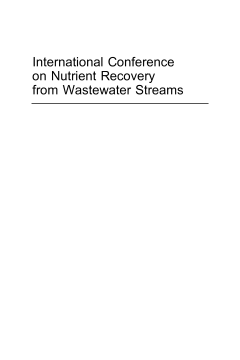
BOOK
International Conference on Nutrient Recovery From Wastewater Streams Vancouver, 2009
Ken Ashley | Don Mavinic | Fred Koch
(2009)
Additional Information
Book Details
Abstract
Paperback + CD-ROM
Closing the loop for nutrients in wastewaters (municipal sewage, animal wastes, food industry, commercial and other liquid waste streams) is a necessary, sustainable development objective, to reduce resource consumption and greenhouse gas emissions. Chemistry, engineering and process integration understanding are all developing quickly, as new processes are now coming online. A new "paradigm" is emerging, globally. Commercial marketing of recovered nutrients as "green fertilizers" or recycling of nutrients through biomass production to new outlets, such as bioenergy, is becoming more widespread. This exciting conference brings together various waste stream industries, regulators, researchers, process engineers and commercial managers, to develop a broad-based, intersectional understanding and joint projects for phosphorus and nitrogen recovery from wastewater streams, as well as reuse. Over 90 papers from over 30 different countries presented in this volume.
This conference is sponsored by: • Metro Vancouver • Global Phosphate Forum • Stantec Consulting Ltd. • The Chartered Institution of Water and Environmental Management (CIWEM) • Ostara Nutrient Recovery Technologies, Inc. (ONRTI) • The University of British Columbia (UBC) • The United States Environmental Protection Agency (EPA) • The British Columbia Water and Wastewater Association (BCWWA) • The Canadian Society for Civil Engineering (CSCE) • The Ostara Research Foundation (ORF)
Table of Contents
Section Title | Page | Action | Price |
---|---|---|---|
Half Title | 1 | ||
Title | 3 | ||
Copyright | 4 | ||
Contents | 5 | ||
Preface: ‘‘The Philosopher’s Stone’’ | 11 | ||
Committees | 13 | ||
Acknowledgements | 14 | ||
Elimination of eutrophication through resource recovery | 15 | ||
INTRODUCTION | 15 | ||
What is eutrophication? | 16 | ||
The concept of a limiting nutrient | 18 | ||
Where do the main nutrients come from? | 19 | ||
How do we deal with this surplus of nutrients? | 21 | ||
Phosphorus recovery | 24 | ||
Composting | 27 | ||
Recovery of nitrogen | 27 | ||
Urine separation | 28 | ||
Use of algae as bio-fuels | 30 | ||
Concluding remarks | 34 | ||
REFERENCES | 34 | ||
Preferred future phosphorus scenarios: A framework for meeting long-term phosphorus needs for global food demand | 37 | ||
INTRODUCTION | 37 | ||
METHODOLOGY: SCENARIO DEVELOPMENT IN THE FACE OF UNCERTAINTY | 38 | ||
AN INTEGRATED FRAMEWORK FOR ANALYSING FUTURE SUPPLY AND DEMAND OPTIONS | 40 | ||
FUTURE GLOBAL PHOSPHORUS DEMAND: A MOVING TARGET | 41 | ||
FUTURE PHOSPHORUS DEMAND REDUCTION MEASURES | 42 | ||
Changing diets | 43 | ||
Food chain efficiency | 44 | ||
Agricultural efficiency | 44 | ||
FUTURE PHOSPHORUS SUPPLY OPTIONS | 45 | ||
Phosphate rock | 46 | ||
Manure | 47 | ||
Human excreta | 48 | ||
Food Waste | 49 | ||
Crop Residues | 50 | ||
Other sources | 51 | ||
A LONG-TERM PERSPECTIVE: HISTORICAL AND FUTURE SCENARIOS | 51 | ||
INSTITUTIONAL CHALLENGES AND POLICY IMPLICATIONS | 51 | ||
CONCLUSIONS | 53 | ||
ACKNOWLEDGEMENTS | 53 | ||
REFERENCES | 53 | ||
Notes | 57 | ||
Impact of supply and demand on the price development of phosphate (fertilizer) | 59 | ||
INTRODUCTION | 59 | ||
SUPPLY: P-RESERVES | 60 | ||
Phosphate supply in 2030 | 61 | ||
DEMAND: P-CONSUMPTION | 61 | ||
Current situation | 61 | ||
Factors affecting the future fertilizer demand | 62 | ||
Phosphate demand in 2030 | 64 | ||
PRICE DEVELOPMENT | 64 | ||
Actual and historical development | 64 | ||
Future development | 65 | ||
CONCLUSIONS | 67 | ||
REFERENCES | 68 | ||
Wastewater treatment and the green revolution | 69 | ||
INTRODUCTION | 69 | ||
THE NEW FLOWSHEET | 70 | ||
Principles and treatment mechanisms | 70 | ||
Principal treatment steps and process systems | 72 | ||
Aerobic MBR | 73 | ||
Anaerobic MBR digestion system | 75 | ||
Phosphorus and nitrogen removal | 76 | ||
Nutrient recovery | 77 | ||
New flowsheet modelling | 77 | ||
Technical and economic hurdles | 80 | ||
SUMMARY | 80 | ||
REFERENCES | 81 | ||
A review of struvite nucleation studies | 83 | ||
INTRODUCTION | 83 | ||
BACKGROUND | 83 | ||
Solution thermodynamics | 83 | ||
Thermodynamic equilibria | 84 | ||
Supersaturation | 85 | ||
Thermodynamic solvers | 86 | ||
Nucleation | 86 | ||
Previous work | 87 | ||
EXPERIMENTAL METHOD | 88 | ||
RESULTS AND DISCUSSION | 89 | ||
CONCLUSIONS | 91 | ||
REFERENCES | 91 | ||
