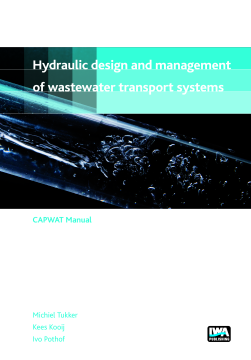
BOOK
Hydraulic design and management of wastewater transport systems
Michiel Tukker | Kees Kooij | Ivo Pothof
(2016)
Additional Information
Book Details
Abstract
Hydraulic Design and Management of Wastewater Transport Systems is a manual resulting from the research project CAPWAT (CAPacity loss in wasteWATer pressure pipelines), which researched the mechanisms for the creation, stagnation and discharge of gas bubbles in wastewater pressure pipelines. During this six-year research programme, it was recognised that there is no hydraulic manual/guideline that focuses on the entire wastewater pressure pipeline system, the processes it includes, and the interaction between the pressure pipeline and the pumping station.
This manual provides a compilation of all the hydraulic knowledge that is necessary for designing a wastewater transport system and to manage it operationally. The wastewater transport system is the link between the collection and treatment of the wastewater and the collection system includes, among others, the gravity flow sewage system from the house (or consumer) and service connection through street and main sewers up to the suction basins. The transport system, for which this manual was written, includes the suction basin, the sewage pumping station and the pressure pipelines.
Wastewater transport systems are becoming more complex due to building larger sewage water treatment plants, wastewater being transported over greater distances and increasingly more (and smaller) pipelines connecting to the main sewers. The operation of the pumping stations is largely determined by how the entire system behaves. Insight into this operation is, therefore, crucial for proper design and management.
The central point of the design is to create an independent and safe system with the necessary transport capacity at minimum societal costs. Predominantly, the management aspect focuses on guidelines to maintain the design principles regarding capacity and required energy.
Table of Contents
Section Title | Page | Action | Price |
---|---|---|---|
Cover | Cover | ||
Table of Contents | v | ||
List of symbols | ix | ||
About this Manual | xiii | ||
Chapter 1: Foreword | 1 | ||
1.1 NECESSITY OF THE MANUAL | 1 | ||
1.2 SCOPE OF THE MANUAL | 2 | ||
1.3 AUTHORS AND EDITORIAL STAFF | 4 | ||
1.4 READER’S GUIDE | 4 | ||
Chapter 2: Designing wastewater transportation systems | 5 | ||
Chapter 3: Pipeline design | 7 | ||
3.1 BOUNDARY CONDITIONS | 7 | ||
3.1.1 Flow rates | 7 | ||
3.1.2 Choice of route | 9 | ||
3.2 DETERMINING THE DIMENSIONS OF THE MAIN | 9 | ||
3.2.1 Profile of the pipeline | 10 | ||
3.2.2 Diameter | 12 | ||
3.2.3 Wall roughness | 14 | ||
3.2.4 Pipeline material | 14 | ||
3.3 CROSSINGS | 15 | ||
3.4 ARRANGEMENTS FOR THE PREVENTION AND REMOVAL OF GAS BUBBLES | 18 | ||
3.4.1 Reduce the diameter locally | 18 | ||
3.4.2 Air-release valve | 19 | ||
3.5 NETWORK SYSTEMS | 20 | ||
