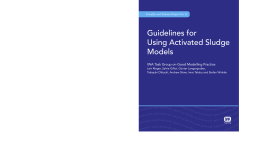
BOOK
Guidelines for Using Activated Sludge Models
Leiv Rieger | Sylvie Gillot | Guenter Langergraber | Takayuki Ohtsuki | Andrew Shaw | Imre Takacs | Stefan Winkler
(2012)
Additional Information
Book Details
Abstract
Mathematical modelling of activated sludge systems is used widely for plant design, optimisation, training, controller design and research. The quality of simulation studies varies depending on the project objectives, finances and expertise available. Consideration has to be given to the model accuracy and the amount of time required carrying out a simulation study to produce the desired accuracy. Inconsistent approaches and insufficient documentation make quality assessment and comparison of simulation results difficult or almost impossible. A general framework for the application of activated sludge models is needed in order to overcome these obstacles.Â
The genesis of the Good Modelling Practice (GMP) Task Group lies in a workshop held at the 4th IWA World Water Congress in Marrakech, Morocco where members of research groups active in wastewater treatment modelling came together to develop plans to synthesize the best practices of modellers from all over the world. The most cited protocols were included in the work, amongst others from: HSG (Hochschulgruppe), STOWA, BIOMATH and WERF. The goal of the group is to set up an internationally accepted framework to deal with the ASM type models in practice. This framework shall make modelling more straightforward and systematic to use especially for practitioners and consultants. Additionally, it shall help to define quality levels for simulation results, a procedure to assess this quality and to assist in the proper use of the models. The framework will describe a methodology for goal-oriented application of activated sludge models demonstrated by means of a concise guideline about the procedure of a simulation study and some illustrative case studies. The case studies shall give examples for the required data quality and quantity and the effort for calibration/validation with respect to a defined goal. The final report will include an extended appendix with additional information and details of methodologies.Â
Additional features in Guidelines for Using Activated Sludge Models include a chapter on modelling industrial wastewater, an overview on the history, current practice and future of activated sludge modelling and several explanatory case studies. It can be used as an introductory book to learn about Good Modelling Practice (GMP) in activated sludge modelling and will be of special interest for process engineers who have no prior knowledge of modelling or for lecturers who need a textbook for their students. The STR can also be used as a modelling reference book and includes an extended appendix with additional information and details of methodologies.
Scientific and Technical Report No. 22
Table of Contents
Section Title | Page | Action | Price |
---|---|---|---|
Cover page | 1 | ||
Half-title page | 2 | ||
Title page | 3 | ||
Copyright page | 4 | ||
Contents | 5 | ||
Acknowledgements | 11 | ||
List of GMP Task Group Members | 12 | ||
Preface | 13 | ||
THE GOOD MODELLING PRACTICE (GMP) TASK GROUP | 13 | ||
THE ACTIVITIES | 13 | ||
THE WORK | 14 | ||
THE SCIENTIFIC & TECHNICAL REPORT | 14 | ||
WHAT STAYS? | 15 | ||
Chapter 1 | 16 | ||
Introduction | 16 | ||
1.1 RATIONALE | 16 | ||
1.2 SCOPE OF REPORT | 17 | ||
