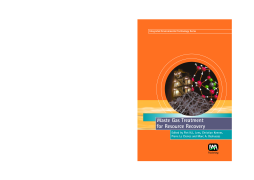
BOOK
Waste Gas Treatment for Resource Recovery
Piet Lens | C. Kennes | P. le Cloirec | M. Deshusses
(2006)
Additional Information
Book Details
Abstract
The prevention of over-exploitation and the efficient use of natural resources are key goals of environmental managment in Industry. Waste Gas Treatment for Resource Recovery presents the reader with technical, ecological and economical aspects of gaseous effluent treatment and resource recovery. Practical experience from industry and agriculture is presented, the role of newly developed advanced technology in future recycling of gas streams discussed and attention given to criteria for sustainability in gas treatment. Detailed analysis of material flows, novel process applications and bioreactor designs, odour quantification and removal process techniques and European legislations for waste gas discharge and recovery are highlights of the extensive and comprehensive coverage of this book. Waste Gas Treatment for Resource Recovery will enable production, process and environmental engineers and managers to evaluate internal recycling possibilities, which contribute to an economically and environmentally friendly manufacturing processes with reduced pollution loads and waste gas volumes. Analysis of material flows, e.g. the development of methodologies and techniques to monitor the use and flow of materials on a life cycle basis Novel process applications and bioreactor designs for resource recovery from waste gases Odour quantification techniques and novel odour removal processes European dimension of polluted gas streams and the European legislation for waste gas discharges and recovery
Table of Contents
Section Title | Page | Action | Price |
---|---|---|---|
Cover\r | Cover | ||
Contents | v | ||
Preface | xiii | ||
Contributors | xv | ||
PART I: Socio-economic aspects of gas pollution and gas recovery | 1 | ||
1 Introduction on air pollution: the emission–effect relation | 3 | ||
1.1 INTRODUCTION: WHAT IS AIR POLLUTION? | 3 | ||
1.2 OVERVIEW OF THE EMISSION EFFECT RELATIONS | 6 | ||
1.3 EMISSIONS | 7 | ||
1.4 FORMATION OF AEROSOLS | 9 | ||
1.5 LIFETIMES OF POLLUTANTS | 10 | ||
1.6 AMBIENT CONCENTRATION OF POLLUTANTS | 11 | ||
1.7 CONCLUSION | 12 | ||
REFERENCES | 12 | ||
2 Transboundary particulate matter pollution in Europe | 13 | ||
2.1 INTRODUCTION\r | 13 | ||
2.1.1 Airborne particulate matter | 13 | ||
2.1.2 PM size distribution | 14 | ||
2.1.3 PM chemical composition | 14 | ||
2.2 EUROPEAN AEROSOL PATTERNS AND TRENDS\r | 16 | ||
2.2.1 Aerosol monitoring | 16 | ||
2.2.2 Composition of non-urban aerosol | 17 | ||
2.2.3 Urban European aerosol pattern | 17 | ||
2.3 AIR POLLUTION OBSERVATION: EXISTING NETWORKS\r | 19 | ||
2.3.1 European Monitoring and Evaluation Programme | 19 | ||
2.3.2 Global Atmosphere Watch | 21 | ||
2.3.3 EuroAirnet | 23 | ||
2.4 MODELLING AMBIENT PM TRANSPORT\r | 23 | ||
2.4.1 Air quality modelling | 23 | ||
2.4.2 Model application | 24 | ||
2.4.3 Air quality software | 25 | ||
2.4.3.1 Mesoscale models | 25 | ||
2.4.3.2 Long-range transport models | 26 | ||
2.5 CONCLUSIONS | 26 | ||
REFERENCES | 26 | ||
3 Abatement strategies for air pollution | 30 | ||
3.1 INTRODUCTION | 30 | ||
3.2 ORIGIN AND FATE OF EMISSIONS\r | 31 | ||
3.2.1 Emission sources and transport to receptors | 31 | ||
3.2.2 Transport scales and pollutant interaction | 32 | ||
3.3 ABATEMENT STRATEGIES\r | 34 | ||
3.3.1 High chimneys | 34 | ||
3.3.2 International protocols for emission control | 35 | ||
3.3.3 Multi-pollutants/multi-effects approach | 36 | ||
3.3.4 Top-down and bottom-up approaches | 37 | ||
3.3.5 Decision aid by integrated optimising modelling | 38 | ||
3.3.6 Flexible instruments | 39 | ||
3.4 OUTLOOK | 40 | ||