Chapter 4: Designing the pumping station | 21 | ||
4.1 BOUNDARY CONDITIONS | 21 | ||
4.1.1 Required capacity | 21 | ||
4.1.2 Pump head | 22 | ||
4.1.3 Operational safety | 23 | ||
4.2 PUMP SET-UP | 23 | ||
4.2.1 Wet or dry set-up | 23 | ||
4.2.2 Number of pumps | 24 | ||
4.2.3 Vertical or horizontal set-up | 24 | ||
4.3 COMPONENTS | 25 | ||
4.3.1 Shut-off valves | 25 | ||
4.3.2 Check valve | 25 | ||
4.4 DETERMINING THE OPERATING RANGE AND SELECTING THE PUMP | 27 | ||
4.5 RECEIVING BASIN | 27 | ||
4.5.1 Storage of the receiving basin | 28 | ||
4.5.2 Preventing air entry | 29 | ||
4.5.3 Sediment discharge and approaching flow of the pump | 30 | ||
4.6 DESIGN OF AIR VALVES | 31 | ||
Chapter 5: Dynamic effects | 33 | ||
5.1 BASIC ASSUMPTIONS | 34 | ||
5.1.1 Allowable maximum and minimum pressures | 35 | ||
5.1.2 Hydraulic model | 36 | ||
5.2 WATER HAMMER ANALYSIS WITHOUT SURGE PROTECTIONS | 37 | ||
5.3 INVENTORY OF SOLUTIONS FOR PREVENTING IMPERMISSIBLE PRESSURES | 38 | ||
Option 1 | 38 | ||
Option 2 | 38 | ||
Option 3 | 38 | ||
Option 4 | 40 | ||
5.4 DIMENSIONING WATER HAMMER SURGE PROTECTIONS | 40 | ||
5.5 NORMAL AND INCIDENTAL OPERATIONS | 41 | ||
Chapter 6: Design aspects for maintaining capacity | 43 | ||
6.1 PERFORMANCE INDICATORS | 43 | ||
6.1.1 Operating hours | 44 | ||
6.1.2 Specific energy consumption | 45 | ||
Short time scale (in the order of minutes) | 46 | ||
Long time scale (in the order of weeks/months) | 47 | ||
6.1.3 System and pump characteristics | 47 | ||
6.1.4 Equivalent wall roughness | 48 | ||
6.2 MEASURING LOCATIONS FOR PRESSURE AND FLOW RATE | 49 | ||
6.2.1 Flow rate measurement | 49 | ||
6.2.2 Pressure measurement | 50 | ||
6.2.3 Pump data | 51 | ||
6.3 PROVISIONS FOR MAINTAINING CAPACITY | 51 | ||
6.3.1 Valves | 51 | ||
6.3.2 Increased flow speed | 51 | ||
6.3.3 Pigging | 52 | ||
6.3.4 Air valve locations | 53 | ||
Chapter 7: Review of the overall system design | 55 | ||
7.1 CONTROLLING THE AIR IN PRESSURE PIPELINES | 55 | ||
7.2 CHECK LISTS | 57 | ||
7.2.1 Pumping station design | 57 | ||
7.2.2 Design of pressure pipelines | 57 | ||
7.2.3 Surge protection design | 58 | ||
Chapter 8: Commissioning of the system | 59 | ||
8.1 BOUNDARY CONDITIONS | 59 | ||
8.2 DRAFTING AN ACCEPTANCE TEST PLAN | 59 | ||
8.2.1 Preparations | 61 | ||
8.2.2 Leakage-proof and gas-proof pipeline system | 61 | ||
8.2.3 Pump capacity | 61 | ||
8.2.4 Check valve | 61 | ||
8.2.5 Pipeline capacity | 62 | ||
8.2.6 Controlling the pumping station | 62 | ||
8.2.7 Dynamic measurements | 62 | ||
Water hammer surge protections | 63 | ||
Dynamic characteristics | 63 | ||
8.3 BENCHMARK TESTING | 63 | ||
Chapter 9: Maintaining hydraulic capacity | 65 | ||
9.1 MEASUREMENTS IN WASTEWATER TRANSPORT SYSTEMS | 65 | ||
9.1.1 Parameters and locations | 66 | ||
9.1.2 Instrumentation | 66 | ||
9.1.3 Measuring strategy | 67 | ||
9.1.4 Implementing field measurements | 67 | ||
9.2 CRITERIA FOR CAPACITY REDUCTION | 68 | ||
9.3 ANALYSIS OF A CAPACITY PROBLEM | 69 | ||