1.3 STRUCTURE OF THE STR | 17 | ||
1.4 MODEL NOTATION, NOMENCLATURE, UNITS | 18 | ||
1.5 SUGGESTED READING | 18 | ||
Chapter 2 | 20 | ||
State-of-the-art in activated sludge modelling | 20 | ||
Short summary | 20 | ||
2.1 REPRESENTING REALITY IN MODELS | 20 | ||
2.2 A BRIEF HISTORY OF ACTIVATED SLUDGE MODELLING | 22 | ||
2.3 REVIEW OF PRACTICE | 24 | ||
2.3.1 Overview of current practice | 24 | ||
2.3.2 Discussed biokinetic models | 26 | ||
2.3.3 Stakeholders in modelling projects | 26 | ||
2.3.4 The role of models in the life cycle of a plant | 26 | ||
2.4 THE FUTURE OF ACTIVATED SLUDGE MODELLING | 27 | ||
2.4.1 Driving forces in wastewater treatment | 27 | ||
2.4.2 Trends and research needs | 28 | ||
FURTHER READING | 29 | ||
Chapter 3 | 30 | ||
Available protocols | 30 | ||
Short summary | 30 | ||
3.1 INTRODUCTION | 30 | ||
3.1.1 Benefits of modelling guidelines | 30 | ||
3.1.2 Potential risks of standardisation | 31 | ||
3.2 EXISTING GUIDELINES | 31 | ||
3.2.1 General modelling guidelines | 31 | ||
3.2.2 Wastewater-oriented guidelines | 31 | ||
3.2.3 Analysis of existing guidelines | 32 | ||
3.2.3.1 Short description of guidelines | 32 | ||
Chapter 4 | 39 | ||
The GMP Unified Protocol | 39 | ||
Short summary | 39 | ||
4.1 TOWARDS A UNIFIED PROTOCOL | 39 | ||
4.2 THE GMP UNIFIED PROTOCOL- STRUCTURED OVERVIEW | 40 | ||
Chapter 5 | 43 | ||
Unified Protocol steps | 43 | ||
Short summary | 43 | ||
Chapter 5.1 | 44 | ||
Project definition | 44 | ||
5.1.1 INTRODUCTION | 44 | ||
5.1.2 PROCEDURE | 44 | ||
5.1.2.1 Problem statement | 44 | ||
5.1.2.2 Objectives | 45 | ||
5.1.2.3 Requirements | 46 | ||
5.1.2.4 Client agreement | 46 | ||
5.1.3 DELIVERABLES | 46 | ||
FURTHER READING | 47 | ||
Chapter 5.2 | 48 | ||
Data collection and reconciliation | 48 | ||
5.2.1 INTRODUCTION | 48 | ||
5.2.2 PROCEDURE | 48 | ||
5.2.3 UNDERSTANDING THE PLANT | 49 | ||
5.2.4 COLLECTION OF EXISTING DATA | 50 | ||
5.2.4.1 Data types | 50 | ||
5.2.4.2 Data sources | 52 | ||
5.2.4.3 General data requirements | 52 | ||
5.2.5 DATA ANALYSIS AND RECONCILIATION | 57 | ||
5.2.5.1 Fundamentals in data quality control | 57 | ||
5.2.5.2 GMP data reconciliation procedure | 58 | ||
5.2.5.3 Step 1: Fault Detection | 59 | ||
5.2.5.4 Step 2: Fault Isolation | 65 | ||
5.2.5.5 Step 3: Fault Identification | 65 | ||
5.2.5.6 Step 4: Data reconciliation | 66 | ||
5.2.6 ADDITIONAL MEASUREMENT CAMPAIGNS | 68 | ||
5.2.6.1 Client agreement | 68 | ||
5.2.7 FINAL CLIENT AGREEMENT | 69 | ||
5.2.8 DELIVERABLES | 69 | ||
FURTHER READING | 69 | ||
Chapter 5.3 | 71 | ||
Plant model set-up | 71 | ||
5.3.1 INTRODUCTION | 71 | ||
5.3.2 PROCEDURE | 71 | ||
5.3.2.1 Plant layout | 71 | ||
5.3.2.2 Sub-model structure | 73 | ||
5.3.2.3 Connections to databases | 74 | ||
5.3.2.4 Graphs and tables | 74 | ||
5.3.2.5 Model checks | 74 | ||
5.3.2.6 Stakeholder agreement | 75 | ||
5.3.3 DELIVERABLES | 75 | ||
5.3.4 SUB-MODEL SELECTION | 75 | ||
5.3.4.1 Flow scheme | 76 | ||
5.3.4.2 Selection of clarifier models | 77 | ||
5.3.4.3 Biokinetic models | 78 | ||
5.3.4.4 Input models | 80 | ||
FURTHER READING | 81 | ||
Chapter 5.4 | 82 | ||
Calibration and validation | 82 | ||
5.4.1 INTRODUCTION | 82 | ||
5.4.2 PROCEDURE | 83 | ||
5.4.2.1 Model prediction quality | 83 | ||
5.4.2.2 Refinement of the stop criteria and validation tests | 83 | ||
5.4.2.3 Initial run of the model | 84 | ||
5.4.2.4 Calibration | 85 | ||
5.4.2.5 Validation | 88 | ||
5.4.3 DELIVERABLES | 88 | ||
FURTHER READING | 88 | ||