REFERENCES | 41 | ||
4 Dealing with waste gas in enhancing sustainable development: the role of the Kyoto mechanisms | 43 | ||
4.1 INTRODUCTION | 43 | ||
4.2 DEFINING SUSTAINABLE DEVELOPMENT | 44 | ||
4.3 WASTE GAS RECOVERY UNDER THE CDM | 46 | ||
4.3.1 Biogas | 48 | ||
4.3.2 Landfill gas | 50 | ||
4.3.3 Fugitive emissions | 51 | ||
4.3.4 Coal mine/bed methane | 52 | ||
4.4 KYOTO-BASED CASE STUDIES OF WASTE GAS CAPTURE PROJECTS | 53 | ||
4.4.1 Solid waste management in Latvia | 53 | ||
4.4.2 Salvador da Bahia landfill, Brazil | 54 | ||
4.4.3 Coal-mine methane power generation project in China | 56 | ||
4.4.4 Sustainable development through waste gas reuse | 57 | ||
4.5 CONCLUSIONS | 58 | ||
REFERENCES | 58 | ||
5 Implementation of the European Solvent Directive (1999/13/EC) | 60 | ||
5.1 INTRODUCTION | 60 | ||
5.2 INFORMATION EXCHANGE PLATFORM AS A PART OF THE IMPLEMENTATION OF THE EU SOLVENT DIRECTIVE | 61 | ||
5.2.1 Development of the internet-based information exchange platform | 61 | ||
5.2.2 Conclusions from the implementation of the information exchange platform | 63 | ||
5.3 DECISION SUPPORT THROUGH MASS AND ENERGY FLOW MANAGEMENT IN THE SECTOR OF VEHICLE REFINISHING | 64 | ||
5.3.1 VOC emission reduction measures in the vehicle refinishing sector | 65 | ||
5.3.2 Development of the process model | 66 | ||
5.3.3 Development of the software model IMPROVE | 67 | ||
5.3.4 Techno-economic evaluation of the material flow network | 68 | ||
5.3.4.1 Material flows | 68 | ||
5.3.4.2 Energy flows | 68 | ||
5.3.4.3 Economic analysis | 69 | ||
5.3.5 Model customization | 69 | ||
5.4 FURTHER USE OF MASS AND ENERGY FLOW MODELS | 69 | ||
5.4.1 Development of a practical guideline for the introduction and use of water-based coatings in smalland medium-sized car refinishing\rbody shops | 70 | ||
5.4.2 Solvent management plan according to the EU Solvent Directive (1999/13/EC) | 71 | ||
5.4.3 Linking IMPROVE with time management | 72 | ||
5.5 CONCLUSION | 72 | ||
ACKNOWLEDGMENTS | 73 | ||
REFERENCES | 73 | ||
6 Integration of biological techniques for air pollution control into sustainable development | 76 | ||
6.1 INTRODUCTION\r | 76 | ||
6.1.1 Biological techniques for air pollution control | 76 | ||
6.1.2 Sustainable development | 77 | ||
6.1.3 Technology selection for sustainable development | 77 | ||
6.2 VOC CONTROL, THE CASE FOR AVOIDING UNNECESSARY CO2 EMISSIONS | 78 | ||
6.3 HIGH-RATE BIOTRICKLING FILTERS FOR H2S CONTROL | 80 | ||
6.4 CONCLUDING REMARKS | 82 | ||
REFERENCES | 82 | ||
PART II: Characterization of waste gases | 85 | ||
7 Characterization of pollutants in gases | 87 | ||
7.1 INTRODUCTION | 87 | ||
7.2 CHARACTERIZING ATMOSPHERIC POLLUTANTS | 88 | ||
7.2.1 Composition of the atmosphere | 88 | ||
7.2.2 Concentration units | 89 | ||
7.2.3 Sources of trace gases | 90 | ||
7.2.4 Particles | 91 | ||
7.2.5 Atmospheric chemistry | 92 | ||
7.2.6 Removal of atmospheric gases from the atmosphere | 93 | ||
7.3 MONITORING AND ANALYSIS | 94 | ||
7.3.1 Sampling | 95 | ||
7.3.2 Analytical methods | 95 | ||
7.3.2.1 Optical methods | 95 | ||
7.3.2.2 Indicative methods | 96 | ||
7.3.2.3 Sulfur dioxide | 97 | ||
7.3.2.4 Nitrogen oxides and ammonia | 97 | ||
7.3.2.5 Hydrocarbons | 98 | ||
7.3.2.6 Ozone | 98 | ||
7.3.2.7 Carbon monoxide | 98 | ||
7.3.2.8 Particulate material | 98 | ||
7.4 EFFECTS | 99 | ||
7.4.1 Health | 99 | ||
7.4.2 Material effects | 101 | ||
7.4.3 Ecological and agricultural effects | 102 | ||
7.4.4 Acid rain and climate change | 102 | ||
7.4.5 Odour and other issues | 102 | ||
7.5 CONCLUSIONS | 103 | ||
REFERENCES | 104 | ||
8 Isotope characterization of gaseous pollutants | 107 | ||
8.1 INTRODUCTION\r | 107 | ||
8.1.1 Identification of sources of emissions | 107 | ||
8.1.2 Isotopes | 108 | ||
