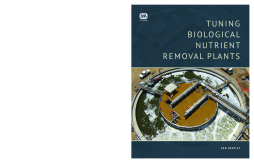
Additional Information
Book Details
Abstract
Tuning Biological Nutrient Removal Plants increases interest in tuning to enhance both performance and capacity, to provide insight into typical plant operating characteristics, and to stimulate operators' interest in studying the behaviour of their own plants. The book focuses on understanding of plant behavioural characteristics so that optimum performance can be achieved and maintained.Â
Tuning Biological Nutrient Removal Plants is carefully organized to cover: influent and effluent characteristics; process fundamentals; individual process characteristics; overall plant characteristics; the evolutionary operation approach to tuning. The approach is practical and the use of mathematics is kept to a minimum and information is supplied in graphical and tabular form. Real operating data from a wide range of plant experiences is included.Â
The book draws on the generosity of many Australian plant owners in permitting their plant data to be incorporated. Not all process types are covered but the tuning principles expounded are universally applicable. The capacity and performance capabilities of a plant are not fixed; both are amenable to on-going enhancement through systematic and enthusiastic effort. Â
The book helps to set new benchmarks in plant operation. Tuning Biological Nutrient Removal Plants is a valuable resource for sewage treatment operations and operations support personnel, sewage process design engineers - operating authorities, consultants, contractors, operators of industrial wastewater treatment plants and sewage treatment lecturers in chemical engineering departments and other training organisations.Â
About the author: Ken Hartley, B.Tech, M.Eng.Sc Fellow, Institution of Engineers, Australia Member Australian Water Association Member International Water Association. Ken Hartley has 45 years' experience in the water and wastewater industry. He has worked for the South Australian water and wastewater authority, consultants GHD and the University of Queensland. Since 1998 he has been an independent consulting process engineer.Â
Table of Contents
Section Title | Page | Action | Price |
---|---|---|---|
Cover\r | Cover | ||
Contents | v | ||
About the Authors | xi | ||
Acknowledgements | xiii | ||
Preface | xv | ||
Chapter 1:\rWhat is tuning? | 1 | ||
Chapter 2:\rInfluent and effluent characteristics | 5 | ||
2.1 THE CATCHMENT | 5 | ||
2.2 FLOW CHARACTERISTICS | 6 | ||
2.3 MASS LOADING CHARACTERISTICS | 9 | ||
2.3.1 Connected population | 13 | ||
2.3.2 Flow | 16 | ||
2.3.3 COD | 16 | ||
2.3.4 SS | 17 | ||
2.3.5 pH and alkalinity | 17 | ||
2.3.6 Dissolved sulfide | 17 | ||
2.3.7 TDS or conductivity | 17 | ||
2.3.8 Pathogens | 18 | ||
2.3.9 Load ratios | 18 | ||
2.3.10 COD/BOD5 | 19 | ||
2.3.11 Nutrient ratios | 19 | ||
2.3.12 Total COD fractions | 19 | ||
2.3.13 Soluble unbiodegradable organic N | 20 | ||
2.3.14 Nitrifier maximum specific growth rate | 21 | ||
2.3.15 Temperature | 21 | ||
2.3.16 Energy content | 22 | ||
2.3.17 Other sewage components | 22 | ||
2.4 SEWER TRANSFORMATIONS | 23 | ||
2.5 EFFECT OF PRIMARY TREATMENT | 23 | ||
2.6 EFFLUENT CHARACTERISTICS | 23 | ||
Chapter 3:\rBiological nutrient removal - process fundamentals | 27 | ||
3.1 THE BASIC PROCESS | 27 | ||
3.2 KINETICS OF BIOLOGICAL PROCESSES | 29 | ||
3.2.1 Substrate utilisation | 29 | ||
3.2.2 Substrate concentration | 30 | ||
3.3 SOLIDS RETENTION TIME\r | 32 | ||
3.3.1 Definition | 32 | ||
3.3.2 Calculation | 32 | ||
3.4 CARBON REMOVAL | 34 | ||
3.4.1 Effect of SRT | 34 | ||
3.4.2 Loading conditions | 35 | ||
3.4.3 F:M ratio | 35 | ||
3.4.4 Mixed liquor suspended solids | 36 | ||
