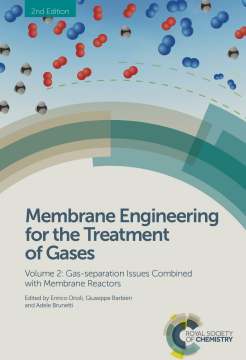
BOOK
Membrane Engineering for the Treatment of Gases
Enrico Drioli | Giuseppe Barbieri | Adele Brunetti
(2017)
Additional Information
Book Details
Abstract
Elaborating on recent and future developments in the field of membrane engineering, Volume 2 is devoted to the main advances in gaseous phase membrane reactors and separators. The book covers innovative membranes and new processes, and includes new chapters on cost analysis and life cycle assessment. Together with Volume 1, these books form an innovative reference work on membrane engineering and technology in the field of gas separation and gaseous phase membrane reactors.
Table of Contents
Section Title | Page | Action | Price |
---|---|---|---|
Cover | Cover | ||
Membrane Engineering for the Treatment of Gases Volume 2: Gas-separation Issues Combined with Membrane Reactors | i | ||
Preface | v | ||
Contents | vii | ||
Contents | xiii | ||
Chapter 1 - Membrane Reactors for Hydrogen Production | 1 | ||
1.1 Introduction | 1 | ||
1.2 Membranes for Hydrogen Production | 4 | ||
1.3 MR Configurations for Hydrogen Production | 5 | ||
1.3.1 Packed Bed MRs | 5 | ||
1.3.2 Fluidized Bed MRs | 6 | ||
1.3.3 Micro-MRs | 7 | ||
1.4 Current and Potential Applications of MRs for Hydrogen Production | 10 | ||
1.4.1 Steam Reforming of Methane and Other Light Hydrocarbons | 10 | ||
1.4.1.1 Autothermal Reforming | 11 | ||
1.4.2 Water–Gas Shift (WGS) Reaction | 11 | ||
1.4.3 MRs for Dehydrogenation Reactions | 15 | ||
1.5 New Indexes for the Comparison of Membrane and Traditional Reactors | 18 | ||
1.6 Conclusions | 24 | ||
Acknowledgements | 24 | ||
References | 24 | ||
Chapter 2 - Chemical Looping for Hydrogen Production and Purification | 30 | ||
2.1 Introduction | 30 | ||
2.2 Chemical Looping and Membrane Reactor Concepts | 34 | ||
2.2.1 Membrane-assisted Chemical Looping Reforming Concept | 36 | ||
2.3 Thermodynamics | 38 | ||
2.4 Hydrodynamics | 44 | ||
2.5 Proof-of-Concept: Oxygen Carrier, Membrane Testing, and Fluidized Bed Membrane Reactor Experiments | 46 | ||
2.6 Conclusions | 53 | ||
Acronyms | 53 | ||
Acknowledgements | 54 | ||
References | 54 | ||
Chapter 3 - Oxidative Coupling of Methane in Membrane Reactors | 58 | ||
3.1 Introduction | 58 | ||
3.1.1 Reactions, Mechanisms, and Important Aspects | 59 | ||
3.1.2 Research Structure on OCM Membrane Reactor | 61 | ||
3.2 Experimentation | 62 | ||
3.2.1 Membrane Modification | 63 | ||
3.2.1.1 Silica–Sol Impregnation Method | 63 | ||
3.2.1.2 SiliconOxyCarbide (SiOC) Coating Method | 64 | ||
3.2.1.3 Coating with Glaze Materials | 64 | ||
3.2.2 Effect of Structural Parameters | 66 | ||
3.2.3 Developing a Catalytic Membrane Reactor | 67 | ||
3.2.4 Experimental Setup | 68 | ||
3.2.4.1 Control Strategies | 71 | ||
3.2.4.2 Experimental Results of the OCM Porous Packed Bed Membrane Reactor | 73 | ||
3.2.4.2.1\rEffect of Methane-to-Oxygen Ratio and Dilution.The methane-to-oxygen ratio is one of the most important factors to be investigat... | 73 | ||
3.2.4.2.2\rEffect of Temperature and Temperature Profile.It is not an exaggeration to claim that thermal engineering remains the main chall... | 74 | ||
3.2.4.3 Hybrid Reactors: Fluidized Bed Membrane Reactor | 75 | ||
3.2.4.4 Hybrid Reactors: Network of Reactors | 76 | ||
3.2.5 Process and Reactor Integration | 77 | ||
3.2.5.1 Integration with Methane Reforming | 77 | ||
3.2.5.2 Dual-membrane Reactors as an Efficient Integrated Reactor Concept | 78 | ||
3.2.5.2.1\rMechanisms, Operation and Practical Issues (Feasibility Study) | 79 | ||
Molten Carbonate Membranes. There are some concerns regarding the design and applicability of the proposed dual-membrane reactor... | 79 | ||