8.1.2.1 Carbon | 108 | ||
8.1.2.2 Sulfur | 108 | ||
8.1.2.3 Oxygen | 109 | ||
8.2 ISOTOPE ABUNDANCE VARIATIONS\r | 109 | ||
8.2.1 Natural carbon isotope abundance variations | 109 | ||
8.2.2 Natural oxygen isotope abundance variations | 109 | ||
8.2.3 Natural sulfur isotope abundance variations | 110 | ||
8.3 ISOTOPE MASS BALANCE\r | 110 | ||
8.3.1 Two source mixing | 110 | ||
8.3.2 Multiple source mixing | 111 | ||
8.3.3 Source apportionment using C and O isotopes | 113 | ||
8.3.4 Compound-specific carbon isotope analysis | 114 | ||
8.4 CONCLUSION | 115 | ||
REFERENCES | 115 | ||
9 Use of NMR to study in situ bioconversion of gaseous formaldehyde\r | 117 | ||
9.1 INTRODUCTION | 117 | ||
9.2 IN SITU NMR STUDY OF BIOCONVERSION OF GASEOUS COMPOUNDS\r | 118 | ||
9.2.1 Generalities | 118 | ||
9.2.2 1H NMR studies\r | 119 | ||
9.2.3 13C NMR studies\r | 120 | ||
9.2.4 Deuterium NMR studies | 121 | ||
9.3 NMR STUDY OF FORMALDEHYDE BIOCONVERSION | 122 | ||
9.3.1 Identification of formaldehyde metabolites via routes I and II | 122 | ||
9.3.2 Synthesis of formate by GSH-formaldehyde dehydrogenase activity (route I) | 123 | ||
9.3.3 Formation of methanol and formate by NADH-oxidoreductase and dismutase (“Cannizzarase”) activities (routes I and II) | 124 | ||
9.3.4 Formation of methylformate (route III) | 126 | ||
9.3.5 Dissimilation of formaldehyde via the RuMP cycle (route IV) | 127 | ||
9.3.6 Transformation of formaldehyde on solid supports | 128 | ||
9.4 CONCLUSION | 130 | ||
REFERENCES | 130 | ||
10 Heavy metal release in waste incineration processes | 132 | ||
10.1 INTRODUCTION\r | 132 | ||
10.1.1 Fate of heavy metals during waste incineration | 132 | ||
10.1.2 Aim of the study | 133 | ||
10.2 THERMODYNAMIC STUDY | 134 | ||
10.2.1 Equilibrium calculation method | 134 | ||
10.2.2 System definition and calculation conditions | 135 | ||
10.2.3 Results of the theoretical study | 135 | ||
10.2.3.1 Influence of temperature on the HM speciation | 136 | ||
10.2.3.2 Effect of the oxygen content on the HM speciation | 137 | ||
10.2.3.3 Influence of the chlorine content on the HM speciation | 138 | ||
10.3 CHARACTERISATION OF ULTIMATE RESIDUES | 139 | ||
10.3.1 Characterisation techniques | 139 | ||
10.3.2 HM speciation in residue | 140 | ||
10.4 KINETICS OF HM VAPORISATION | 141 | ||
10.4.1 Experimental study | 141 | ||
10.4.1.1 Lab-scale reactor | 141 | ||
10.4.1.2 On-line gas analysis system | 141 | ||
10.4.1.3 Model wastes | 142 | ||
10.4.2 Theoretical study | 143 | ||
10.4.2.1 Method | 143 | ||
10.4.2.2 Direct model | 143 | ||
10.4.2.3 Inverse model | 144 | ||
10.4.3 Determination of the metal vaporisation kinetics | 145 | ||
10.4.3.1 Validation of the method with alumina matrix | 145 | ||
10.4.3.2 Application to RAW | 146 | ||
10.5 CONCLUSION | 148 | ||
ACKNOWLEDGEMENTS | 148 | ||
REFERENCES | 148 | ||
11 Functional interpretation of gas composition | 150 | ||
11.1 INTRODUCTION | 150 | ||
11.2 SOURCES OF VOLATILE ORGANIC COMPOUNDS\r | 151 | ||
11.2.1 NMVOCs emissions | 151 | ||
11.2.2 Biochemistry of the anaerobic environment | 152 | ||
11.3 ANALYSIS OF NMVOCS | 154 | ||
11.3.1 Concentrating the sample | 155 | ||
11.3.2 Gas chromatography | 156 | ||
11.3.3 Mass spectrometry | 156 | ||
11.4 NMVOC EMISSION RATES\r | 157 | ||
11.4.1 Determination of emission rates | 157 | ||
11.4.2 Physical factors affecting emission rates | 157 | ||
11.4.2.1 Effects of wind speed | 157 | ||
11.4.2.2 Henry’s law | 158 | ||
11.4.2.3 Effect of pH on gas concentration in the headspace | 158 | ||
11.4.2.4 Non-ideal Henry’s law conditions | 158 | ||
11.5 DIFFERENTIATING PROCESSES USING THE NMVOC PROFILE | 159 | ||
11.5.1 Composting | 160 | ||
11.5.1.1 Composting processes | 160 | ||
11.5.1.2 The effect of different substrates | 161 | ||
