, the book is rooted in real-life practice with a wealth of examples and case studies from different sectors and industries around the world.
Table of Contents
Section Title | Page | Action | Price |
---|---|---|---|
Front Cover | Front Cover | ||
Half Title Page | i | ||
Title Page | iii | ||
Copyright Page | iv | ||
Brief Contents | v | ||
Contents | vii | ||
Guide to ‘Operations in practice’ examples | xv | ||
Preface | xix | ||
To the instructor | xxii | ||
To the student | xxiii | ||
Ten steps to getting a better grade in operations management | xxiv | ||
About the authors | xxvi | ||
Acknowledgements | xxviii | ||
Publisher’s acknowledgements | xxx | ||
Operations management and performance | 2 | ||
Introduction | 3 | ||
Key questions | 3 | ||
What is operations management? | 4 | ||
Operations can produce both services and products | 6 | ||
Operations management in not-for-profit organizations | 9 | ||
What is the input–transformation–output process? | 10 | ||
Inputs to the process | 11 | ||
Why is operations management important to an organization’s performance? | 13 | ||
Performance at three levels | 14 | ||
What is the processes hierarchy? | 20 | ||
Operations management is relevant to all parts of the business | 21 | ||
Business processes | 22 | ||
How do operations and processes differ? | 23 | ||
The volume dimension | 24 | ||
The variety dimension | 24 | ||
The variation dimension | 24 | ||
The visibility dimension | 25 | ||
The implications of the four Vs of operations processes | 26 | ||
What do operations managers do? | 27 | ||
The model of operations management | 31 | ||
Summary answers to key questions | 32 | ||
Problems and applications | 34 | ||
Want to know more? | 36 | ||
Operations strategy | 38 | ||
Introduction | 39 | ||
Key questions | 39 | ||
What is strategy and what is operations strategy? | 40 | ||
Operations strategy | 42 | ||
Hayes and Wheelwright’s four stages of operations contribution | 42 | ||
Perspectives on operations strategy | 43 | ||
What is the difference between a ‘top-down’ and ‘bottom-up’ view of operations strategy? | 44 | ||
‘Top-down’ strategies | 44 | ||
‘Bottom-up’ strategies | 45 | ||
What is the difference between a market requirements and operations resources view of operations strategy? | 47 | ||
Market requirements-based strategies | 47 | ||
The operations resources perspective | 52 | ||
How can operations strategy form the basis for operations improvement? | 58 | ||
The ‘line of fit’ between market requirements and operations capabilities | 58 | ||
What is the ‘process’ of operations strategy? | 60 | ||
Operation strategy formulation | 60 | ||
Operations strategy implementation | 62 | ||
Operations strategy monitoring | 62 | ||
Operations strategy control | 63 | ||
Summary answers to key questions | 64 | ||
Problems and applications | 66 | ||
Want to know more? | 68 | ||
Product and service innovation | 70 | ||
Introduction | 71 | ||
Key questions | 71 | ||
What is product and service innovation? | 72 | ||
Innovation, creativity and design | 72 | ||
Incremental or radical innovation | 73 | ||
What is the strategic role of product and service innovation? | 75 | ||
The process of design | 76 | ||
Design process objectives | 76 | ||
What are the stages of product and service innovation? | 81 | ||
Concept generation | 82 | ||
Concept screening | 83 | ||
Preliminary design | 85 | ||
Reducing design complexity | 86 | ||
Design evaluation and improvement | 87 | ||
Prototyping and final design | 89 | ||
What are the benefits of interactive product and service innovation? | 90 | ||
Simultaneous development | 90 | ||
Early conflict resolution | 91 | ||
Project-based organizational structures | 92 | ||
Summary answers to key questions | 95 | ||
Problems and applications | 97 | ||
Want to know more? | 98 | ||
Process design – resources | 100 | ||
Introduction | 101 | ||
Key questions | 101 | ||
Why is choosing the right resources important? | 102 | ||
Process design and product/service design are interrelated | 102 | ||
Do processes match volume–variety requirements? | 103 | ||
The ‘product–process’ matrix | 104 | ||
Process types | 105 | ||
Moving off the natural diagonal | 108 | ||
Are process layouts appropriate? | 110 | ||
Layout should reflect volume and variety | 110 | ||
Layout selection | 113 | ||
Advantages and disadvantages of layout types | 114 | ||
Layout and ‘servicescapes’ | 114 | ||
Are process technologies appropriate? | 115 | ||
Process technology should reflect volume and variety | 116 | ||
Are job designs appropriate? | 119 | ||
Job design should reflect volume and variety | 119 | ||
To what degree should jobs be defined? | 121 | ||
How should job commitment be encouraged? | 123 | ||
Summary answers to key questions | 125 | ||
Problems and applications | 127 | ||
Want to know more? | 128 | ||
Process design – analysis | 130 | ||
Introduction | 131 | ||
Key questions | 131 | ||
Why is it important to get the details of process design correct? | 132 | ||
What should be the objectives of process design? | 134 | ||
