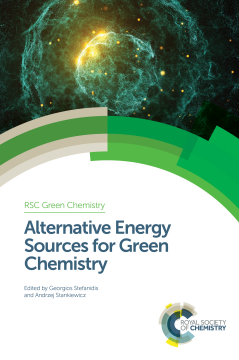
BOOK
Alternative Energy Sources for Green Chemistry
Georgios Stefanidis | Andrzej Stankiewicz
(2016)
Additional Information
Book Details
Abstract
The use of alternative energy forms and transfer mechanisms is one of the key approaches of process intensification. In recent years, significant amounts of research have been carried out in developing chemical processing technologies enhanced by plasma, electric and magnetic fields, electromagnetic and ultra-sound waves and high gravity fields. Discussing the broad impact of alternative energy transfer technologies on reactions, separations and materials synthesis, this book reports on recent breakthrough results in various application areas. It provides a comprehensive overview of the current developments in the field. The book enables industrialists, academics and postgraduates in alternative-energy based processing to see the potential of alternative energies for green chemistry and sustainability of chemical manufacturing.
Andrzej Stankiewicz is Professor of Process Intensification at Delft University of Technology, The Netherlands. His research focuses on the application of alternative energy forms and transfer mechanisms for the intensification of chemical reactions.
Giorgos Stefanidis is Assistant Professor at the Chair of Intensified Reaction and Separation Systems of Delft University of Technology, The Netherlands. His research focusses on process intensification, chemical reactor design and alternative energy forms.
Table of Contents
Section Title | Page | Action | Price |
---|---|---|---|
Cover | Cover | ||
Alternative Energy Sources for Green Chemistry | i | ||
Preface | vii | ||
Contents | xi | ||
Chapter 1 - Microwave-Assisted Green Organic Synthesis | 1 | ||
1.1 Introduction | 1 | ||
1.2 Solvent-Free Reactions | 4 | ||
1.3 Microwave Susceptors | 8 | ||
1.3.1 Graphite As a Microwave Susceptor | 8 | ||
1.3.2 Silicon Carbide (SiC) As a Microwave Susceptor | 10 | ||
1.3.3 Other Microwave Susceptors | 14 | ||
1.4 Reactions in Solution | 15 | ||
1.4.1 Reactions in Water | 16 | ||
1.4.2 Reactions in Ionic Liquids (ILs) | 19 | ||
1.4.3 Fluorous Chemistry | 22 | ||
1.5 Flow Chemistry | 24 | ||
1.6 Conclusions | 30 | ||
References | 30 | ||
Chapter 2 - Microwave-Assisted Plant Extraction Processes | 34 | ||
2.1 Introduction | 34 | ||
2.2 Microwave Heating Foundations | 35 | ||
2.2.1 Volumetric Heating Term | 37 | ||
2.3 Microwave-Assisted Extraction Systems | 39 | ||
2.3.1 Usage of Modified Domestic Microwave Ovens | 40 | ||
2.3.2 Usage of Commercial Microwave Reactors | 41 | ||
2.3.3 Continuous and High-Scale Microwave Applicators for MAE | 43 | ||
2.4 Plants and Components of Interest for Microwave-Assisted Extraction Processes | 43 | ||
2.4.1 Essential Oils from Herbs | 43 | ||
2.4.2 Phenolic Compounds and Antioxidants | 44 | ||
2.4.3 Oils, Lipids and Fatty Acids | 44 | ||
2.4.4 Polysaccharides and Pectin Extraction | 45 | ||
2.5 Microwave-Assisted Extraction Techniques | 45 | ||
2.5.1 Solvent-Free Microwave Extraction | 47 | ||
2.5.2 Microwave-Assisted Extraction | 48 | ||
2.5.3 Microwave Pre-Treatment | 50 | ||
2.6 Extraction Fundamentals | 50 | ||
2.6.1 Heat Generation | 51 | ||
2.6.2 Mass Transfer | 52 | ||
2.6.3 Kinetics Modelling | 54 | ||
2.7 Operating Variables | 55 | ||
2.7.1 Time | 55 | ||