Components of MLSS | 36 | ||
Mass of solids | 36 | ||
3.4.5 Nutrient requirements | 38 | ||
3.4.6 Carbonaceous oxygen demand | 39 | ||
3.5 NITROGEN REMOVAL\r | 40 | ||
3.5.1 The nitrogen cycle | 40 | ||
3.5.2 Nitrification | 40 | ||
Nitrifiers | 40 | ||
Kinetics | 41 | ||
Ammonia-N (substrate) concentration3 | 42 | ||
Temperature | 42 | ||
Salinity | 44 | ||
Concurrent biological phosphorus removal | 44 | ||
Alum dosing | 44 | ||
Load variation | 44 | ||
Unaerated mass fraction | 45 | ||
Nitrification capacity | 46 | ||
3.5.3 Denitrification | 47 | ||
Stoichiometry | 47 | ||
Kinetics | 48 | ||
3.5.4 Simultaneous nitrification and denitrification | 51 | ||
3.5.5 Total process oxygen demand | 52 | ||
Steady state conditions | 52 | ||
Dynamic conditions | 53 | ||
3.6 PHOSPHORUS REMOVAL\r | 53 | ||
3.6.1 Mechanisms | 53 | ||
3.6.2 Process characteristics | 55 | ||
3.6.3 Adverse factors | 57 | ||
Dissolved oxygen and nitrate | 58 | ||
Sulfide | 58 | ||
PAO-GAO competition | 59 | ||
3.7 SUPPLEMENTARY CHEMICAL DOSING | 60 | ||
3.7.1 Phosphorus removal | 60 | ||
3.7.2 Nitrogen removal | 66 | ||
3.7.3 Other effects | 66 | ||
3.8 ALKALINITY AND pH\r | 67 | ||
3.8.1 Chemistry | 67 | ||
3.8.2 Process behaviour | 68 | ||
3.9 RULES OF THUMB | 69 | ||
Chapter 4:\rSludge settleability | 71 | ||
4.1 CHARACTERISING SETTLEABILITY | 71 | ||
4.2 SETTLING RATES | 73 | ||
4.3 FACTORS AFFECTING SETTLEABILITY | 75 | ||
4.3.1 Non-BNR activated sludge processes | 75 | ||
Feed quality | 75 | ||
Operating parameters | 75 | ||
Reactor mixing characteristics | 76 | ||
4.3.2 BNR processes | 76 | ||
Anoxic fraction | 76 | ||
Influent RBCOD | 79 | ||
Chemical dosing | 80 | ||
4.4 EFFECT OF SVI ON EFFLUENT QUALITY | 80 | ||
4.5 FOAMING | 81 | ||
Chapter 5:\rBNR flowsheets | 83 | ||
5.1 NITROGEN REMOVAL\r | 83 | ||
5.1.1 Modified Ludzack-Ettinger (MLE) | 83 | ||
5.1.2 Bardenpho | 83 | ||
5.2 PHOSPHORUS REMOVAL\r | 84 | ||
5.2.1 Phoredox | 84 | ||
5.3 NITROGEN AND PHOSPHORUS REMOVAL\r | 84 | ||
5.3.1 Modified Bardenpho | 84 | ||
5.3.2 Johannesburg (JHB) | 84 | ||
5.3.3 University of Cape Town (UCT) | 84 | ||
5.3.4 Modified UCT (MUCT) | 84 | ||
5.3.5 Westbank | 85 | ||
5.3.6 Membrane Bioreactor (MBR) | 85 | ||
Chapter 6:\rReactors | 89 | ||
6.1 MIXING | 89 | ||
6.1.1 Mixing regime | 89 | ||
Complete mix | 89 | ||
Plug flow | 91 | ||
Arbitrary flow | 91 | ||
Time constant | 94 | ||
6.1.2 Mixing intensity | 94 | ||
Active mixing | 94 | ||
Flocculation | 94 | ||
6.2 AERATION | 96 | ||
6.2.1 Oxygen transfer rate | 96 | ||
6.2.2 Oxygen transfer efficiency | 99 | ||
6.2.3 Carbon dioxide stripping | 99 | ||
6.3 COMPARTMENTALISED REACTORS\r | 100 | ||
6.3.1 Description | 100 | ||
6.3.2 Process characteristics | 100 | ||
6.3.3 Operating principles | 103 | ||
6.4 OXIDATION DITCHES\r | 103 | ||
6.4.1 Description | 103 | ||
6.4.2 Process characteristics | 103 | ||
6.4.3 Hydraulics | 107 | ||
6.4.4 Mechanical aerator characteristics | 109 | ||
Horizontal shaft aerators | 109 | ||
Vertical shaft aerators | 109 | ||
6.4.5 Operating principles | 110 | ||
6.5 MEMBRANE BIOREACTORS\r | 110 | ||
6.5.1 Description | 110 | ||
6.5.2 Process characteristics | 111 | ||
Bioreactor | 111 | ||
Membranes | 113 | ||
6.5.3 Operating principles | 115 | ||
6.6 SEQUENCING BATCH REACTORS\r | 115 | ||
6.6.1 Description | 115 | ||
6.6.2 Process characteristics | 116 | ||
6.6.3 Operating principles | 120 | ||
Chapter 7:\rSecondary clarifiers | 121 | ||
7.1 DESCRIPTION | 121 | ||
7.2 MASS BALANCES | 122 | ||
7.3 OPERATING DIAGRAMS | 124 | ||
7.4 EFFLUENT QUALITY\r | 127 | ||
7.4.1 Factors affecting effluent SS | 127 | ||
Degree of flocculation | 128 | ||
Environmental chemistry | 128 | ||
SRT | 128 | ||
SSVI | 129 | ||
MLSS concentration | 129 | ||