9.3.1 Localising the problem | 69 | ||
9.3.2 Analysis of the pumping station | 71 | ||
9.3.3 Analysis of the pressure pipeline | 71 | ||
9.3.4 Follow-up maintenance for capacity problems | 74 | ||
Chapter 10: References | 75 | ||
Appendix A: Theoretical background | A-1 | ||
A.1 CHARACTERISTICS OF DRINKING WATER | A-1 | ||
A.1.1 Density | A-1 | ||
A.1.2 Viscosity | A-1 | ||
A.1.3 Compressibility modulus | A-2 | ||
A.1.4 Surface tension | A-3 | ||
A.1.5 Vapour pressure | A-4 | ||
A.2 BASIC EQUATIONS | A-4 | ||
A.2.1 Reynolds number | A-4 | ||
A.2.2 Bernoulli’s principle | A-5 | ||
A.3 TRANSPORT LOSSES | A-6 | ||
A.3.1 Pipe friction losses | A-6 | ||
A.3.2 Local losses | A-9 | ||
Inlet losses | A-9 | ||
Outlet losses | A-10 | ||
Bend losses | A-10 | ||
Elbow losses | A-12 | ||
Losses due to contraction and expansion of the pipe | A-12 | ||
A.4 RECEIVING BASINS AND INLET STRUCTURES | A-13 | ||
A.4.1 Rules of thumb for the design of receiving basins | A-13 | ||
A.4.1.1 Bottom clearance | A-13 | ||
A.4.1.2 Backwall distance | A-14 | ||
A.4.1.3 Width of the pump compartment | A-14 | ||
A.4.1.4 Length of the pump compartment | A-14 | ||
A.4.1.5 Inclined walls (side walls/floor) | A-14 | ||
A.4.1.6 Submergence depth | A-14 | ||
A.4.1.7 Summary of the rules of thumb | A-17 | ||
A.4.2 Air entrainment in pump basins | A-19 | ||
A.4.3 Measures against air entrainment | A-21 | ||
A.5 PUMPS IN PIPELINE SYSTEMS | A-24 | ||
A.5.1 System characteristics and operating point | A-24 | ||
A.5.2 Changes in the operating point due to fluctuation in the static pump head | A-24 | ||
A.5.3 Changes in the operating point due to fluctuating transport losses | A-25 | ||
A.5.4 Comparing various pumps | A-26 | ||
A.5.5 Parallel and serial operation of pumps | A-26 | ||
A.5.6 Changes in pump speed | A-28 | ||
A.6 VALVES | A-28 | ||
A.6.1 Shut-off valves | A-28 | ||
A.6.2 Valve characteristics | A-29 | ||
A.6.3 Check valves | A-31 | ||
A.6.4 Characterising check valves | A-33 | ||
A.7 WATER HAMMER IN PIPELINE SYSTEMS | A-36 | ||
A.7.1 Propagation speed | A-37 | ||
A.7.2 Reflection time | A-38 | ||
A.7.3 Joukowsky’s Law | A-39 | ||
A.7.4 Allowed pressure in synthetic pipelines | A-39 | ||
A.7.5 Surge vessel as water hammer surge protection | A-40 | ||
A.7.6 Surge tower as water hammer surge protection | A-42 | ||
A.7.7 Bypass as water hammer surge protection | A-43 | ||
A.7.8 Air valve as water hammer surge protection | A-43 | ||
A.8 GAS BUBBLES IN PIPELINES | A-44 | ||
A.8.1 Transport mechanisms | A-44 | ||
A.8.2 Velocity criterion | A-46 | ||
A.8.3 Calculation model for gas transport | A-48 | ||
Air transport in the plug-flow regime | A-49 | ||
Air transport model in the blowback flow regime | A-50 | ||
A.8.4 Catching gas | A-52 | ||
A.8.5 Release of gas by negative pressure | A-53 | ||
Appendix B: Description of gas bubble detection methods | B-1 | ||
B.1 FLOW RATE PATTERN DURING A PUMP START | B-1 | ||
B.2 PRESSURE CHANGE AFTER DRAINING | B-2 | ||
B.3 DYNAMIC MEASUREMENTS | B-3 |