11.5.2 Sewage sludge cake | 162 | ||
11.5.3 Differentiating dietary intake | 164 | ||
11.6 CONCLUSION | 165 | ||
REFERENCES | 166 | ||
12 Biomarkers of air pollution | 168 | ||
12.1 INTRODUCTION\r | 168 | ||
12.1.1 Air pollution and health | 168 | ||
12.1.2 Biomarker categories | 170 | ||
12.2 THE IDEAL BIOMARKER\r | 170 | ||
12.2.1 Criteria for biomarkers | 170 | ||
12.2.2 Biomarker validation | 171 | ||
12.2.3 Legal implications | 171 | ||
12.3 DIVERSITY OF POLLUTANTS AND BIOMARKERS | 173 | ||
12.4 EXPOSURE BIOMARKERS\r | 174 | ||
12.4.1 Exposure biomarkers in environmental medicine | 174 | ||
12.4.2 Illustrative examples | 175 | ||
12.4.2.1 Carbon monoxide and tobacco smoke | 175 | ||
12.4.2.2 Benzene | 176 | ||
12.4.2.3 1,3-Butadiene | 176 | ||
12.4.2.4 Polycyclic aromatic hydrocarbons | 177 | ||
12.4.2.5 Ozone | 177 | ||
12.4.2.6 Sulfur dioxide | 177 | ||
12.4.2.7 Nitrogen dioxide | 177 | ||
12.4.2.8 Particulate matter | 178 | ||
12.5 BIOMARKERS OF EFFECTS | 178 | ||
12.5.1 The pneumoproteinaemia concept | 178 | ||
12.5.2 Markers of airway inflammation such as exhaled NO | 180 | ||
12.5.3 Markers of oxidative stress | 181 | ||
12.5.3.1 Oxidative stress using PM as an example | 181 | ||
12.5.3.2 Biomarkers of oxidative stress | 182 | ||
12.5.4 Other cellular effects and immunotoxicity | 183 | ||
12.5.5 Biomarkers of air pollution in organs other than lung | 184 | ||
12.5.5.1 The kidney | 184 | ||
12.5.5.2 The central nervous system | 184 | ||
12.5.5.3 The liver | 185 | ||
12.6 BIOMARKERS OF SUSCEPTIBILITY | 186 | ||
12.7 CONCLUSION | 187 | ||
REFERENCES | 187 | ||
PART III: Bioreactors for waste gas cleaning | 193 | ||
13 Gas purification by heterogeneous photocatalysis | 195 | ||
13.1 INTRODUCTION | 195 | ||
13.2 GAS-PHASE PHOTOCATALYTIC DEGRADATION OF POLLUTANTS | 197 | ||
13.2.1 Background and controversy | 198 | ||
13.2.2 Photocatalysis of selected compounds | 201 | ||
13.2.2.1 Alcohols, aldehydes, ketones, acids and olefins | 201 | ||
13.2.2.2 Aromatic compounds | 203 | ||
13.2.2.3 Compounds with heteroatoms (halogens, nitrogen and sulfur) | 204 | ||
13.2.2.4 Inorganic species | 208 | ||
13.2.3 Process improvements | 209 | ||
13.2.3.1 Use of modified catalysts | 209 | ||
13.2.3.2 Periodic illumination | 210 | ||
13.2.3.3 Addition of ozone | 210 | ||
13.2.4 Effect of water and temperature | 211 | ||
13.2.4.1 Water | 211 | ||
13.2.4.2 Temperature | 211 | ||
13.2.5 Behavior of mixtures | 212 | ||
13.2.6 Deactivation of the photocatalyst | 212 | ||
13.3 POTENTIAL APPLICATIONS\r | 215 | ||
13.3.1 Treatment of air in building interiors | 215 | ||
13.3.2 Industry | 216 | ||
13.3.3 Exteriors | 216 | ||
13.3.4 Disinfection | 216 | ||
13.3.5 Odor treatment | 217 | ||
13.3.6 Passive treatment of architectural elements: self-cleaning materials | 217 | ||
13.3.7 Treatment of polluted soil and water | 218 | ||
REFERENCES | 219 | ||
14 Removal of airborne particulate matter | 226 | ||
14.1 INTRODUCTION | 226 | ||
14.2 DEFINITION – PARTICULATE POLLUTANT SOURCES AND IMPACTS | 227 | ||
14.2.1 Origin of air pollutant particles | 228 | ||
14.2.2 Structure and physico-chemical properties | 229 | ||
14.2.2.1 Size, shape and density of particles | 229 | ||
14.2.2.2 Influence of particle composition | 229 | ||
14.2.2.3 Influence of electrical resistivity and surface charge | 229 | ||
14.2.3 Noxious effects on health and the environment | 230 | ||
14.2.3.1 Effect on human health | 230 | ||
14.2.3.2 Impact on the environment | 230 | ||
14.3 MEASUREMENT OF PARTICLE SIZE DISTRIBUTION AND CONCENTRATION | 231 | ||
14.4 AIRBORNE PARTICLE TRANSPORT – THEORETICAL APPROACHES | 231 | ||
14.4.1 Particle falling velocity | 233 | ||
14.4.2 Forces acting on particles in a moving fluid | 234 | ||
14.4.3 Sphericity correction | 235 | ||