Chapter 5.5 | 89 | ||
Simulation and result interpretation | 89 | ||
5.5.1 INTRODUCTION | 89 | ||
5.5.2 PROCEDURE | 89 | ||
5.5.2.1 Define scenarios | 89 | ||
5.5.2.2 Set up plant models for scenarios | 93 | ||
5.5.2.3 Run simulations | 94 | ||
5.5.2.4 Present and interpret results | 96 | ||
5.5.2.5 Reporting | 98 | ||
5.5.2.6 Client agreement | 100 | ||
5.5.3 TYPICAL PITFALLS | 100 | ||
5.5.4 DELIVERABLES | 100 | ||
FURTHER READING | 101 | ||
Chapter 6 | 102 | ||
The GMP Application Matrix | 102 | ||
Short summary | 102 | ||
6.1 INTRODUCTION | 102 | ||
6.2 EXAMPLE APPLICATIONS | 103 | ||
(A) Design examples | 103 | ||
(1) Calculate sludge production | 103 | ||
(2) Design aeration system | 104 | ||
(3) Develop a process configuration for nitrogen removal | 104 | ||
(4) Develop a process configuration for phosphorus removal | 104 | ||
(5) Assess plant capacity for nitrogen removal | 104 | ||
(6) Design a treatment system to meet peak effluent nitrogen limits | 104 | ||
(B) Operation examples | 105 | ||
(7) Optimise aeration control | 105 | ||
(8) Test effect of taking tanks out of service | 105 | ||
(9) Use model to develop sludge wastage strategy | 105 | ||
(10) Develop a strategy to handle storm flows | 105 | ||
(C) Training examples | 105 | ||
(11) Develop a general model for process understanding | 105 | ||
(12) Develop a site specific model for operator training | 105 | ||
(D) Industrial examples | 106 | ||
(13) Develop a process configuration for nitrogen removal treating waste from a food production factory (soy sauce) | 106 | ||
(14) Assess acceptability of new influent at a petrochemical site | 106 | ||
6.3 MATRIX SCORING SYSTEM | 106 | ||
6.4 THE APPLICATION MATRIX | 108 | ||
6.5 OTHER IMPORTANT CONSIDERATIONS | 110 | ||
6.6 GUIDANCE BASED ON THE APPLICATION MATRIX | 110 | ||
6.6.1 Stop criteria for calibration | 110 | ||
6.6.2 Data requirements | 112 | ||
6.6.3 Selecting scenarios for analysis | 114 | ||
6.6.4 Using the GMP Unified Protocol: benefits and averted risks | 116 | ||
Chapter 7 | 118 | ||
Using the GMP Unified Protocol by example | 118 | ||
Short summary | 118 | ||
7.1 INTRODUCTION | 118 | ||
7.2 CALCULATE SLUDGE PRODUCTION | 118 | ||
UP Step 1: Project definition | 118 | ||
UP Step 2: Data collection and reconciliation | 119 | ||
UP Step 3: Plant model set-up | 120 | ||
UP Step 4: Calibration and validation | 120 | ||
Sludge production | 120 | ||
Clarifier | 122 | ||
UP Step 5: Simulation and result interpretation | 124 | ||
7.3 ASSESS PLANT CAPACITY FOR NITROGEN REMOVAL | 124 | ||
UP Step 1: Project definition | 124 | ||
UP Step 2: Data collection and reconciliation | 125 | ||
UP Step 3: Plant model set-up | 125 | ||
UP Step 4: Calibration and validation | 125 | ||
Nitrification | 125 | ||
Denitrification | 127 | ||
Oxygen transfer | 128 | ||
UP Step 5: Simulation and result interpretation | 129 | ||
7.4 DEVELOP A SITE SPECIFIC MODEL FOR OPERATOR TRAINING | 130 | ||
UP Step 1: Project definition | 130 | ||
UP Step 2: Data collection and reconciliation | 131 | ||
UP Step 3: Plant model set-up | 131 | ||
UP Step 4: Calibration and validation | 131 | ||
UP Step 5: Simulation and result interpretation | 132 | ||
7.5 A PLANT WIDE PROCESS MODEL FOR BEENYUP WWTP DESIGN UPGRADE | 136 | ||
UP Step 1: Project definition | 136 | ||
Background | 136 | ||
Modelling objectives | 136 | ||
Requirements | 136 | ||
UP Step 2: Data collection and reconciliation | 136 | ||
Influent flow validation | 136 | ||