2.7.2 Microwave Power and Energy | 56 | ||
2.7.3 Temperature | 57 | ||
2.7.4 Particle Size | 57 | ||
2.7.5 Solvent | 58 | ||
2.7.6 Pressure | 58 | ||
2.8 Conclusions | 59 | ||
References | 59 | ||
Chapter 3 - Low-Temperature Microwave Pyrolysis and Large Scale Microwave Applications | 64 | ||
3.1 Microwave Technology | 64 | ||
3.1.1 Microwave Technology Applications | 65 | ||
3.1.2 History of Heating Application of Microwave Irradiation | 66 | ||
3.1.3 Microwave Equipment | 67 | ||
3.2 Heating | 68 | ||
3.2.1 General Discussion | 68 | ||
3.2.2 Mechanism of Microwave Heating | 69 | ||
3.3 Microwave Pyrolysis/Torrefaction | 72 | ||
3.3.1 Introduction | 72 | ||
3.3.2 Low-Temperature Pyrolysis of Constituent Biomass Components | 73 | ||
3.3.2.1 Cellulose | 73 | ||
3.3.2.2 Hemi-Cellulose | 78 | ||
3.3.2.3 Lignin | 79 | ||
3.3.3 Microwave Pyrolysis of Lignocellulosic Biomass | 80 | ||
3.3.3.1 Wood | 80 | ||
3.3.3.2 Wheat Straw and Rice Straw | 81 | ||
3.3.3.3 Macro and Micro Algae | 83 | ||
3.3.3.4 Oil Palm | 83 | ||
3.4 Commercial Applications of Microwaves | 84 | ||
3.4.1 Drying Apparatus | 85 | ||
3.4.2 Other Processes | 86 | ||
3.4.3 Microwave-Assisted Biomass Activation | 87 | ||
3.5 Conclusion | 89 | ||
Acknowledgements | 89 | ||
References | 90 | ||
Chapter 4 - Microwave Reactor Concepts: From Resonant Cavities to Traveling Fields | 93 | ||
4.1 Introduction: The Limitations of Thermal Reactor Activation | 93 | ||
4.2 Resonant Microwave Cavities | 95 | ||
4.2.1 Multimode Cavities | 97 | ||
4.2.2 Single Mode Cavities | 100 | ||
4.2.2.1 CEM Discover | 100 | ||
4.2.2.2 TE10n Cavities | 103 | ||
4.3 Advanced Non-Cavity Applicator Types | 110 | ||
4.3.1 Internal Transmission Line | 111 | ||
4.3.2 Traveling Microwave Reactor | 112 | ||
4.3.2.1 Liquid Phase Process Configuration | 115 | ||
4.3.2.2 Gas–Solid Phase Process Configuration | 119 | ||
4.4 Conclusions | 121 | ||
Acknowledgements | 122 | ||
References | 122 | ||
Chapter 5 - Greener Processing Routes for Reactions and Separations Based on Use of Ultrasound and Hydrodynamic Cavitation | 126 | ||
5.1 Introduction | 126 | ||
5.2 Mechanism of Cavitation-Based Process Intensification | 128 | ||
5.3 Reactor Configurations | 130 | ||
5.3.1 Sonochemical Reactors | 130 | ||
5.3.2 Hydrodynamic Cavitation Reactors | 133 | ||
5.4 Guidelines for the Selection of Cavitational Reactor Designs and Operating Parameters | 136 | ||
5.5 Comparison of Two Modes of Cavity Generation | 138 | ||
5.6 Overview of Intensification of Chemical Synthesis | 140 | ||
5.7 Overview of Applications in the Area of Wastewater Treatment | 143 | ||
5.8 Overview of Cavitational Reactors for Intensified Separations | 147 | ||
5.8.1 Crystallization | 147 | ||
5.8.2 Extraction | 150 | ||
5.8.3 Adsorption | 153 | ||
5.8.4 Distillation | 155 | ||
5.9 Summary | 156 | ||
References | 157 | ||
Chapter 6 - Magnetically Assisted Separations in Chemical Industry and Biotechnology: Basic Principles and Applications | 161 | ||
6.1 Introduction | 161 | ||
6.1.1 Magnetic Separations at a Glance | 162 | ||
6.1.2 Topics Analyzed at a Glance | 162 | ||
6.1.2.1 Mechanical Magnetic Separations | 163 | ||
6.1.2.2 Separations Involving Non-Tailored Magnetic Solids | 163 | ||
6.1.2.3 Separations Involving Magnetic Solids with Tailored and Functionalized Surfaces | 163 | ||
6.2 Mechanical Magnetic Separations | 163 | ||