A quantitative method analyzing the content of struvite in phosphate-based precipitates | 93 | ||
INTRODUCTION | 93 | ||
MATERIALS AND METHOD | 94 | ||
Formation of single crystal of struvite | 94 | ||
Formation of phosphate-based precipitates | 95 | ||
Crystal characterization and image analyses | 95 | ||
Element analyses | 95 | ||
Calculating the struvite content | 95 | ||
RESULTS AND DISCUSSION | 96 | ||
XRD and image analyses | 96 | ||
Element analyses | 98 | ||
Calculating the struvite content in precipitates | 99 | ||
CONCLUSIONS | 101 | ||
ACKNOWLEDGEMENTS | 101 | ||
REFERENCES | 101 | ||
Phosphorus removal from an industrial wastewater by struvite crystallization into an airlift reactor | 103 | ||
INTRODUCTION | 103 | ||
MATERIALS AND METHODS | 105 | ||
RESULTS AND DISCUSSION | 106 | ||
CONCLUSIONS | 110 | ||
ACKNOWLEDGEMENTS | 110 | ||
REFERENCES | 110 | ||
Quantifying phosphorus recovery potentials by full-scale process analysis and modelling | 113 | ||
INTRODUCTION | 113 | ||
DESCRIPTION OF RELEVANT FLOWS | 114 | ||
Relevant flows and fractions | 115 | ||
Comparison of literature and measured data | 116 | ||
MODELLING APPROACH | 118 | ||
RESULTS OF LABORATORY-, Semi- AND \x06FULL-SCALE MEASUREMENTS | 121 | ||
Check of kinetic parameters of the enhanced biological phosphorous removal | 121 | ||
Model enhancement | 121 | ||
Module integration ‘‘P recovery via struvite’’ | 122 | ||
FUTURE PROSPECTS | 123 | ||
REFERENCES | 124 | ||
Validation of a comprehensive chemical equilibrium model for predicting struvite precipitation | 125 | ||
INTRODUCTION | 125 | ||
MODEL FORMULATION | 127 | ||
Assumptions | 127 | ||
Equations | 128 | ||
RESULTS AND DISCUSSION | 129 | ||
CONCLUSIONS | 133 | ||
REFERENCES | 134 | ||
A thermochemical approach for struvite precipitation modelling from wastewater | 135 | ||
INTRODUCTION | 135 | ||
CHEMICAL EQUILIBRIUM MODEL FOR STRUVITE PRECIPITATION | 136 | ||
Model formulation | 136 | ||
Solution strategy | 138 | ||
RESULTS AND DISCUSSION | 140 | ||
CONCLUSION | 142 | ||
REFERENCES | 143 | ||
Numerical investigations of the hydrodynamics of the UBC MAP fluidized bed crystallizer | 145 | ||
INTRODUCTION | 145 | ||
CRYSTALLIZATION PROCESS IN UBC MAP FLUIDIZED BED REACTOR | 147 | ||
CFD MODELLING | 147 | ||
RESULTS AND DISCUSSION | 149 | ||
CONCLUSIONS | 155 | ||
REFERENCES | 157 | ||
About the economy of phosphorus recovery | 159 | ||
INTRODUCTION | 159 | ||
THE RESOURCE ECONOMY OF PHOSPHORUS | 160 | ||
The price of phosphorus | 161 | ||
The value of nutrients | 162 | ||
THE COSTS OF PHOSPHORUS RECOVERY | 164 | ||
Process components | 164 | ||
Costs for MAP precipitation | 165 | ||
Costs of phosphate remobilization | 168 | ||
Reducing supplies input | 169 | ||
CONCLUSIONS | 170 | ||
REFERENCES | 171 | ||
Different strategies for recovering phosphorus: Technologies and costs | 173 | ||
INTRODUCTION | 173 | ||
PROCESS DESCRIPTIONS | 174 | ||
Post precipitation in the effluent of a WWTP | 174 | ||
Phosphate release and struvite crystallisation (PRISA process) | 174 | ||
Phosphorus extraction and recovery from ash (RPA process) | 177 | ||
ECONOMICS | 178 | ||
COMPARISON AND OUTLOOK | 179 | ||
ACKNOWLEDGEMENT | 180 | ||
REFERENCES | 180 | ||
Social and economic feasibility of struvite recovery from Urine at the community level in Nepal | 183 | ||
INTRODUCTION | 183 | ||
Struvite | 184 | ||
Siddhipur | 184 | ||
METHODS | 185 | ||
Urine quality | 185 | ||
FINANCIAL FEASIBILITY | 186 | ||
CONCLUSIONS | 190 | ||
ACKNOWLEDGEMENTS | 191 | ||
REFERENCES | 191 | ||
Induced struvite precipitation in an airlift reactor for phosphorus recovery | 193 | ||
INTRODUCTION | 193 | ||
MATERIALS AND METHODS | 195 | ||
The investigated model system | 195 | ||
Airlift reactor in batch mode | 195 | ||
Airlift reactor in continuous operation | 197 | ||
Particle sizes of precipitated MAP | 197 | ||
RESULTS AND DISCUSSION | 198 | ||
Airlift reactor in batch mode | 198 | ||
Airlift reactor in continuous operation | 202 | ||
CONCLUSION | 205 | ||
REFERENCES | 205 | ||
Pilot testing and economic evaluation of struvite recovery from dewatering centrate at HRSD’s Nansemond WWTP | 207 | ||
INTRODUCTION | 207 | ||
THE NANSEMOND TREATMENT PLANT | 208 | ||
STRUVITE RECOVERY PROCESS DESCRIPTION | 210 | ||
PILOT RESULTS | 212 | ||
DISCUSSION | 214 | ||
COST/BENEFIT ANALYSIS | 215 | ||
CONCLUSIONS | 216 | ||
REFERENCES | 216 | ||
Standardizing the struvite solubility product for field trial optimization | 217 | ||
INTRODUCTION | 217 | ||
Struvite solubility product | 217 | ||
Struvite chemistry | 219 | ||
Methodology | 220 | ||
Experimental setup | 220 | ||