Chemical precipitant dosing | 130 | ||
Overflow and settling rates | 132 | ||
Rising sludge | 133 | ||
7.4.2 Other effects of clarifiers on effluent quality | 133 | ||
7.5 CLARIFIER STRESS TESTING | 133 | ||
Chapter 8:\rSludge processes | 137 | ||
8.1 OVERVIEW | 137 | ||
8.2 AEROBIC DIGESTION | 137 | ||
8.2.1 Stabilisation performance | 138 | ||
8.2.2 Operating characteristics | 140 | ||
8.2.3 Operating examples | 141 | ||
West Byron STP | 141 | ||
Brunswick Valley STP | 143 | ||
8.2.4 Operating principles | 145 | ||
8.3 SLUDGE DEWATERING | 145 | ||
8.3.1 Mass balances | 145 | ||
8.3.2 Belt filter press | 146 | ||
8.3.3 Centrifuge | 148 | ||
Chapter 9:\rPlant characteristics | 155 | ||
9.1 MASS BALANCES | 155 | ||
RAS concentration | 155 | ||
Sludge thickeners | 156 | ||
Sludge dewatering | 157 | ||
Dewatered sludge P content | 157 | ||
Biological P removal | 157 | ||
9.2 OPERATIONAL PROCESS CAPACITY | 157 | ||
9.2.1 Bottlenecks | 158 | ||
9.2.2 Failure curves | 159 | ||
9.3 CAPACITY ENVELOPES | 159 | ||
9.3.1 Continuous flow process | 160 | ||
9.3.2 SBR process | 162 | ||
9.4 ENERGY CONSUMPTION | 164 | ||
9.4.1 Water cycle | 164 | ||
9.4.2 Plant energy balance | 165 | ||
9.4.3 Energy models | 166 | ||
General | 166 | ||
Plant-specific energy characteristics | 168 | ||
MBRs | 168 | ||
9.4.4 Tuning | 170 | ||
Chapter 10:\rProcess control | 171 | ||
10.1 THE ROLE OF CONTROL AND AUTOMATION | 171 | ||
10.2 DISTURBANCES | 172 | ||
10.3 CONTROL PRIORITIES\r | 173 | ||
10.3.1 The system | 173 | ||
10.3.2 The importance of dynamics | 173 | ||
10.3.3 Modelling | 174 | ||
10.4 FEEDBACK CONTROL | 174 | ||
10.4.1 Open and closed loop control | 174 | ||
10.4.2 Low level control | 176 | ||
10.4.3 Integral action | 178 | ||
10.4.4 Derivative action | 178 | ||
10.4.5 Computer realisation of the PID controller | 179 | ||
10.4.6 When is PID control appropriate? | 179 | ||
10.4.7 Controller tuning | 180 | ||
10.4.8 Manual PI tuning | 181 | ||
10.4.9 Ziegler-Nichols frequency response method | 182 | ||
10.4.10 Autotuning | 183 | ||
10.5 INSTRUMENTATION AND MONITORING\r | 183 | ||
10.5.1 Instruments | 183 | ||
10.5.2 Estimating the oxygen uptake rate | 184 | ||
10.6 PUMPING\r | 185 | ||
10.6.1 Pump characteristics | 185 | ||
10.6.2 Relationship between flow rate and power | 187 | ||
10.7 ESSENTIAL CONTROL LOOPS | 188 | ||
10.7.1 Dissolved oxygen control | 188 | ||
10.7.2 Ammonia-Based DO control | 192 | ||
10.7.3 Recycle flow controls | 193 | ||
10.7.4 Chemical precipitation | 193 | ||
10.7.5 Anaerobic digestion process control | 194 | ||
10.8 MINIMISING OPERATING COST\r | 195 | ||
10.8.1 Approaches | 195 | ||
10.8.2 The human factor | 195 | ||
10.9 CONCLUDING REMARKS | 196 | ||
Chapter 11:\rEvolutionary operation | 197 | ||
11.1 LEARNING | 197 | ||
11.2 APPLICATION TO SEWAGE TREATMENT PLANTS\r | 198 | ||
11.2.1 Plant improvement strategies | 198 | ||
11.2.2 Learning curves | 199 | ||
11.2.3 Startup phase | 200 | ||
Experience | 200 | ||
Contractual startups | 203 | ||
11.3 LONG-TERM IMPROVEMENT\r | 204 | ||
11.3.1 Potential | 204 | ||
11.3.2 Tuning | 205 | ||
11.3.3 Stress testing | 206 | ||
11.3.4 Debottlenecking | 207 | ||
11.3.5 Costs | 207 | ||
11.4 EVOP PROCEDURES | 209 | ||
11.4.1 Method | 209 | ||
Step 1: Data collection | 210 | ||
Step 2: Data interpretation | 213 | ||
Step 3: Process adjustment | 213 | ||
11.4.2 Trend plots | 214 | ||
11.4.3 General principles | 220 | ||
11.5 FAUX EVOP | 221 | ||
Appendix 1:\rA note on the statistics of variability | 223 | ||
AVERAGE AND MEDIAN | 223 | ||
PERCENTILES | 223 | ||
APPLICATION | 224 | ||
Appendix 2:\rChemicals: useful properties | 227 | ||
Appendix 3:\rAbbreviations | 231 | ||
References | 233 | ||
Index | 241 |