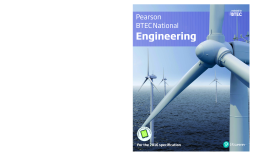
BOOK
BTEC Nationals Engineering Student Book
Andrew Buckenham | Gareth Thomson | Natalie Griffiths | Steve Singleton | Alan Serplus | Author
(2016)
Additional Information
Book Details
Abstract
The Student Book and ActiveBook has clearly laid out pages with a range of supportive features to aid learning and teaching:
• Getting to know your unit sections ensure learners understand the grading criteria and unit requirements.
• Getting ready for assessment sections focus on preparation for external assessment with guidance for learners on what to expect. Hints and tips will help them prepare for assessment and sample answers are provided for a range of question types including, short and long answer questions, all with a supporting commentary.
• Pause point features provide opportunities for learners to self-evaluate their learning at regular intervals. Each Pause point feature gives learners a Hint or Extend option to either revisit and reinforce the topic or encourage independent research or further study skills.
• Case study and Theory into practice features enable development of problem-solving skills and place the theory into real life situations learners could encounter.
• Assessment practice features provide scaffolded activities that help prepare learners for assessment. Within each assessment practice activity, a Plan, Do and Review section supports learners’ formative assessment by to making sure they fully understand what they are being asked to do, what their goals are and how to evaluate the task and consider how they could improve.
• Literacy and numeracy activities provide opportunities for reinforcement in these key areas, placing the skills into a children’s play, learning and development context.
• Dedicated Think future pages provide case studies from the industry, with a focus on aspects of skills development that can be put into practice in a real work environment and further study.
Table of Contents
Section Title | Page | Action | Price |
---|---|---|---|
Front Cover | Front Cover | ||
Contents | iii | ||
Introduction | iv | ||
Chapter 1: Engineering Principles | 1 | ||
A: Algebraic and trigonometric mathematical methods | 3 | ||
A1: Algebraic methods | 3 | ||
A2: Trigonometric methods | 13 | ||
B: Static engineering systems | 18 | ||
B1: Static engineering systems | 18 | ||
B2: Loaded components | 23 | ||
C: Dynamic engineering systems | 27 | ||
C1: Dynamic engineering systems | 27 | ||
D: Fluid and thermodynamic engineering systems | 34 | ||
D1: Fluid systems | 34 | ||
D2: Thermodynamic systems | 38 | ||
E: Static and direct current electricity and circuits | 46 | ||
E1: Static and direct current electricity | 46 | ||
E2: Direct current circuit theory | 49 | ||
E3: Direct current networks | 53 | ||
F: Magnetism and electromagnetic induction | 57 | ||
F1: Magnetism | 57 | ||
F2: Electromagnetic induction | 59 | ||
G: Single-phase alternating current | 62 | ||
Single-phase alternating current theory | 62 | ||
Chapter 2: Delivery of Engineering Processes Safely as a Team | 73 | ||
A: Examine common engineering processes to create products or deliver services safely and effectively as a team | 76 | ||
A1: Common engineering processes | 76 | ||
A2: Health and safety | 84 | ||
A3: Human factors | 87 | ||
B: Develop 2D computer-aided drawings that can be used in engineering processes | 89 | ||
B1: Principles of engineering drawing | 89 | ||
B2: Two-dimensional (2D) computer-aided drawing | 94 | ||
C: Carry out engineering processes safely to manufacture a product or to deliver a service effectively as a team | 96 | ||
C1: Principles of effective teams | 96 | ||
C2: Team set-up and organisation | 99 | ||
C3: Health and safety risk assessment | 100 | ||
C4: Preparation activities for batch manufacture or batch service delivery | 103 | ||
C5: Delivery of manufacturing or service engineering processes | 104 | ||