Experimental solutions | 220 | ||
Operating conditions | 220 | ||
Analytical techniques | 221 | ||
Modeling techniques | 221 | ||
Formation model | 221 | ||
PHREEQC model | 222 | ||
Speciation model | 223 | ||
RESULTS AND DISCUSSIONS | 223 | ||
Solubility curve | 223 | ||
Model comparison | 224 | ||
CONCLUSIONS | 226 | ||
ACKNOWLEDGEMENTS | 226 | ||
REFERENCES | 226 | ||
Plant availability of P fertilizers recycled from sewage sludge and meat-and-bone meal in field and pot experiments | 229 | ||
INTRODUCTION | 229 | ||
MATERIALS AND METHODS | 230 | ||
RESULTS | 232 | ||
DISCUSSION | 235 | ||
CONCLUSION | 237 | ||
REFERENCES | 237 | ||
Ecological testing of products from phosphorus recovery processes – first results | 239 | ||
INTRODUCTION | 239 | ||
AIM OF THE STUDY | 240 | ||
MATERIAL AND METHODS | 241 | ||
Test strategy | 241 | ||
Material | 242 | ||
Methods | 242 | ||
RESULTS | 244 | ||
Solubility of phosphorus | 244 | ||
Trace metals | 245 | ||
Plant available phosphorus | 246 | ||
P-uptake | 247 | ||
CONCLUSIONS | 247 | ||
REFERENCES | 248 | ||
Strategy for separation of manure P through flocculation | 249 | ||
INTRODUCTION | 249 | ||
MATERIALS AND METHODS | 251 | ||
RESULTS AND DISCUSSION | 251 | ||
Effect of flocculation | 251 | ||
Strategy for flocculation | 255 | ||
CONCLUSION | 256 | ||
REFERENCES | 256 | ||
Phosphate removal in agro-industry: pilot and full-scale operational considerations of struvite crystallisation | 259 | ||
INTRODUCTION | 259 | ||
MATERIAL AND METHODS | 260 | ||
Pilot plant description | 260 | ||
Anaerobic effluent characteristics | 261 | ||
Analytical methods | 261 | ||
RESULTS | 262 | ||
Pilot-scale tests | 262 | ||
Full scale unit | 264 | ||
DISCUSSION | 266 | ||
CONCLUSIONS | 267 | ||
REFERENCES | 268 | ||
Development of a process control system for online monitoring and control of a struvite crystallization process | 271 | ||
INTRODUCTION | 271 | ||
Objective | 272 | ||
METHODS AND MATERIALS | 272 | ||
Process description | 272 | ||
Terminology | 273 | ||
Supersaturation ratio (SSR) | 273 | ||
Struvite solubility product | 273 | ||
The controlled variable | 274 | ||
Set point (SP) | 274 | ||
Manipulated variable | 274 | ||
Instrumentation and process monitoring | 274 | ||
Process control | 275 | ||
Feedback controller model program development | 276 | ||
Carbon dioxide stripping model | 277 | ||
Graphical User Interface (GUI) | 279 | ||
Analytical methods | 279 | ||
Expectations from the model | 280 | ||
CONCLUSIONS | 280 | ||
ACKNOWLEDGEMENT | 281 | ||
REFERENCES | 281 | ||
Increasing cost efficiency of struvite precipitation by using alternative precipitants and P-remobilization from sewage sludge | 283 | ||
INTRODUCTION | 283 | ||
MATERIALS AND METHODS | 284 | ||
Biological P-remobilization from activated sludge | 284 | ||
Seawater and wastewater from potash production as magnesium sources | 285 | ||
Pilot-scale precipitation reactor (seawater as precipitant) | 286 | ||
RESULTS AND DISCUSSION | 287 | ||
Remobilization of phosphorus | 287 | ||
Seawater as precipitant | 288 | ||
Wastewater from potash production as precipitant | 290 | ||
Upflow precipitation reactor | 290 | ||
CONCLUSIONS | 292 | ||
REFERENCES | 293 | ||
Temperature dependence of electrical conductivity and its relationship with ionic strength for struvite precipitation system | 295 | ||
INTRODUCTION | 296 | ||
MATERIALS AND METHODS | 297 | ||
Temperature dependence of EC | 297 | ||
EC-I relationship | 297 | ||
Analyses | 297 | ||
RESULTS AND DISCUSSION | 298 | ||
Temperature dependence of EC | 298 | ||
EC-I relationship | 300 | ||
CONCLUSIONS | 303 | ||
REFERENCES | 304 | ||
Study on phosphorus recovery by calcium phosphate precipitation from wastewater treatment plants | 305 | ||
INTRODUCTION | 305 | ||
EXPERIMENT METHODS | 306 | ||
Principle | 306 | ||
Raw wastewater | 306 | ||
Experiment focus | 308 | ||
TEST RESULTS | 308 | ||
Adjust pH by adding Ca(OH)&sub2 | 308 | ||
The effect of pH | 308 | ||
The effect of temperature | 309 | ||
Adjusting pH by adding NaOH | 310 | ||
Adjusting pH by aeration | 310 | ||
The effect of aeration time | 310 | ||
The effect of SP concentration | 310 | ||
THE REUSE FEASIBILITY OF RECOVERED HAP | 312 | ||
Content analysis of the product | 312 | ||
Reuse potential of recovered product | 312 | ||
CONCLUSIONS | 312 | ||
REFERENCES | 313 | ||
Phosphorus removal and recovery from sewage sludge as calcium phosphate by addition of calcium silicate hydrate compounds (CSH) | 315 | ||
INTRODUCTION | 315 | ||
Phosphorus in waste water treatment | 316 | ||
MATERIAL AND METHODS | 317 | ||
Analytical methods | 317 | ||