‘Micro’ objectives | 134 | ||
Standardization of processes | 136 | ||
Environmentally sensitive process design | 137 | ||
How are processes currently designed? | 138 | ||
Process mapping | 139 | ||
Are process tasks and capacity configured appropriately? | 143 | ||
Throughput time, cycle time and work in progress | 143 | ||
Workflow | 147 | ||
Process bottlenecks | 148 | ||
Arranging the stages | 149 | ||
Is process variability recognized? | 152 | ||
Summary answers to key questions | 157 | ||
Problems and applications | 159 | ||
Want to know more? | 161 | ||
Supply chain management | 162 | ||
Introduction | 163 | ||
Key questions | 163 | ||
What is supply chain management? | 164 | ||
Internal and external supply chains | 167 | ||
Tangible and intangible supply chains | 167 | ||
How do supply chains compete? | 167 | ||
Performance objectives for supply networks | 169 | ||
Lean versus agile supply networks | 171 | ||
How should you manage supply chain relationships? | 173 | ||
Contracting and relationships | 173 | ||
Which type of relationship? | 176 | ||
How should the supply side be managed? | 177 | ||
Sourcing strategy | 177 | ||
Global sourcing | 180 | ||
Supplier selection | 180 | ||
Managing on-going supply | 182 | ||
Improving supplier capabilities | 184 | ||
How should the demand side be managed? | 184 | ||
Logistics services | 185 | ||
Customer relationship management (CRM) | 186 | ||
Customer development | 187 | ||
What are the dynamics of supply chains? | 188 | ||
Controlling supply chain dynamics | 190 | ||
Summary answers to key questions | 192 | ||
Problems and applications | 194 | ||
Want to know more? | 196 | ||
Capacity management | 198 | ||
Introduction | 199 | ||
Key questions | 199 | ||
What is capacity management? | 200 | ||
Long-, medium- and short-term capacity management | 201 | ||
What are the main long-term capacity decisions? | 201 | ||
Economies of scale and the ‘optimum’ capacity level | 201 | ||
The timing of capacity change | 203 | ||
What are the main medium-term capacity decisions? | 205 | ||
The objectives of capacity management | 206 | ||
Understanding medium-term demand | 206 | ||
Understanding medium-term capacity | 207 | ||
Both demand and capacity can vary | 210 | ||
Predictable and unpredictable variation | 211 | ||
What are the ways of coping with mismatches between medium-term demand and capacity? | 213 | ||
Level capacity plan | 213 | ||
Chase demand plan | 214 | ||
Demand management plan | 216 | ||
Yield management | 218 | ||
How can operations understand the consequences of their medium-term capacity decisions? | 218 | ||
Considering capacity decisions using cumulative representations | 219 | ||
Considering capacity decisions using queuing principles | 220 | ||
Considering capacity decisions over time | 225 | ||
Summary answers to key questions | 227 | ||
Problems and applications | 229 | ||
Want to know more? | 232 | ||
Inventory management | 234 | ||
Introduction | 235 | ||
Key questions | 235 | ||
What is inventory? | 236 | ||
All processes, operations and supply networks have inventories | 237 | ||
Why do you need inventory? | 239 | ||
So why have inventory? | 240 | ||
Reducing physical inventory | 243 | ||
Day-to-day inventory decisions | 244 | ||
How much should you order? (The volume decision) | 245 | ||
The economic order quantity (EOQ) formula | 247 | ||
Gradual replacement – the economic batch quantity (EBQ) model | 251 | ||
Criticisms of EOQ models | 252 | ||
When should you order? (The timing decision) | 254 | ||
Continuous and periodic review | 258 | ||
How can you control inventory? | 260 | ||
Using the ABC system to prioritize inventories | 261 | ||
Measuring inventory | 263 | ||
Inventory information systems | 263 | ||
Common problems with inventory systems | 267 | ||
Summary answers to key questions | 269 | ||
Problems and applications | 271 | ||
Want to know more? | 272 | ||
Resource planning and control | 274 | ||
Introduction | 275 | ||
Key questions | 275 | ||
What is resource planning and control? | 276 | ||
What is the difference between planning and control? | 278 | ||
Long-, medium- and short-term resource planning and control | 278 | ||
How do supply and demand affect planning and control? | 280 | ||
Uncertainty in supply and demand | 280 | ||
Dependent and independent demand | 280 | ||
Responding to demand | 281 | ||
P:D ratios | 284 | ||
What are the activities of planning and control? | 285 | ||
Loading | 285 | ||
Sequencing | 287 | ||
Scheduling | 291 | ||
Monitoring and controlling the operation | 297 | ||
Drum, buffer, rope | 298 | ||
What is enterprise resource planning (ERP)? | 299 | ||
How did ERP develop? | 301 | ||
Summary answers to key questions | 303 | ||
Problems and applications | 304 | ||
Want to know more? | 306 | ||
Lean operations | 308 | ||
Introduction | 309 | ||
Key questions | 309 | ||
What is lean? | 310 | ||
Three perspectives of lean | 312 | ||
How lean operations consider flow | 312 | ||
How lean operations consider inventory | 314 | ||