Chapter 3: Engineering Product Design and Manufacture | 109 | ||
A: Design triggers, challenges, constraints and opportunities, and materials and processes | 112 | ||
A1: Design triggers | 112 | ||
A2: Design challenges | 116 | ||
A3: Equipment-level and system‑level constraints and opportunities | 118 | ||
A4: Material properties | 120 | ||
A5: Mechanical power transmission | 125 | ||
A6: Manufacturing processes | 128 | ||
B: Interpreting a brief into operational requirements and analysing existing products | 134 | ||
B1: Design for a customer | 134 | ||
B2: Regulatory constraints and opportunities | 137 | ||
B3: Market analysis | 139 | ||
B4: Performance analysis | 140 | ||
B5: Manufacturing analysis | 143 | ||
C: Using an iterative process to design ideas and develop a modified product proposal | 145 | ||
C1: Design proposals | 145 | ||
C2: Communicating designs | 149 | ||
C3: Iterative development process | 152 | ||
D: Technical justification and validation of the design solution | 152 | ||
D1: Statistical methods | 152 | ||
D2: Validating designs | 161 | ||
Chapter 4: Applied Commercial and Quality Principles in Engineering | 169 | ||
A: Examine business functions and trade considerations that help engineering organisations thrive | 172 | ||
A1: Business functions | 172 | ||
A2: Trade considerations | 173 | ||
A3: Competitive advantage | 175 | ||
B: Explore activity-based costing as a method to control costs and to determine if an engineering product or service is profitable | 176 | ||
B1: Reasons for cost control | 176 | ||
B2: Activity-based costing method | 177 | ||
C: Explore how engineering organisations use quality systems and value management to create value | 180 | ||
C1: Quality systems | 180 | ||
C2: The principles and processes of value management | 183 | ||
Chapter 5: A Specialist Engineering Project | 189 | ||
A: Investigate an engineering project in a relevant specialist area | 192 | ||
A1: Project life cycle | 192 | ||
A2: Generating ideas and developing solutions | 194 | ||
A3: Feasibility study of solutions | 196 | ||
B: Develop project-management processes and a design solution for the specialist engineering project as undertaken in industry | 200 | ||
B1: Planning and monitoring | 200 | ||
B2: Risk and issue management | 204 | ||
B3: Technical specification | 205 | ||
B4: Design information | 206 | ||
C: Undertake the solution for a specialist engineering project and present the solution as undertaken in industry | 209 | ||
C1: Undertake and test the solution to the problem | 209 | ||
C2: Demonstration of relevant behaviours | 212 | ||
C3: Present a solution to the problem | 213 | ||
Chapter 6: Microcontroller Systems for Engineers | 219 | ||
A: Investigate typical microcontroller system hardware | 221 | ||
A1: Control hardware | 222 | ||
A2: Input devices | 227 | ||
A3: Output devices | 233 | ||
A4: Selecting hardware devices and system design | 238 | ||
A5: Assembling and operating a microcontroller system | 239 | ||
B: Programming techniques and coding | 239 | ||
B4: Numbering systems | 239 | ||
B1: Programming techniques | 243 | ||
B2: Coding constructs | 246 | ||
B3: Structured program design | 253 | ||
C: System development cycle | 267 | ||
C1: Development processes | 268 | ||
C2: Documentation | 269 | ||
Chapter 7: Calculus to Solve Engineering Problems | 287 | ||
A: Examine how differential calculus can be used to solve engineering problems | 290 | ||
A1: Functions, rate of change and gradient | 290 | ||
A2: Methods of differentiation | 292 | ||
A3: Numerical value of a derivative | 297 | ||
A4: Second derivative and turning points | 298 | ||
B: Examine how integral calculus can be used to solve engineering problems | 304 | ||
B1: Integration as the reverse/inverse of differentiation | 304 | ||
B2: Integration as a summating tool | 309 | ||
B3: Numerical integration | 312 | ||
C: Investigate the application of calculus to the solution of a defined specialist engineering problem | 316 | ||