Long-term experiments | 317 | ||
RESULTS AND DISCUSSION | 320 | ||
Long-term experiments | 320 | ||
Long-term experiments with EBPR sludges | 323 | ||
Economical aspects | 328 | ||
CONCLUSIONS | 328 | ||
ACKNOWLEDGEMENTS | 329 | ||
REFERENCES | 329 | ||
Field application methods for the liquid fraction of separated animal slurry in growing cereal crops | 331 | ||
INTRODUCTION | 331 | ||
MATERIALS AND METHODS | 332 | ||
Measuring draught force | 332 | ||
Sand bin | 332 | ||
Soil bin | 334 | ||
NH&sub3 | 334 | ||
RESULTS AND DISCUSSION | 334 | ||
Pressure and flow | 334 | ||
Draught force | 335 | ||
Jet pointing forward | 335 | ||
Jet pointing down | 338 | ||
Jet pointing back | 338 | ||
Ammonia emission | 339 | ||
REFERENCES | 339 | ||
Research on nutrient removal and recovery from swine wastewater in China | 341 | ||
INTRODUCTION | 341 | ||
MATERIALS AND METHODS | 342 | ||
Bench scale experiments | 342 | ||
Pilot scale experiments | 343 | ||
Analytical Methods and Instrumentation | 344 | ||
RESULTS AND DISCUSSION | 345 | ||
Bench scale experiments | 345 | ||
Influence of pH value | 345 | ||
Influence of Mg² | 346 | ||
Influence of Ca²+ and carbonate | 346 | ||
Pliot scale experiments | 348 | ||
Nutrient removal and recovery in the sequencing batch MAP reactor | 348 | ||
Nutrient removal in the continuous flow MAP reactor | 350 | ||
CONCLUSIONS | 351 | ||
ACKNOWLEDGEMENTS | 352 | ||
REFERENCES | 352 | ||
Chemical recycling of phosphorus from piggery wastewater | 353 | ||
INTRODUCTION | 353 | ||
MATERIAL AND METHODS | 354 | ||
Piggery wastewater supernatants | 354 | ||
Biochemical analyses | 355 | ||
Description of the precipitation runs | 355 | ||
Solid analyses | 356 | ||
RESULTS AND DISCUSSION | 356 | ||
Run 1: | 356 | ||
Run 2: | 359 | ||
CONCLUSIONS | 362 | ||
REFERENCES | 363 | ||
Struvite harvesting to reduce ammonia and phosphorus recycle | 365 | ||
INTRODUCTION | 365 | ||
Sidestream treatment options | 366 | ||
PILOTING THE OSTARA PROCESS | 366 | ||
Reactor operation | 366 | ||
Reactor products | 370 | ||
Reactor effluent | 370 | ||
FULL SCALE STRUVITE RECOVERY ANALYSIS | 370 | ||
CONCLUSIONS | 372 | ||
REFERENCE | 373 | ||
The application of process systems engineering to the development of struvite recovery systems | 375 | ||
INTRODUCTION | 375 | ||
PROCESS MODELLING | 376 | ||
Process chemistry and thermodynamics | 376 | ||
Process kinetics | 377 | ||
Process description | 378 | ||
Model simulation and thermodynamic validation | 378 | ||
PARAMETER ESTIMATION | 380 | ||
Experimental design | 380 | ||
Regression of growth rate parameters k and n | 381 | ||
RESULTS AND DISCUSSION | 381 | ||
CONCLUSIONS AND RECOMENDATIONS | 383 | ||
REFERENCES | 384 | ||
Membrane EBPR for phosphorus removal and recovery using a sidestream flow system: preliminary assessment | 385 | ||
INTRODUCTION | 385 | ||
METHODOLOGY | 386 | ||
Model and process design | 386 | ||
MEBPR process | 387 | ||
Sidestream configuration | 388 | ||
Struvite crystallizer | 388 | ||
Sampling and analyses | 389 | ||
Sidestream wasting | 390 | ||
RESULTS AND DISCUSSION | 390 | ||
Simulation results | 390 | ||
Experimental results | 394 | ||
PO&sub4-P and NH&sub4-N release in PRU | 396 | ||
P recovery study | 398 | ||
P removal and recovery efficiency | 398 | ||
N removal | 399 | ||
CONCLUSIONS | 399 | ||
REFERENCES | 400 | ||
Phosphorus recovery from eluated sewage sludge ashes by nanofiltration | 403 | ||
INTRODUCTION | 403 | ||
THEORETICAL BACKGROUND OF THE PROCESS | 404 | ||
MATERIAL AND METHODS | 405 | ||
Preparation of ash eluates | 405 | ||
Filtration experiments | 406 | ||
Analytics | 408 | ||
Preparation of model solutions | 408 | ||
RESULTS AND DISCUSSION | 409 | ||
Nanofiltration | 409 | ||
Ultrafiltration | 413 | ||
Economical aspects | 415 | ||
CONLCUSION AND OUTLOOK | 417 | ||
ACKNOWLEDGEMENT | 417 | ||
REFERENCES | 417 | ||
P-recovery from sewage sludge ash – technology transfer from prototype to industrial manufacturing facilities | 419 | ||
INTRODUCTION | 419 | ||
THE PROCESS | 420 | ||
THE PRODUCT | 421 | ||
TECHNOLOGY TRANSFER | 424 | ||
The prototype manufacturing plant | 424 | ||
The industrial manufacturing plant | 426 | ||
CONCLUSION | 428 | ||
REFERENCES | 429 | ||
Phosphorus recovery by thermochemical treatment of sewage sludge ash – Results of the European FP6-project SUSAN | 431 | ||
INTRODUCTION | 431 | ||
METHODOLOGY | 433 | ||
RESULTS | 435 | ||
Thermochemical process | 435 | ||
Heavy metal recycling | 439 | ||
Pot trials | 439 | ||
CONCLUSION | 443 | ||
OUTLOOK | 444 | ||
REFERENCES | 444 | ||
Remediation of phosphorus from animal slurry | 445 | ||