14.4.4 Influence of particle concentration | 235 | ||
14.5 AIRBORNE PARTICLE TREATMENT SYSTEMS | 235 | ||
14.5.1 Fibrous filter media | 235 | ||
14.5.1.1 Operating conditions and principles | 236 | ||
14.5.1.2 Design of filters | 237 | ||
14.5.1.3 Filtration efficiency | 240 | ||
14.5.1.4 Qualification of filter | 242 | ||
14.5.2 Cyclones | 243 | ||
14.5.2.1 Operation principle | 243 | ||
14.5.2.2 Operating conditions | 243 | ||
14.5.2.3 Design | 244 | ||
14.5.3 Electrostatic precipitators | 244 | ||
14.5.3.1 ESP operation | 244 | ||
14.5.3.2 ESP design | 245 | ||
14.5.4 Wet scrubbers | 245 | ||
14.5.5 Comparison | 246 | ||
14.6 EXAMPLES OF INDUSTRIAL APPLICATIONS | 246 | ||
14.6.1 Industrial effluent gas treatment | 246 | ||
14.6.2 Indoor air treatment | 246 | ||
14.6.2.1 Airborne particle treatment processes classified according to application | 247 | ||
14.6.2.2 Process intensification: combined treatment of inert particles and microbial aerosols/VOCs and odours | 247 | ||
14.7 CONCLUSION | 247 | ||
REFERENCES | 248 | ||
15 Bioprocess engineering aspects of biological waste gas treatments | 250 | ||
15.1 INTRODUCTION | 250 | ||
15.2 WASTE GAS TREATMENT PROCESSES\r | 251 | ||
15.2.1 Air treatment processes | 251 | ||
15.2.2 Biological treatments of waste gases (Le Cloirec et al., 2005) | 251 | ||
15.3 BIOFILTERS\r | 251 | ||
15.3.1 General presentation of the process | 251 | ||
15.3.2 Practical operating conditions and performances | 253 | ||
15.3.3 Modeling a biofilter | 257 | ||
15.3.3.1 Ottengraf’s model | 257 | ||
15.3.4 An example of biofiltration performances and modeling | 262 | ||
15.4 BIOTRICKLING FILTERS\r | 265 | ||
15.4.1 Principle, operating conditions and performance | 265 | ||
15.4.2 Modeling a biotrickling filter | 265 | ||
15.5 BIOSCRUBBERS\r | 267 | ||
15.5.1 Presentation of the process | 267 | ||
15.5.2 Practical operating conditions and performance | 268 | ||
15.5.3 Modeling | 268 | ||
15.5.3.1 Model description | 268 | ||
15.5.3.2 Comparison of experimental and computed results | 272 | ||
15.5.3.3 Influence of the biodegradation step on the deodorization efficiency | 273 | ||
15.6 CONCLUSIONS | 274 | ||
ACKNOWLEDGMENTS | 274 | ||
REFERENCES | 274 | ||
16 Fungal and dechlorinating biocatalysts in waste gas treatment | 277 | ||
16.1 INTRODUCTION | 277 | ||
16.2 FUNGAL ACTIVITIES USED IN GAS-PHASE BIOREACTORS\r | 278 | ||
16.2.1 Introduction | 278 | ||
16.2.2 VOC-degrading fungi | 278 | ||
16.2.3 Fungal gas-phase bioreactors | 281 | ||
16.2.3.1 Water content | 282 | ||
16.2.3.2 pH | 282 | ||
16.2.3.3 Pressure drop | 283 | ||
16.3 DECHLORINATING BIOCATALYSTS\r | 284 | ||
16.3.1 Chlorinated compounds and air pollution | 284 | ||
16.3.2 Removal of chlorinated compounds from air in bioreactors | 285 | ||
16.3.2.1 Introduction | 285 | ||
16.3.2.2 Aerobic dechlorination of DCM | 286 | ||
16.3.2.3 Aerobic dechlorination of chlorobenzenes | 289 | ||
16.3.2.4 Aerobic dechlorination of TCE | 291 | ||
16.3.2.5 Anaerobic dechlorination of highly chlorinated pollutants | 296 | ||
16.4 OTHER BIOCATALYTIC ACTIVITIES RECENTLY STUDIED IN GAS-PHASE BIOREACTORS | 297 | ||
16.5 CONCLUSIONS | 297 | ||
ACKNOWLEDGEMENT | 298 | ||
REFERENCES | 298 | ||
PART IV: Technologies for resource recovery | 303 | ||
17\rWet scrubbing for the removal of NH3 from waste gases | 305 | ||
17.1 INTRODUCTION | 305 | ||
17.2 CHOICE OF SOLVENTS FOR ABSORPTION | 306 | ||
17.3 FUNDAMENTALS OF MASS TRANSFER\r | 307 | ||
17.3.1 Physical absorption | 307 | ||
17.3.2 Absorption associated with an irreversible chemical reaction | 308 | ||
17.4 WET SCRUBBING TECHNOLOGIES | 310 | ||
17.4.1 Packed tower | 310 | ||
17.4.1.1 Operating principle | 310 | ||
17.4.1.2 Packing material | 311 | ||
17.4.2 Spray column | 312 | ||
17.5 DESIGN OF PACKED AND SPRAY COLUMNS | 312 | ||