How lean operations consider capacity utilization | 315 | ||
How lean operations consider the role of people | 315 | ||
How lean operations consider improvement | 318 | ||
How does lean eliminate waste? | 318 | ||
Causes of waste – muda, mura, muri | 319 | ||
Types of waste | 319 | ||
Looking for waste (and kaizen opportunities) – the ‘gemba walk’ | 321 | ||
Eliminating waste through streamlined flow | 321 | ||
Eliminating waste through matching demand and supply exactly | 326 | ||
Eliminating waste through flexible processes | 328 | ||
Eliminating waste through minimizing variability | 331 | ||
Keeping things simple – the 5S method | 334 | ||
How does lean apply throughout the supply network? | 334 | ||
Summary answers to key questions | 337 | ||
Problems and applications | 338 | ||
Want to know more? | 340 | ||
Operations improvement | 342 | ||
Introduction | 343 | ||
Key questions | 343 | ||
Why is improvement so important in operations management? | 344 | ||
Radical, or breakthrough, change | 346 | ||
Continuous, or incremental, improvement | 347 | ||
Exploitation or exploration | 347 | ||
The structure of improvement ideas | 348 | ||
Why is failure management also improvement? | 349 | ||
Assessing the potential causes and consequences of failure | 349 | ||
How can failure be prevented? | 350 | ||
How can operations mitigate the effects of failure? | 351 | ||
How can operations recover from the effects of failure? | 351 | ||
What are the key elements of operations improvement? | 352 | ||
Improvement cycles | 352 | ||
A process perspective | 353 | ||
End-to-end processes | 353 | ||
Evidence-based problem solving | 353 | ||
Customer-centricity | 354 | ||
Systems and procedures | 354 | ||
Reduce process variation | 355 | ||
Synchronized flow | 356 | ||
Emphasize education/training | 356 | ||
Perfection is the goal | 356 | ||
Waste identification | 356 | ||
Include everybody | 356 | ||
Develop internal customer–supplier relationships | 357 | ||
What are the broad approaches to improvement? | 357 | ||
Total quality management as an improvement approach | 357 | ||
Lean as an improvement approach | 358 | ||
Business process re-engineering (BPR) | 358 | ||
Six Sigma | 361 | ||
Differences and similarities | 362 | ||
What techniques can be used for improvement? | 364 | ||
Scatter diagrams | 364 | ||
Process maps (flow charts) | 365 | ||
Cause–effect diagrams | 366 | ||
Pareto diagrams | 367 | ||
Why–why analysis | 368 | ||
Benchmarking | 370 | ||
Summary answers to key questions | 371 | ||
Problems and applications | 373 | ||
Want to know more? | 375 | ||
Quality management | 376 | ||
Introduction | 377 | ||
Key questions | 377 | ||
What is quality and why is it so important? | 378 | ||
The operation’s view of quality | 378 | ||
Customers’ view of quality | 379 | ||
Reconciling the operation’s and the customer’s views of quality | 380 | ||
How can quality problems be diagnosed? | 383 | ||
What steps lead towards conformance to specification? | 384 | ||
Step 1 – define the quality characteristics | 385 | ||
Step 2 – decide how to measure each characteristic | 386 | ||
Step 3 – set quality standards | 386 | ||
Step 4 – control quality against those standards | 387 | ||
Steps 5 and 6 – find and correct causes of poor quality and continue to make improvements | 393 | ||
What is total quality management (TQM)? | 394 | ||
TQM as an extension of previous practice | 394 | ||
The principles of TQM | 395 | ||
TQM means meeting the needs and expectations of customers | 396 | ||
TQM means covering all parts of the organization | 396 | ||
TQM means including every person in the organization | 397 | ||
TQM means all costs of quality are considered | 398 | ||
TQM means developing the systems and procedures that support quality and improvement | 401 | ||
Summary answers to key questions | 404 | ||
Problems and applications | 406 | ||
Want to know more? | 407 | ||
Project management | 408 | ||
Introduction | 409 | ||
Key questions | 409 | ||
What is project management? | 410 | ||
What do projects have in common? | 410 | ||
What is project management exactly? | 412 | ||
Not all projects are the same | 412 | ||
The stages of project management | 415 | ||
What is a project’s ‘environment’? | 416 | ||
The role of stakeholders in projects | 416 | ||
Project definition | 418 | ||
How can projects be planned? | 420 | ||
Identify activities – the work breakdown structure | 420 | ||
Estimate times and resources | 421 | ||
Identify relationships and dependencies | 422 | ||
Identify schedule constraints | 426 | ||
Fix the schedule | 427 | ||
Network analysis | 428 | ||
Program evaluation and review technique (PERT) | 429 | ||
How can projects be controlled? | 432 | ||
Project monitoring | 432 | ||
Assessing project performance | 433 | ||
Intervening to change the project | 433 | ||
Managing matrix tensions | 434 | ||
Summary answers to key questions | 435 | ||
Problems and applications | 437 | ||
Want to know more? | 439 | ||
Notes | 440 | ||
Index | 444 | ||
Back Cover | Back Cover |