INTRODUCTION | 445 | ||
MATERIALS AND METHODS | 446 | ||
Dry matter (DM), ash fraction (AF) and volatile solids (VS) | 447 | ||
Thermal gravimetric analysis (TGA) | 447 | ||
X-ray diffraction spectroscopy (XRD) | 447 | ||
Extraction | 448 | ||
Phosphorus analysis | 448 | ||
RESULTS AND DISCUSSION | 448 | ||
Thermal gravimetric analysis | 448 | ||
X-ray diffraction | 450 | ||
Phosphorus content | 453 | ||
CONCLUSIONS | 454 | ||
REFERENCES | 454 | ||
Affecting corn processing nutrients using membrane separation and biological extraction and conversion | 457 | ||
INTRODUCTION | 457 | ||
CHARACTERIZATION OF CORN PROCESSING NUTRIENTS | 460 | ||
Wet milling | 461 | ||
Dry grind | 464 | ||
MEMBRANE SEPARATIONS | 465 | ||
Gluten filtration and nutrient separations | 465 | ||
Thin stillage filtration and nutrient separations | 468 | ||
EXTRACTION, CONVERSION AND USE OF NUTRIENTS | 469 | ||
CONCLUSIONS | 470 | ||
REFERENCES | 470 | ||
Technology for recovery of phosphorus from animal wastewater through calcium phosphate precipitation | 473 | ||
INTRODUCTION | 473 | ||
Basic process configuration (Figure 1) | 474 | ||
Process chemistry | 474 | ||
PROCESS APPLICATIONS TO LIVESTOCK WASTEWATER | 476 | ||
Phosphorus extraction from digested swine lagoon effluents (Figure 2) | 476 | ||
Manure treatment systems without lagoon (Figure 2) | 478 | ||
CONCLUSIONS | 481 | ||
REFERENCES | 482 | ||
Determining the operational conditions required for homogeneous struvite precipitation from belt press supernatant | 483 | ||
INTRODUCTION | 483 | ||
MATERIAL AND METHODS | 485 | ||
RESULTS AND DISCUSSION | 486 | ||
Reactor operation at different HRTs and different pH values for each HRT | 487 | ||
CONCLUSIONS | 491 | ||
ACKNOWLEDGEMENTS | 491 | ||
REFERENCES | 491 | ||
Involvement of filamentous bacteria in the phosphorus recovery cycle | 493 | ||
INTRODUCTION | 493 | ||
MATERIALS AND METHODS | 495 | ||
RESULTS AND DISCUSSION | 495 | ||
PRACTICAL IMPLICATIONS | 500 | ||
CONCLUSIONS | 501 | ||
REFERENCES | 501 | ||
Carbon and struvite recovery from centrate at a biological nutrient removal plant | 503 | ||
INTRODUCTION | 503 | ||
Description of plant process | 504 | ||
Background | 504 | ||
Objectives | 505 | ||
Acknowledgements | 505 | ||
METHODS | 506 | ||
Crystallizer operation | 506 | ||
Feed | 506 | ||
Magnesium | 508 | ||
pH control | 508 | ||
Monitoring | 508 | ||
RESULTS AND DISCUSSION | 509 | ||
Reactor operation | 509 | ||
Monitoring | 509 | ||
Volatile fatty acids | 509 | ||
Phosphate | 510 | ||
Ammonium nitrogen | 512 | ||
Magnesium | 512 | ||
pH | 512 | ||
Temperature | 512 | ||
Total suspended solids | 513 | ||
Batch test results | 513 | ||
CONCLUSIONS | 514 | ||
REFERENCES | 515 | ||
Recovery of phosphorus from sewage sludge incineration ash by combined bioleaching and bioaccumulation | 517 | ||
INTRODUCTION | 517 | ||
MATERIALS AND METHODS | 519 | ||
Acidithiobacillus spec. strains and AEDS- population | 519 | ||
Sampling and analysis | 520 | ||
RESULTS AND DISCUSSION | 520 | ||
Bioleaching of phosphorus and metals | 520 | ||
Bioaccumulation of phosphorus and separation of heavy metals | 522 | ||
CONCLUSIONS | 523 | ||
ACKNOWLEDGEMENT | 524 | ||
REFERENCES | 524 | ||
Energy efficient nutrient recovery from household wastewater using struvite precipitation and zeolite adsorption techniques A pilot plant study in Sweden | 525 | ||
INTRODUCTION | 525 | ||
METHOD AND MATERIALS | 526 | ||
The pilot plant | 526 | ||
Wastewater flows in the house | 527 | ||
The energy system of the house | 529 | ||
Sampling | 529 | ||
Chemical analysis | 529 | ||
RESULTS AND DISCUSSION | 530 | ||
CONCLUSIONS | 532 | ||
Nutrient recovery | 532 | ||
Energy saving and reduction of greenhouse gases | 533 | ||
ACKNOWLEDGEMENTS | 534 | ||
REFERENCES | 534 | ||
Crystallisation of calcium phosphate from sewage: efficiency of batch mode technology and quality of the generated products | 535 | ||
INTRODUCTION | 535 | ||
OBJECTIVE | 536 | ||
MATERIAL AND METHODS | 536 | ||
RESULTS AND DISCUSSION | 537 | ||
CONCLUSION | 542 | ||
ACKNOWLEDGEMENT | 543 | ||
REFERENCES | 543 | ||
Effect of osmotic pressure and substrate resistance on transmembrane flux during the concentration of pretreated swine manure with reverse osmosis membranes | 545 | ||
INTRODUCTION | 545 | ||
MATERIALS AND METHOD | 547 | ||
RESULTS AND DISCUSSION | 549 | ||
Transmembrane flux and osmotic pressure | 549 | ||
Resistance and concentration polarization | 553 | ||
REFERENCES | 555 | ||
P and N in solids from manure separation: separation efficiency and particle size distribution | 557 | ||
INTRODUCTION | 557 | ||