17.5.1 Physical absorption | 312 | ||
17.5.1.1 Design equation | 312 | ||
17.5.1.2 Packed column | 314 | ||
17.5.1.3 Spray column | 314 | ||
17.5.2 Absorption with an irreversible chemical reaction | 315 | ||
17.5.2.1 Design equations | 315 | ||
17.5.2.2 Packed column | 316 | ||
17.5.2.3 Spray column | 316 | ||
17.6 EXAMPLES OF DESIGN\r | 317 | ||
17.6.1 Absorption of NH3 by water in a packed tower | 317 | ||
17.6.2 Absorption of NH3 by a dilute acid solution in a packed tower | 317 | ||
17.6.3 Absorption of NH3 by a dilute acid solution in a spray column | 318 | ||
17.7 CONCLUSIONS | 318 | ||
REFERENCES | 319 | ||
18 CO2 capture in energy production | 320 | ||
18.1 INTRODUCTION | 320 | ||
18.2 ABSORPTION\r | 321 | ||
18.2.1 Working principle | 321 | ||
18.2.2 Use of monoethanolamine as a solvent | 321 | ||
18.2.3 FGD product recycling | 322 | ||
18.2.4 Advantages and disadvantages for absorption | 323 | ||
18.2.5 Process improvements | 323 | ||
18.2.5.1 New solvents | 323 | ||
18.2.5.2 New equipment configuration | 324 | ||
18.2.5.3 Other possible improvements to absorption | 325 | ||
18.3 ADSORPTION\r | 326 | ||
18.3.1 Working principle | 326 | ||
18.3.2 Process improvements | 326 | ||
18.3.2.1 Electrical desorption | 326 | ||
18.3.2.2 Hydrotalcite and water–gas shift | 327 | ||
18.3.3 Advantages and disadvantages for adsorption | 327 | ||
18.4 CRYOGENIC DISTILLATION\r | 328 | ||
18.4.1 Working principle | 328 | ||
18.4.2 Advantages and disadvantages for cryogenic distillation | 328 | ||
18.5 MEMBRANE SEPARATIONS\r | 329 | ||
18.5.1 Working principle | 329 | ||
18.5.2 Advantages and disadvantages for membrane diffusion | 330 | ||
18.6 CO2 PRECIPITATION\r | 331 | ||
18.6.1 Hydrate formation and dissociation | 331 | ||
18.6.1.1 Working principle | 331 | ||
18.6.1.2 Addition of tetrahydrofuran for hydrate formation | 332 | ||
18.6.1.3 Advantages and disadvantages of hydrate formation | 332 | ||
18.6.2 Ammonium carbonation | 333 | ||
18.6.2.1 Working principle | 333 | ||
18.7 SUMMARY OF DEVELOPMENT STATUS | 334 | ||
REFERENCES | 334 | ||
19 Use of hydrates in gas treatment | 336 | ||
19.1 GAS HYDRATES AND THEIR PROPERTIES | 336 | ||
19.2 SELF-PRESERVATION PHENOMENON | 339 | ||
19.3 HYDRATE TECHNOLOGIES FOR BIOGAS SEPARATION AND TRANSPORTATION | 342 | ||
19.4 HYDRATE TECHNOLOGIES OF CO2 SEQUESTRATION IN THE COURSE OF OFFSHORE NATURAL GAS PRODUCTION | 344 | ||
19.5 CONCLUSION | 346 | ||
REFERENCES | 346 | ||
20 Application of zeolites in environmental catalysis | 348 | ||
20.1 INTRODUCTION | 348 | ||
20.2 ZEOLITES IN CATALYSIS | 349 | ||
20.3 ZEOLITE CATALYSTS AND GREEN CHEMISTRY | 350 | ||
20.4 ABATEMENT OF NOx IN OXYGEN-RICH STREAMS WITH ZEOLITE CATALYSTS | 351 | ||
20.4.1 Catalytic NOx removal | 351 | ||
20.4.1.1 Decomposition | 351 | ||
20.4.1.2 NSCR technologies | 352 | ||
20.4.1.3 SCR technologies | 352 | ||
20.4.1.4 SCR under lean-burn conditions | 353 | ||
20.4.2 New developments | 354 | ||
20.5 VOCs ABATEMENT USING ZEOLITES\r | 355 | ||
20.5.1 Sources of VOCs | 355 | ||
20.5.2 VOCs removal and reuse | 356 | ||
20.5.2.1 Adsorption | 356 | ||
20.5.2.2 Decomposition | 356 | ||
20.6 CONCLUSION | 357 | ||
REFERENCES | 358 | ||
21 Operation of fuel cells with biomass resources (hydrogen and alcohols) | 360 | ||
21.1 INTRODUCTION | 360 | ||
21.2 PRINCIPLES AND DIFFERENT TYPES OF FUEL CELLS\r | 361 | ||
21.2.1 Working principles of a fuel cell | 361 | ||
21.2.1.1 FC thermodynamics | 362 | ||
21.2.1.2 FC kinetics | 363 | ||
21.2.2 Different types of a fuel cell | 367 | ||
21.2.2.1 Fuels for fuel cells | 367 | ||
21.2.2.2 Hydrogen fed fuel cells | 369 | ||
21.2.2.3 Methanol and ethanol fed fuel cells | 369 | ||
21.3 WASTE GASES AND BIOMASS TREATMENTS FOR LOW-TEMPERATURE FUEL CELLS | 370 | ||