Influent loading rate | 137 | ||
Influent characterisation | 137 | ||
UP Step 3: Plant model set-up | 138 | ||
UP Step 4: Calibration and validation | 139 | ||
UP Step 5: Simulation and result interpretation | 139 | ||
Conclusions | 140 | ||
Chapter 8 | 141 | ||
Use of activated sludge models for industrial wastewater | 141 | ||
Short summary | 141 | ||
8.1 INTRODUCTION | 141 | ||
8.2 LINKS TO UNIFIED PROTOCOL STEPS | 142 | ||
8.3 WASTEWATER SOURCES | 143 | ||
8.3.1 Wastewater composition with few specific contaminants | 144 | ||
8.3.2 Multiple wastewater sources of different nature | 145 | ||
8.3.3 Source control | 146 | ||
8.4 INFLUENT COMPONENTS | 146 | ||
8.4.1 Unbiodegradable fractions | 146 | ||
8.4.1.1 Soluble unbiodegradable fractions | 146 | ||
8.4.1.2 Particulate unbiodegradable fractions | 147 | ||
8.4.2 Biodegradable organic fractions | 147 | ||
8.4.2.1 Particulate very slowly biodegradable fractions | 150 | ||
8.4.3 Nitrogen fractions | 151 | ||
8.4.4 Inhibitory and toxic components | 151 | ||
8.4.5 Physico-chemical characteristics of specific chemicals | 153 | ||
8.4.6 Additional nutrient and essential metal limitations | 154 | ||
8.5 IMPACT ON BIOMASS COMPOSITION | 154 | ||
8.5.1 Varying biomass yields | 155 | ||
8.5.2 Acclimation and activity loss (decay) | 155 | ||
8.6 VARYING OPERATIONAL CONDITIONS | 156 | ||
8.6.1 Modelling temperature dependency | 156 | ||
8.6.2 Modelling pH effects | 157 | ||
8.7 EXPERIMENTAL METHODS FOR INDUSTRIAL APPLICATIONS | 158 | ||
8.8 PITFALLS AND SUGGESTIONS IN INDUSTRIAL APPLICATIONS | 158 | ||
FURTHER READING | 159 | ||
Chapter 9 | 160 | ||
Frequently asked questions | 160 | ||
Glossary | 164 | ||
Appendix A | 173 | ||
Sub-model descriptions | 173 | ||
A.1 HYDRAULIC AND TRANSPORT MODELS | 173 | ||
A.1.1 Reactor models | 173 | ||
A.1.2 Flow scheme | 173 | ||
A.1.2.1 Return Activated Sludge (RAS) and Internal Recycle (IR) flows | 174 | ||
A.1.2.2 Waste activated sludge (WAS) flow | 174 | ||
A.1.2.3 Flow splitter | 175 | ||
A.2 CLARIFIER MODELS | 175 | ||
A.2.1 Overview | 175 | ||
A.2.2 Selection of clarifier models | 176 | ||
A.2.3 Reactive clarifier models | 176 | ||
A.3 BIOKINETIC MODELS | 176 | ||
A.3.1 Temperature dependency of parameters (Arrhenius equation) | 176 | ||
A.4 INPUT MODELS | 177 | ||
A.4.1 Influent model | 177 | ||
A.4.2 Concepts for influent fractionation | 177 | ||
A.4.2.1 COD fractions | 177 | ||
A.4.2.2 Nitrogen and phosphorus fractions | 178 | ||
A.4.2.3 Suspended solids fractions | 181 | ||
A.5 pH AND ALKALINITY | 182 | ||
A.6 OUTPUT MODELS | 182 | ||
A.7 AERATION MODELS | 183 | ||
A.7.1 Oxygen transfer model | 183 | ||
A.7.2 Aeration control model | 184 | ||
A.7.2.1 DO control loops | 184 | ||
A.7.2.2 Reactor definition | 184 | ||
A.7.2.3 Location of DO sensors | 184 | ||
A.7.3 Detailed aeration system model | 185 | ||
A.8 PHOSPHORUS PRECIPITATION MODEL | 185 | ||
REFERENCES | 185 | ||
Appendix B | 187 | ||
Representation of biokinetic models - the Gujer Matrix | 187 | ||
B.1 INTRODUCTION | 187 | ||
B.2 MATRIX FORMAT | 187 | ||
B.2.1 The structure of the Gujer Matrix | 188 | ||
REFERENCES | 193 | ||
Appendix C | 194 | ||
The numerical engine -solvers for beginners | 194 | ||
C.1.1 STEADY-STATE SOLVERS | 195 | ||
C.1.2 DYNAMIC SOLVERS | 195 | ||
C.1.3 SIMULATION SPEED AND TIME STEPS | 195 | ||
C.1.4 ALGEBRAIC SOLVERS | 195 | ||
C.1.5 OPTIMISERS | 196 | ||
Appendix D1 | 197 | ||
New framework for standardized notation in wastewater treatment modelling | 197 | ||