MATERIALS AND METHODS | 558 | ||
RESULTS AND DISCUSSION | 560 | ||
Separation efficiencies | 560 | ||
P distribution in particle sizes | 562 | ||
CONCLUSION | 563 | ||
REFERENCES | 564 | ||
Treating solid dairy manure by using the microwave-enhanced advanced oxidation process | 565 | ||
INTRODUCTION | 565 | ||
MATERIALS AND METHODS | 567 | ||
Apparatus and substrate | 567 | ||
Experimental design | 567 | ||
Part 1 | 568 | ||
Part 2 | 568 | ||
Analytical procedures | 569 | ||
RESULTS AND DISCUSSIONS | 569 | ||
Part 1 | 570 | ||
Soluble phosphate | 570 | ||
Ammonia and NO&subx | 571 | ||
Volatile fatty acids | 571 | ||
Soluble COD | 572 | ||
Part 2 | 573 | ||
REFERENCES | 575 | ||
Profitable recovery of phosphorus from sewage sludge and meat & bone meal by the Mephrec process – a new means of thermal sludge and ash treatment | 577 | ||
PARTICULAR FEATURES OF THE MEPHREC PROCESS | 577 | ||
Input material | 577 | ||
Equipment | 578 | ||
Investment | 578 | ||
Smelting technology | 578 | ||
RECENT RESULTS OF THE SMELTING-GASIFICATION WITH THE MEPHREC PROCESS | 579 | ||
Slag formation | 579 | ||
Basic slag components | 579 | ||
P-contents of different Mephrec slags | 579 | ||
Heavy metal content of Mephrec slags | 580 | ||
Empirical evaluation of nutrient recovery using Seaborne technology at the wastewater treatment plant Gifhorn | 581 | ||
INTRODUCTION | 581 | ||
SEABORNE TECHNOLOGY AT THE WASTEWATER TREATMENT PLANT GIFHORN | 582 | ||
EVALUATION METHODS | 583 | ||
RESULTS AND DISCUSSION | 585 | ||
Metal and heavy metal distribution | 585 | ||
COD, TOC distribution | 588 | ||
Mass balance of the main compounds | 590 | ||
CONCLUSION | 590 | ||
REFERENCES | 591 | ||
Sewage treatment to remove ammonium ions by struvite precipitation | 593 | ||
INTRODUCTION | 593 | ||
RESULTS AND DISCUSSION | 594 | ||
CONCLUSIONS | 603 | ||
ACKNOWLEDGEMENT | 603 | ||
REFERENCES | 603 | ||
Full-scale plant test using sewage sludge ash as raw material for phosphorus production | 605 | ||
INTRODUCTION | 605 | ||
PROCESS DESCRIPTION | 606 | ||
INFLUENCES ON ASH QUALITY | 607 | ||
FULL SCALE TESTS | 609 | ||
CONCLUSIONS AND OUTLOOK | 610 | ||
REFERENCES | 612 | ||
Phosphorous recovery and nitrogen removal from wastewater using BioIronTech process | 613 | ||
INTRODUCTION | 613 | ||
The recovery of phosphorus from reject water | 613 | ||
The BioIronTech process | 614 | ||
The potential application of BioIronTech process for the recovery of phosphate and removal of nitrogen from reject water | 615 | ||
ANAEROBIC TREATMENT OF REJECT WATER USING THE BIORONTECH PROCESS | 616 | ||
The components of the system | 616 | ||
The ferrous production from the iron ore | 617 | ||
Organics and nitrogen removal from reject water using BioIronTech process | 617 | ||
Effect of nitrate and organic acids on the phosphate recovery from reject water | 619 | ||
CONCLUSIONS | 619 | ||
REFERENCES | 620 | ||
Phosphorus speciation of sewage sludge ashes and potential for fertilizer production | 623 | ||
INTRODUCTION | 623 | ||
MATERIALS AND METHODS | 624 | ||
RESULTS, PRELIMENARY DATA AND DISCUSSION | 624 | ||
OUTLOOK | 627 | ||
REFERENCES | 627 | ||
Savings from integration of centrate ammonia reduction with BNR operation: simulation of single-sludge and two-sludge plant operation | 629 | ||
INTRODUCTION | 629 | ||
BACKGROUND AND CONDITIONS MODELED | 630 | ||
FINDINGS | 631 | ||
Single-sludge plant | 633 | ||
Two-sludge plant | 634 | ||
CONCLUSION | 635 | ||
REFERENCES | 636 | ||
The use of phosphorus-saturated ochre as a fertiliser | 637 | ||
INTRODUCTION | 637 | ||
OCHRE AS A PHOSPHORUS ADSORBENT | 638 | ||
Laboratory experiments | 639 | ||
Ochre as a filter substrate | 639 | ||
Ongoing research on the use of ochre as a filter substrate | 641 | ||
USE OF PHOSPHORUS-SATURATED OCHRE AS A FERTILISER | 641 | ||
Materials and methods | 642 | ||
Pot experiments | 642 | ||
Field trials | 642 | ||
Results | 643 | ||
Soil P concentration | 643 | ||
Plant response | 644 | ||
Potentially toxic elements | 645 | ||
CONCLUSIONS | 645 | ||
ACKNOWLEDGEMENTS | 646 | ||
REFERENCES | 646 | ||
Volatile Fatty Acid (VFA) and nutrient recovery from biomass fermentation | 649 | ||
INTRODUCTION | 649 | ||
MATERIAL AND METHODS | 650 | ||
Experiment approach | 650 | ||
Phosphorus recovery via struvite formation | 651 | ||
Analytical procedure | 651 | ||
RESULTS AND DISCUSSION | 652 | ||
VFA production and solids reduction | 652 | ||
Nutrient recovery | 653 | ||
Solubilisation of P and N | 653 | ||
Struvite formation test | 654 | ||
CONCLUSION | 657 | ||
ACKNOWLEDGEMENT | 657 | ||
REFERENCES | 657 | ||