21.3.1 Thermo-chemical transformation of solid biomass | 370 | ||
21.3.1.1 Steam reforming | 370 | ||
21.3.1.2 Water gas shift reaction | 371 | ||
21.3.1.3 Partial oxidation | 371 | ||
21.3.1.4 Cracking | 371 | ||
21.3.1.5 Impurities | 372 | ||
21.3.2 Transformation of liquid biomass | 372 | ||
21.3.3 Utilization of biogas | 372 | ||
21.3.4 “Syngas” upgrading to high-quality hydrogen | 373 | ||
21.4 LOW-TEMPERATURE FUEL CELLS (PEMFC AND DAFC)\r | 374 | ||
21.4.1 PEMFC | 374 | ||
21.4.1.1 Principle of a PEMFC | 374 | ||
21.4.1.2 The proton exchange membrane | 375 | ||
21.4.1.3 The electrode catalysts | 376 | ||
21.4.1.4 The MEA | 376 | ||
21.4.1.5 The bipolar plates | 376 | ||
21.4.1.6 Auxiliary and control equipment | 377 | ||
21.4.2 DEFC | 378 | ||
21.4.2.1 Principle of the DEFC | 378 | ||
21.4.2.2 DEFC fuel cell tests | 379 | ||
21.5 CONCLUSIONS | 383 | ||
REFERENCES | 383 | ||
22 Resource recovery from synthesis gas | 385 | ||
22.1 INTRODUCTION\r | 385 | ||
22.1.1 Synthesis gas | 385 | ||
22.1.2 The chemical water–gas shift reaction | 386 | ||
22.1.3 The biological water–gas shift reaction | 386 | ||
22.2 HYDROGENOGENIC CO CONVERSION IN ANAEROBIC GRANULAR SLUDGE\r | 387 | ||
22.2.1 Occurrence of hydrogenogenic CO-converting bacteria in sludges from anaerobic wastewater treatment plants\r | 387 | ||
22.2.2 Effect of PCO and H2 on CO conversion routes at 55°C\r | 387 | ||
22.3 APPLICATION OF SYNTHESIS GAS IN THERMOPHILIC BIODESULFURIZATION\r | 389 | ||
22.3.1 Microbiology | 389 | ||
22.3.2 H2S inhibition | 390 | ||
22.3.3 Competition between sulfate reduction and methanogens | 391 | ||
22.3.4 Biomass retention | 392 | ||
22.4 DESIGN OF A BIOLOGICAL SYNTHESIS GAS PURIFICATION PROCESS\r | 392 | ||
22.4.1 Product specification | 392 | ||
22.4.2 Product gas purification | 394 | ||
22.4.3 Bioreactor design | 394 | ||
22.5 CONCLUSION | 395 | ||
REFERENCES | 395 | ||
23 Product recovery from H2S-containing gases | 399 | ||
23.1 INTRODUCTION | 399 | ||
23.2 BIOLOGICAL DESULFURIZATION OF GASEOUS FUELS WITH RECOVERY OF ELEMENTAL SULFUR\r | 400 | ||
23.2.1 Pre-combustion desulfurization | 400 | ||
23.2.1.1 Aqueous iron processes with bacterial regeneration | 401 | ||
23.2.1.2 Phototrophic microbial conversion of H2S to elemental sulfur | 402 | ||
23.2.1.3 Chemotrophic microbial conversion of H2S to elemental sulfur | 402 | ||
23.2.2 Post-combustion process | 405 | ||
23.2.3 Elemental sulfur applications | 405 | ||
23.3 CONCLUSIONS | 406 | ||
REFERENCES | 406 | ||
PART V: Implementation of resource recovery from gas streams | 409 | ||
24 CO2 recovery from flue gas by membrane gas absorption and use in the horticultural industry | 411 | ||
24.1 INTRODUCTION | 411 | ||
24.1.1 CO2 in the horticultural industry | 412 | ||
24.1.2 Integrated supply of heat and CO2 | 412 | ||
24.2 MEMBRANE GAS ABSORPTION\r | 413 | ||
24.2.1 Principle and process | 413 | ||
24.2.2 Membrane flow sheet | 415 | ||
24.2.3 Mass transfer analysis | 416 | ||
24.3 CASE STUDY: CO2 REUSE IN HORTICULTURE\r | 420 | ||
24.3.1 Bench scale studies | 420 | ||
24.3.1.1 Experimental set-up | 420 | ||
24.3.1.2 Bench scale experimental results | 421 | ||
24.3.2 Pilot plant study | 425 | ||
24.3.2.1 Experimental set-up | 425 | ||
24.3.2.2 CO2 product quality | 426 | ||
24.3.3 Heat requirement | 429 | ||
24.4 CONCLUSIONS | 430 | ||
NOMENCLATURE | 430 | ||
REFERENCES | 431 | ||
25 Treatment of carbon disulfide from industrial waste gas emissions: pollutant converted into reusable sulfuric acid | 433 | ||
25.1 INTRODUCTION\r | 433 | ||
25.1.1 Quantities of carbon disulfide emissions | 433 | ||
25.1.2 Adverse effects of carbon disulfide | 434 | ||
25.1.3 Carbon disulfide treatment | 434 | ||
25.2 BIOLOGICAL CARBON DISULFIDE DEGRADATION\r | 434 | ||