ABSTRACT | 197 | ||
D1.1 INTRODUCTION | 198 | ||
D1.1.1 Motivation | 199 | ||
D1.2 GENERAL FRAMEWORK | 200 | ||
D1.2.1 Naming system established for the new notation | 200 | ||
D1.3 STATE VARIABLES | 200 | ||
D1.3.1 Specific problems encountered | 200 | ||
D1.3.2 Framework | 202 | ||
D1.3.3 Notational procedure | 203 | ||
D1.3.3.1 Naming lumped variables | 205 | ||
D1.4. MODEL PARAMETERS | 206 | ||
D1.4.1 Stoichiometric parameters | 208 | ||
D1.4.1.1 Composition and fractionation coefficients | 209 | ||
D1.5.1 Kinetic parameters | 210 | ||
D1.5.1.1 Rate Coefficients and reduction factors | 210 | ||
D1.5.1.2 Saturation or inhibition coefficients | 211 | ||
D1.6 CONTRIBUTIONS OF THE NEW FRAMEWORK | 211 | ||
CONCLUSIONS | 212 | ||
Acknowledgements | 212 | ||
REFERENCES | 213 | ||
ADDITIONAL MATERIAL | 215 | ||
Appendix D2 | 218 | ||
Example Fractionation according to New Notation | 218 | ||
Appendix E | 220 | ||
A Systematic approach for model verification - application on seven published activated sludge models | 220 | ||
ABSTRACT | 220 | ||
E.1 INTRODUCTION | 221 | ||
E.2 HOW TO TRACK TYPING ERRORS AND INCONSISTENCIES IN MODEL DEVELOPMENT AND SOFTWARE IMPLEMENTATION | 221 | ||
E.2.1 How to track stoichiometric discontinuities | 221 | ||
E.2.2 How to track kinetic inconsistencies | 222 | ||
E.3 COMMON PUBLISHED ERRORS | 223 | ||
E.3.1 Rounding parameters | 223 | ||
E.3.2 Temperature adjustment of kinetic parameters | 223 | ||
E.3.3 Impact of alkalinity on kinetic rates | 224 | ||
E.4 TYPING ERRORS, INCONSISTENCIES AND GAPS IN PUBLISHED MODELS | 225 | ||
E.4.1 ASM1 (Henze et al. 2000) | 225 | ||
E.4.2 ASM2d (Henze et al. 2000b) | 225 | ||
E.4.3 ASM3 (Gujer et al. 2000) | 226 | ||
E.4.4 ASM3+ BioP (Rieger et al. 2001) | 226 | ||
E.4.5 ASM2d + TUD (Meijer, 2004) | 227 | ||
E.4.6 New general (Barker & Dold, 1997) | 227 | ||
E.4.7 UCTPHO+ (Hu et al. 2007) | 229 | ||
CONCLUSION | 232 | ||
Acknowledgments | 232 | ||
REFERENCES | 233 | ||
ADDITIONAL MATERIAL | 235 | ||
Appendix F | 237 | ||
Activated sludge modelling: Development and potential use of a practical applications database | 237 | ||
ABSTRACT | 237 | ||
F.1 INTRODUCTION | 238 | ||
F.1.1 Method | 238 | ||
F.1.1.1 Source of data | 238 | ||
F.1.1.2 Database description | 239 | ||
F.1.1.3 Database analysis | 239 | ||
F.2 RESULTS | 240 | ||
F.2.1 Modelling project characteristics | 240 | ||
F.2.2 ASM1 | 240 | ||
F.2.3 Discussion | 244 | ||
F.2.3.1 ASM2d | 245 | ||
F.2.3.2 Discussion | 247 | ||
F.3 GENERAL DISCUSSION | 248 | ||
F.3.1 Inter-model comparison | 248 | ||
F.3.2 Limitations of modelling project articles | 248 | ||
F.3.3 Potential use of the database | 248 | ||
CONCLUSION | 249 | ||
Acknowledgement | 249 | ||
REFERENCES | 249 | ||
ADDITIONAL MATERIAL | 251 | ||
Parameter definitions | 251 | ||
ASM3 + BioP | 251 | ||
Barker and Dold model | 257 | ||
DATABASE REFERENCES | 258 | ||
Appendix G | 261 | ||
Typical sources of measurement errors | 261 | ||
Appendix H | 265 | ||
Sources of uncertainties | 265 | ||
H.1 DEFINITIONS | 265 | ||
H.2 SOURCES OF UNCERTAINTY | 265 | ||
REFERENCES | 270 | ||
Appendix I | 271 | ||
Mass balancing | 271 | ||
I.1 TYPES OF MASS BALANCES | 271 | ||
I.2 APPLICATION TO SPECIFIC PROCESS VARIABLES | 272 | ||
I.3 BALANCING PERIOD | 272 | ||
I.4 UNCERTAINTY OF WWTP MASS BALANCES | 273 | ||
I.5 OVERLAPPING MASS BALANCES | 273 | ||
I.6 TYPICAL PITFALLS AND RECOMMENDATION | 274 | ||
REFERENCES | 274 | ||
References | 275 | ||
Index | 282 |