Phosphorus recovery from sewage sludge ash by a wet-chemical process | 659 | ||
INTRODUCTION | 659 | ||
LEACHING THE ASH | 659 | ||
Characterisation of the ash material | 660 | ||
General leaching investigations | 660 | ||
SOLVENT EXTRACTION | 661 | ||
Solvent extraction principles | 661 | ||
Chemical reactions involved using Alamine&supreg; 336 | 664 | ||
Laboratory-scale solvent extraction experiments | 665 | ||
PRECIPITATION | 667 | ||
Precipitation of calcium (magnesium-) phosphate product and separation of aluminium | 667 | ||
Preparation of the phosphorus product | 670 | ||
Product quality | 670 | ||
CONCLUSIONS | 671 | ||
ACKNOWLEDGEMENTS | 672 | ||
REFERENCES | 672 | ||
Phosphorus recovery from sewage sludge ash: possibilities and limitations of wet chemical technologies | 673 | ||
INTRODUCTION | 673 | ||
MATERIAL AND METHODS | 674 | ||
Origin and Composition of the sewage sludge ashes | 674 | ||
Thermal treatment of mixtures of pure substances | 676 | ||
Elution Tests | 676 | ||
Separation of Phosphorus and Metals via Sequential Increase of the pH-value | 676 | ||
Separation of Phosphorus and Metals via Nanofiltration | 677 | ||
RESULTS AND DISCUSSION | 677 | ||
Thermal Treatment of Mixtures of Pure Substances | 677 | ||
Elution Tests | 678 | ||
Separation of Phosphorus and Metals via Sequential Increase of the pH-value | 680 | ||
Separation of Phosphorus and Metals via Nanofiltration | 682 | ||
CONCLUSIONS | 682 | ||
ACKNOWLEDGEMENT | 683 | ||
REFERENCES | 684 | ||
Phosphate adsorption from sewage sludge filtrate using Zinc-Aluminium layered double hydroxides | 685 | ||
INTRODUCTION | 685 | ||
MATERIALS AND METHODS | 687 | ||
Preparation of LDHs | 687 | ||
Phosphate adsorption from sewage sludge filtrate | 687 | ||
Effect of pH on phosphate adsorption | 687 | ||
Study of adsorption isotherm | 688 | ||
Study of phosphate desorption | 688 | ||
Analysis | 688 | ||
Characterization of LDHs | 688 | ||
Phosphate measurement | 689 | ||
RESULTS AND DISCUSSION | 689 | ||
Parameters affecting phosphate adsorption from sewage sludge filtrate by LDHs | 689 | ||
Metal compositon | 689 | ||
Zn/Al molar ratio | 690 | ||
Calcination | 691 | ||
pH | 692 | ||
Adsorption kinetics | 694 | ||
Adsorption isotherm | 694 | ||
Phosphate desorption | 696 | ||
CONCLUSIONS | 697 | ||
ACKNOWLEDGEMENTS | 698 | ||
REFERENCES | 698 | ||
Urine reuse as fertilizer for bamboo plantations | 701 | ||
INTRODUCTION | 701 | ||
MATERIALS AND METHODS | 703 | ||
The experimental set up | 703 | ||
The analytical method | 704 | ||
Measured parameters and performed analyses | 705 | ||
RESULTS AND DISCUSSION | 705 | ||
The biomass production | 705 | ||
TOC removal through urine application – soil pH and conductivity (salts concentration) | 706 | ||
Nutrient loading rate and nutrient uptake N and P | 708 | ||
CONCLUSION | 708 | ||
REFERENCES | 709 | ||
Ammonium absorption in reject water using vermiculite | 711 | ||
ABSORPTION EXPERIMENTS | 711 | ||
Analytical procedures | 712 | ||
The effect of temperature | 712 | ||
The stirring experiment | 712 | ||
Results | 713 | ||
The ammonium nitrogen content in the reject water | 713 | ||
The ammonium nitrogen content in the vermiculite | 714 | ||
GREENHOUSE EXPERIMENT 1: AUGUST – DECEMBER 2004 | 714 | ||
Materials and methods | 714 | ||
Growing conditions | 714 | ||
Results | 715 | ||
Seedling weight | 715 | ||
Needle nutrient content | 716 | ||
GREENHOUSE EXPERIMENT 2: APRIL – AUGUST 2005 | 716 | ||
Materials and Methods | 716 | ||
Growing conditions | 716 | ||
Results | 717 | ||
Seedling weight | 717 | ||
Needle nutrient concentration | 718 | ||
ACKNOWLEDGEMENT | 719 | ||
REFERENCE | 719 | ||
Alternating anoxic-aerobic process for nitrogen recovery from wastewater in a biofilm reactor | 721 | ||
INTRODUCTION | 721 | ||
MATERIALS AND METHODS | 723 | ||
Description of the pilot-plant and the experimental set-up | 723 | ||
RESULTS AND DISCUSSION | 724 | ||
Removal of organics | 724 | ||
Nitrogen transformations | 729 | ||
Process application | 730 | ||
CONCLUSIONS | 731 | ||
REFERENCES | 732 | ||
Air stripping of ammonia from anaerobic digestate | 733 | ||
INTRODUCTION | 733 | ||
MATERIALS AND METHODS | 735 | ||
Anaerobic digestion plant | 735 | ||
Pre-treatment of the anaerobic digestate | 735 | ||
Precipitation with lime milk | 735 | ||
Elimination of CO&sub2 with sulphuric acid and pH adjustment | 736 | ||
Stripping of carbon dioxide in bubble reactors | 736 | ||
Stripping of ammonia | 736 | ||
Stripping of ammonia in bubble reactors | 736 | ||
Air stripping of ammonia with a stripping column | 736 | ||
RESULTS AND DISCUSSION | 738 | ||