3.2.5.2.2\rTechnical Considerations for the Analysis of the Performance of Integrated Systems.Having considered the advantages of dual-memb... | 80 | ||
3.2.5.3 Alternative Integrated Reactor: OCM and Ethane Dehydrogenation | 81 | ||
3.2.6 Model-based Analysis of OCM Membrane Reactors | 82 | ||
3.2.6.1 Model Validation for Packed Bed Membrane Reactors | 83 | ||
3.2.6.2 Modeling and Analysis of Dual-membrane Reactor Performance | 89 | ||
3.2.6.3 Individual Performance Analysis of Dual-membrane Reactors | 89 | ||
3.2.6.4 Performance of Dual-membrane Reactors in Integrated Processes | 89 | ||
3.2.6.5 CFD Simulation of OCM Membrane Reactors | 91 | ||
3.3 Conclusions and Review of Observations and Results | 91 | ||
Acknowledgements | 92 | ||
References | 92 | ||
Chapter 4 - Ultrathin and Thin Film Pd/Ag Membranes for Hydrogen Production | 95 | ||
4.1 Introduction | 95 | ||
4.2 Development of Thin Film Pd-based Membranes | 97 | ||
4.2.1 Membrane Fabrication Methods | 98 | ||
4.2.2 Supported Membranes for High H2 Flux | 100 | ||
4.2.2.1 Embrittlement and Sulfur Resistant Membranes | 110 | ||
4.2.3 Mechanical, Thermal, and Chemical Stability | 111 | ||
4.2.3.1 Embrittlement and Sulfur Resistant Membranes | 111 | ||
4.2.3.2 Thermal Stability at High Temperature | 115 | ||
4.2.3.3 Wear Resistant Membranes | 117 | ||
4.3 Integration of Pd-based Membranes for Hydrogen Production | 118 | ||
4.3.1 Water–Gas Shift Membrane Reactors | 119 | ||
4.3.2 Steam Methane Reforming Membrane Reactor | 121 | ||
4.3.3 Methanol and Ethanol Reforming Membrane Reactors | 126 | ||
4.4 Conclusions | 129 | ||
Disclosure | 130 | ||
Acknowledgements | 130 | ||
References | 130 | ||
Chapter 5 - Polarization and CO-inhibition in Pd-based Membranes and Membrane Reactors | 139 | ||
5.1 Pd-based Membranes: Overview and Potentialities for Hydrogen Purification | 139 | ||
5.2 Objectives | 141 | ||
5.3 Gas–Surface Interactions for Pd-based Membranes | 141 | ||
5.4 Concentration Polarization in Gas Separation | 142 | ||
5.5 Inhibition by CO in Pd-based Membranes | 144 | ||
5.6 Coupled Effect of Concentration Polarization and Inhibition by CO | 145 | ||
5.6.1 Concentration Polarization Coefficient (CPC) | 146 | ||
5.6.1.1 Overview on the CPC Definition | 146 | ||
5.6.1.2 CPC Based on the Permeation Driving Force | 148 | ||
5.6.1.3 Definition of the CPC in the Presence of Inhibition | 150 | ||
5.6.2 Inhibition Coefficient (IC) | 151 | ||
5.6.3 Overall Permeation Reduction Coefficient13 | 153 | ||
5.6.4 Main Results of the Analysis | 154 | ||
5.6.4.1 Permeance and Flux Analysis | 154 | ||
5.6.4.2 Permeation Reduction Maps | 159 | ||
5.7 Concentration Polarization in Membrane Reactors and Contactors | 163 | ||
5.7.1 Definition of Average CPC | 164 | ||
5.7.2 CPC Profiles by a Pseudo-homogeneous Approach | 165 | ||
5.7.3 CPC Profiles from a CFD Heterogeneous Approach | 167 | ||
5.8 Conclusions | 170 | ||
List of Symbols | 172 | ||
Greek Symbols | 172 | ||
Acronyms | 172 | ||
Acknowledgements | 173 | ||
References | 173 | ||
Chapter 6 - Pd-based Membranes in Hydrogen Production: Long-term Stability and Contaminant Effects | 177 | ||
6.1 Introduction | 177 | ||
6.2 Pd-based Membrane Technology | 180 | ||
6.3 Stability Issues | 181 | ||
6.3.1 Hydrogen Embrittlement | 181 | ||
6.3.2 Structural Stability | 182 | ||
6.3.3 Temperature Stability | 183 | ||
6.3.4 Stability Against Gaseous Contaminants | 185 | ||
6.3.4.1 Carbon Monoxide | 185 | ||
6.3.4.2 Hydrogen Sulphide | 187 | ||
6.3.4.3 Ammonia | 188 | ||
6.3.4.4 Hydrocarbons | 189 | ||
6.3.4.5 Efforts to Reduce the Flux Inhibition by Gaseous Contaminants | 191 | ||
6.3.5 Other Stability Issues | 193 | ||