C1: Thinking methods | 316 | ||
C2: Mathematical modelling of engineering problems | 317 | ||
C3: Problem specification and proposed solution | 317 | ||
C4: Solution implementation | 319 | ||
Chapter 8: Further Engineering Mathematics | 325 | ||
A: Examine how sequences and series can be used to solve engineering problems | 328 | ||
A1: Arithmetic and geometric progressions | 328 | ||
A2: Binomial expansion | 333 | ||
A3: Power series | 336 | ||
B: Examine how matrices and determinants can be used to solve engineering problems | 337 | ||
B1: Matrices | 337 | ||
B2: Determinants | 341 | ||
C: Examine how complex numbers can be used to solve engineering problems | 345 | ||
C1: Complex numbers | 345 | ||
D: Investigate how statistical and probability techniques can be used to solve engineering problems | 348 | ||
D1: Statistical techniques | 348 | ||
Chapter 10: Computer-Aided Design in Engineering | 359 | ||
A: Develop a three-dimensional computer-aided model of an engineered product that can be used as part of other engineering processes | 362 | ||
A1: 3D parametric modelling | 362 | ||
A2: Develop 3D components | 367 | ||
A3: Develop a 3D model | 368 | ||
A4: Output of drawings from a model | 370 | ||
B: Develop two-dimensional detailed computer-aided drawings of an engineered product that can be used as part of other engineering processes | 374 | ||
B1: 2D drawing commands | 374 | ||
B2: Development of 2D engineering drawings | 375 | ||
B3: Output of 2D drawings | 377 | ||
C: Develop a three-dimensional computer-aided model for a thin-walled product and a fabricated product that can be used as part of other engineering processes | 378 | ||
C1: 3D modelling commands | 378 | ||
C2: Development of 3D components | 379 | ||
C3: Development of a 3D model | 379 | ||
C4: Output of product drawings | 380 | ||
Chapter 19: Electronic Devices and Circuits | 383 | ||
A: Explore the safe operation and applications of analogue devices and circuits that form the building blocks of commercial circuits | 386 | ||
A1: Safe electronic working practices | 386 | ||
A2: Diode devices and diode-based circuits | 389 | ||
A3: Transistor devices and transistor-based circuits | 394 | ||
A4: Operational amplifier circuits | 400 | ||
B: Explore the safe operation and applications of digital logic devices and circuits that form the building blocks of commercial circuits | 406 | ||
B1: Logic gates and Boolean algebra | 406 | ||
B2: Combinational logic | 408 | ||
B3: Sequential logic circuits | 411 | ||
C: Review the development of analogue and digital electronic circuits and reflect on own performance | 414 | ||
Improving your own performance | 414 | ||
Chapter 25 Mechanical Behaviour of Metallic Materials | 419 | ||
A: Investigate the microstructures of metallic materials and the effects of processing on them and how these effects influence their mechanical properties | 422 | ||
A1: Types of ferrous metals and alloys | 422 | ||
A2: Types of non-ferrous metals and alloys | 424 | ||
A3: Mechanical properties of metallic materials | 427 | ||
A4: Grain structure of metallic materials | 429 | ||
A5: Effects of processing on the mechanical properties of metallic materials | 437 | ||
A6: Microstructure investigation of metallic materials | 442 | ||
B: Explore safely the mechanical properties of metallic materials and the impact of their in-service requirements | 444 | ||
B1: In-service requirements of metallic materials | 444 | ||
B2: Destructive test procedures | 444 | ||
B3: Non-destructive test procedures | 451 | ||
C: Explore the in-service failure of metallic components and consider improvements to their design | 454 | ||
C1: Ductile and brittle fracture | 455 | ||
C2: Creep failure | 456 | ||
C3: Fatigue failure | 458 | ||
C4: Corrosion mechanisms | 459 | ||
C5: Design considerations to help prevent component failure | 462 | ||
Glossary | 467 | ||
Index | 472 | ||
Back Cover | Back Cover |