Pretreatment | 738 | ||
Precipitation with lime milk | 738 | ||
Stripping of carbon dioxide | 738 | ||
Adjustment of the pH | 739 | ||
Stripping of ammonia | 741 | ||
Stripping of ammonia in bottles | 741 | ||
Air stripping of ammonia with a stripping column | 745 | ||
Setting of flow conditions | 745 | ||
Influence of temperature | 747 | ||
Influence of pH | 747 | ||
CONCLUSION | 748 | ||
ACKNOWLEDGEMENT | 749 | ||
REFERENCES | 749 | ||
Effect of air temperature and air humidity on mass transfer coefficient for volume reduction and urine concentration | 751 | ||
INTRODUCTION | 751 | ||
CASE STUDY OF SOUTHERN PAKISTAN | 752 | ||
Comparison of cost of commercially available fertilizer with transportation cost of equivalent quantity of urine for paddy cultivation | 753 | ||
Nitrogen fertilizer | 753 | ||
Phosphorus fertilizer | 755 | ||
Potassium fertilizer | 755 | ||
Summary | 756 | ||
PREVIOUS VOLUME REDUCTION METHODS | 756 | ||
MATERIAL AND METHOD | 757 | ||
Design of experiments | 757 | ||
Water supply rate (WSR) experiments | 757 | ||
Material | 757 | ||
Method | 758 | ||
Evaporation rate (ER) experiments | 758 | ||
Material | 759 | ||
Method | 759 | ||
Experimental conditions | 759 | ||
Model for design of vertical sheets for OVRS | 759 | ||
RESULTS AND DISCUSSION | 760 | ||
WSR experiments | 760 | ||
ER Experiments | 760 | ||
Effect of air temperature on mass transfer coefficient | 761 | ||
Effect of air humidity on mass transfer coefficient: | 762 | ||
ESTIMATION OF VERTICAL SHEET FOR OVRS | 764 | ||
REFERENCES | 765 | ||
Phosphorus cycling by using biomass ashes | 767 | ||
INTRODUCTION | 767 | ||
MATERIALS AND METHODS | 768 | ||
RESULTS AND DISCUSSION | 770 | ||
Nutrient content and P availability in different biomass ashes | 770 | ||
Effect of ash application on dry matter yield and P uptake of tested catch crops | 770 | ||
Soil pH and soil P parameters as affected by ash application | 771 | ||
CONCLUSIONS | 773 | ||
REFERENCES | 774 | ||
Phosphorus recovery from high-phosphorus containing excess sludge in an anaerobic-oxic-anoxic process by using the combination of ozonation and phosphorus adsorbent | 777 | ||
INTRODUCTION | 777 | ||
MATERIALS AND METHODS | 778 | ||
Reactor design and operation | 778 | ||
Analytical procedures | 781 | ||
RESULTS AND DISCUSSION | 781 | ||
Reactor operation | 781 | ||
Phosphorus recovery from excess sludge | 782 | ||
Feasibility of the A/O/A system | 783 | ||
CONCLUSIONS | 784 | ||
REFERENCES | 785 | ||
Struvite control techniques in an enhanced biological phosphorus removal plant | 787 | ||
INTRODUCTION | 787 | ||
Transition to biological phosphorus removal | 788 | ||
Struvite appears | 788 | ||
Material testing | 788 | ||
pH adjustment | 789 | ||
Centrate storage system design | 791 | ||
Digester struvite issues | 791 | ||
Future plans for struvite recovery | 792 | ||
CONCLUSION | 793 | ||
REFERENCE | 793 | ||
A novel waste sludge operation to minimize uncontrolled phosphorus precipitation and maximize the phosphorus recovery: a case study in Tarragona, Spain | 795 | ||
INTRODUCTION AND BACKGROUND | 795 | ||
MATERIALS AND METHODS | 797 | ||
Mathematical model | 797 | ||
RESULTS AND DISCUSSION | 797 | ||
Sludge line modelization | 797 | ||
Proposal of a sludge management modification | 798 | ||
Control system | 802 | ||
CONCLUSIONS | 803 | ||
ACKNOWLEDGMENTS | 803 | ||
REFERENCES | 803 | ||
Study of uncontrolled precipitation problems in Tarragona WWTP (Spain) | 805 | ||
INTRODUCTION | 805 | ||
MATERIALS AND METHODS | 806 | ||
Tarragona WWTP | 806 | ||
Analytical campaign | 807 | ||
Mass balance | 808 | ||
RESULTS AND DISCUSSION | 809 | ||
Gravity thickening | 809 | ||
DAF thickening | 809 | ||
Anaerobic digestion | 811 | ||
Distribution of precipitates in the digester | 812 | ||
CONCLUSIONS | 813 | ||
ACKNOWLEDGMENTS | 813 | ||
REFERENCES | 813 | ||
Phosphorus recovery in EBPR systems by struvite crystallization | 815 | ||
NOMENCLATURE | 815 | ||
Subscripts | 816 | ||
INTRODUCTION | 816 | ||
MATERIALS AND METHODS | 817 | ||
Pilot plants description | 817 | ||
Experimental procedure | 818 | ||
Analytical methods | 818 | ||
Calculation of phosphorus precipitation in digestion and crystallization processes | 819 | ||
Phosphorus precipitation assessment in the digester | 819 | ||
Phosphorus precipitation assessment in the crystallization process | 819 | ||
RESULTS AND DISCUSSION | 819 | ||
Phosphorus precipitation in the digester | 820 | ||
Phosphorus recovery in the crystallization process | 821 | ||
Evaluation of global phosphorus recovery | 822 | ||
CONCLUSIONS | 823 | ||
REFERENCES | 824 | ||
Index | 827 |