6.3.6 Regeneration of Deactivated Membranes | 193 | ||
6.4 Applications and Resulting Stability Demands | 194 | ||
6.4.1 Methane Steam Reforming (MSR) | 194 | ||
6.4.2 H2 Production from Gasification of Coal and Biomass | 196 | ||
6.4.3 Water–Gas Shift (WGS) | 197 | ||
6.4.4 Dehydrogenation of Alkanes | 198 | ||
6.4.5 Decomposition of Ammonia | 199 | ||
6.5 Long-term Tests and Results | 200 | ||
6.6 Concluding Remarks | 203 | ||
Acknowledgements | 203 | ||
References | 204 | ||
Chapter 7 - Membrane Processes for Pure Hydrogen Production from Biomass | 212 | ||
7.1 Introduction | 212 | ||
7.2 Membranes for Pure Hydrogen Production | 218 | ||
7.2.1 Metallic Membranes for Hydrogen Separation | 219 | ||
7.2.2 Polymeric Membranes for Hydrogen Separation | 220 | ||
7.2.3 Ceramic Membranes for Hydrogen Separation | 221 | ||
7.2.4 Membranes for High Temperature Applications | 221 | ||
7.2.5 Hydrogen Production in Membrane Reactors: Reforming and Water–Gas Shift | 223 | ||
7.2.5.1 Methane and Biogas Reforming in Membrane Reactors | 223 | ||
7.2.5.2 Ethanol Steam Reforming in Membrane Reactors | 228 | ||
7.2.5.3 Dark Fermentation | 229 | ||
7.2.5.4 Water–Gas Shift in Membrane Reactors | 229 | ||
7.3 Hydrogen Production from Biomass and Integration with Hydrogen Selective Membranes | 233 | ||
7.3.1 Gasification | 234 | ||
7.3.2 Pyrolysis | 236 | ||
7.3.3 Aqueous Phase Reforming (APR) | 237 | ||
7.3.4 Liquid Biofuel and Wastewater | 239 | ||
7.4 Micro-membrane Reactors: Increasing the Area per Volume | 240 | ||
References | 243 | ||
Chapter 8 - Membrane-assisted Syngas Production for Gas-to-Liquid Processes | 247 | ||
8.1 Introduction | 247 | ||
8.2 Pilot Facility | 249 | ||
8.2.1 Process Scheme | 249 | ||
8.2.2 Membrane and Catalyst | 252 | ||
8.2.3 Catalytic Partial Oxidation Reactor | 257 | ||
8.2.4 Operating Conditions | 258 | ||
8.3 Experimental Results | 261 | ||
8.3.1 Low-temperature Steam Reforming Catalyst | 261 | ||
8.3.2 Membrane Modules | 262 | ||
8.3.3 CPO Catalyst | 265 | ||
8.3.4 Overall Configuration Performance for GTL Applications | 268 | ||
8.4 Conclusions | 269 | ||
Acknowledgements | 270 | ||
References | 270 | ||
Chapter 9 - Mixed Ionic–Electronic Conducting Membranes for Hydrogen Separation | 273 | ||
9.1 Introduction | 273 | ||
9.2 Proton Transfer and Membrane Properties | 275 | ||
9.2.1 Transport Properties | 275 | ||
9.2.2 Membrane Properties | 277 | ||
9.3 Materials | 280 | ||
9.3.1 Single-phase Materials | 280 | ||
9.3.1.1 Perovskite Materials | 280 | ||
9.3.1.2 Tungstate-based Materials | 285 | ||
9.3.1.3 Other Materials | 288 | ||
9.3.2 Dual-phase Materials | 290 | ||
9.3.2.1 Cer–Met Composites | 290 | ||
9.3.2.2 Cer–Cer Composites | 294 | ||
9.4 Concluding Remarks and Perspectives | 299 | ||
References | 299 | ||
Chapter 10 - Inorganic Membranes for Gas Separation | 303 | ||
10.1 Introduction | 303 | ||
10.2 Silica Membranes | 306 | ||
10.2.1 Sol–Gel Method | 308 | ||
10.2.2 Chemical Vapor Deposition | 313 | ||
10.2.3 Silica Membranes Prepared from Preceramic Polymers | 316 | ||
10.3 Carbon Molecular Sieve Membranes | 317 | ||
10.3.1 Supported CMS Membranes | 320 | ||
10.3.2 Self-supported CMS Membranes | 324 | ||
10.3.3 Aging of CMS Membranes | 326 | ||
10.4 Zeolite Membranes | 327 | ||
10.4.1 Zeolite Seed Crystal Preparation | 330 | ||
10.4.2 Preparation of Seed Layers | 332 | ||
10.4.3 Seeded Growth for Zeolite Membranes | 333 | ||
10.4.4 Gas–Vapor Separation Using Zeolite Membranes | 334 | ||
10.5 MOF Membranes | 336 | ||
10.5.1 In situ Growth Method | 338 | ||
10.5.2 Seeded Growth Methods | 340 | ||
10.5.3 Gas Separation Using MOF Membranes | 341 | ||
10.6 Conclusions and Outlook | 345 | ||
References | 346 | ||
Subject Index | 358 |