25.2.1 Microbial carbon disulfide degradation | 434 | ||
25.2.2 Carbon disulfide degrading microorganisms isolated from full-scale bioreactors | 435 | ||
25.2.2.1 Physiological characteristics | 435 | ||
25.2.2.2 Kinetic parameters | 436 | ||
25.3 BIOREACTORS TREATING CARBON DISULFIDE WASTE GAS EMISSIONS\r | 437 | ||
25.3.1 Introduction | 437 | ||
25.3.2 New developed bioreactors for full-scale applications | 437 | ||
25.3.2.1 Start-up and removal efficiencies | 437 | ||
25.3.2.2 Robustness of a biological system | 438 | ||
25.3.2.3 Formation of sulfuric acid and possibilities for reuse | 440 | ||
25.4 TRADITIONAL TREATMENT OF CARBON DISULFIDE WASTE GAS EMISSIONS\r | 442 | ||
25.4.1 Introduction | 442 | ||
25.4.2 Adsorption | 442 | ||
25.4.3 Incineration | 442 | ||
25.5 EXAMPLES OF FULL-SCALE BIOREACTORS APPLIED AT INDUSTRIES EMITTING CS2\r | 443 | ||
25.5.1 Introduction | 443 | ||
25.5.1 Treatment of CS2 emissions from a cellulose sponge manufacturer | 444 | ||
25.5.2 Treatment of CS2 emissions at fungicide manufacturers | 444 | ||
25.5.3 Treatment of CS2 emissions from manufacturers of cellulose casings | 447 | ||
25.6 CONCLUSION | 448 | ||
REFERENCES | 448 | ||
26 Volatile organic compound treatment by adsorption onto activated carbon fiber cloth and electrothermal regeneration | 450 | ||
26.1 INTRODUCTION | 450 | ||
26.2 ACTIVATED CARBON FIBER CLOTH\r | 451 | ||
26.2.1 Macroscopic and microscopic characteristics | 451 | ||
26.2.2 Electrical properties | 452 | ||
26.2.3 Thermal properties | 453 | ||
26.3 ADSORPTION ONTO ACFC–ELECTROTHERMAL DESORPTION PROCESS | 455 | ||
26.4 DEVELOPMENT OF AN INDUSTRIAL TREATMENT PROCESS | 457 | ||
26.4.1 Characterization of the industrial polluted emission | 457 | ||
26.4.2 VOC removal system | 457 | ||
26.4.3 ACFC adsorber module | 457 | ||
26.4.4 Adsorption: electrothermal desorption procedures | 459 | ||
26.4.5 Process validation | 459 | ||
26.5 CONCLUSION | 461 | ||
ACKNOWLEDGMENTS | 461 | ||
REFERENCES | 461 | ||
27 Treatment of waste gases from formaldehydeand formaldehyde-resin-producing industries | 463 | ||
27.1 INTRODUCTION\r | 463 | ||
27.1.1 Production of formaldehyde and formaldehyde-based resins | 463 | ||
27.1.1.1 Formaldehyde usage | 463 | ||
27.1.1.2 Production of formaldehyde | 464 | ||
27.1.1.3 Production of formaldehyde derivates | 465 | ||
27.1.2 Emission of volatile pollutants in formaldehyde-resin-producing facilities | 466 | ||
27.2 NON-BIOLOGICAL TECHNOLOGIES FOR THE ABATEMENT OF OFF-GASES FROM THE FORMALDEHYDE INDUSTRY | 467 | ||
27.3 BIOLOGICAL TECHNOLOGIES FOR THE ABATEMENT OF OFF-GASES FROM THE FORMALDEHYDE INDUSTRY\r | 468 | ||
27.3.1 Bioreactors for waste gas trea | 468 | ||
27.3.2 Previous studies | 469 | ||
27.3.3 Optimization of the biological treatment | 469 | ||
27.3.3.1 Batch studies | 469 | ||
27.3.3.2 Treatment of formaldehyde and methanol in single-stage bioreactors | 470 | ||
27.3.3.3 Treatment of formaldehyde and methanol in two-stage bioreactor configuration | 473 | ||
27.3.3.4 Treatment of mixtures of formaldehyde, methanol, dimethylether and carbon monoxide | 474 | ||
27.4 CONCLUSIONS | 476 | ||
ACKNOWLEDGMENTS | 476 | ||
NOMENCLATURE | 476 | ||
REFERENCES | 477 | ||
28 Upgrading of biogas for its usage in high-temperature fuel cells and gas grid injection | 479 | ||
28.1 INTRODUCTION | 479 | ||
28.2 BIOGAS UPGRADING TECHNOLOGIES\r | 480 | ||
28.2.1 Advanced biotrickling filter for sulfide removal | 480 | ||
28.2.2 Microbial removal of siloxanes from biogas | 481 | ||
28.2.2.1 Measurement of siloxanes | 481 | ||
28.2.2.2 Microbial degradation of siloxanes | 483 | ||
28.3 HIGH-TECH APPLICATIONS OF BIOGAS\r | 483 | ||
28.3.1 Fuel cells | 483 | ||
28.3.2 Natural gas grid injection | 485 | ||
28.4 CONCLUSIONS | 486 | ||
REFERENCES | 486 | ||
Index | 489 |