6.2.1 Magnetically-Assisted Fluidization (MAF) | 164 | ||
6.2.1.1 Operating Modes | 165 | ||
6.2.1.2 Magnetic Fields Used | 165 | ||
6.2.1.3 Hydrodynamic Background | 167 | ||
6.2.1.3.1 Solids Flow Through the Reactor: Operating Modes.There are two operating modes with respects the solids flow through the reactor... | 167 | ||
6.2.1.3.2 Fluidization Vessels.In general, fluidization is performed in cylindrical vessels (columns) allowing a homogeneous gas distribut... | 167 | ||
6.2.1.3.3 Bed Regimes Map.Commonly, the original studies are motivated by the need to operate either: at high working velocities, impossib... | 168 | ||
6.2.2 Magnetically-Assisted Particle–Particle Separations by Density | 169 | ||
6.2.2.1 Batch-Solids Separations | 169 | ||
6.2.2.2 Continuous Cross-Flow MSB for Particle–Particle Separations | 170 | ||
6.2.3 Particle Separation from Flow | 171 | ||
6.2.3.1 Magnetic Matrix Filters | 171 | ||
6.2.3.2 MSB-Based Aerosol Filters | 172 | ||
6.2.3.2.1 Aerosols Capture in Magnetization FIRST Mode: Axial Fields.This is the oldest application of MSB filters based on the doctoral t... | 173 | ||
6.2.3.2.2\rAerosols Capture in Magnetization LAST Mode: Axial Fields.The group of Tien58–60 developed the idea for MSB filters in more deta... | 174 | ||
6.2.3.2.3 Aerosols Capture in Magnetization FIRST Mode: Transverse Fields.In axial fields, in order to create an almost homogeneous partic... | 174 | ||
6.2.3.3 Aerosol Filtration by Magnetically Semi-Fluidized Beds | 174 | ||
6.2.3.4 Magnetically-Assisted Cake Filtration | 175 | ||
6.2.4 Magnetically-Assisted Gravity Sedimentation | 176 | ||
6.3 Magnetic Separations Involving Magnetic Solids with Non-Tailored Surfaces | 177 | ||
6.3.1 Magnetic Seeding | 177 | ||
6.3.2 Adsorption: Focusing on Magnetite as Adsorbent | 178 | ||
6.3.2.1 Adsorption of Hazardous Species: Examples | 180 | ||
6.3.2.1.1\rRadioactive contaminants | 180 | ||
Cesium. Milonjic and Ruvarac86 reported the adsorption of cesium (Cs), cobalt (Co2+ as less than 5 wt%) and cerium (Ce+) by magn... | 180 | ||
Cobalt. Cotten and Navratil88 observed the adsorption of cobalt in a static field of a neodymium–iron–boron permanent magnet irr... | 180 | ||
Uranium. Uranium and associated radionuclides, in particular radium and radon, pose significant health risks to humans due to bo... | 180 | ||
Europium. Being a typical member of the lanthanide series, europium (Eu), usually assumes the oxidation state of +3, but due to ... | 181 | ||
6.3.2.1.2\rHeavy Metals | 181 | ||
Chromium. Namdeo and Bajpai93 investigated deposition of a hexavalent chromium Cr(vi) onto synthetic magnetite nanoparticles fro... | 181 | ||
Selenium. Selenium (a metalloid found in group VI of the periodic table below sulfur) is a natural trace element found in bedroc... | 181 | ||
Arsenic. Arsenic is a heavy metal occurring in the environment in different oxidation states and form various species, e.g., As ... | 181 | ||
6.3.2.1.3\rPost-Adsorption Separations.The next step, after the adsorption, is the removal of the magnetic adsorbents from the solution. Co... | 182 | ||
6.3.2.1.4\rCoarse Particles vs. Nanoparticles As Adsorbents.The main problem in the sorption by nanoparticles is the impossibility to organ... | 183 | ||
6.3.2.1.5\rMagnetically-Assisted Fluidization: An Alternative in the Adsorption Separations.The sorption with magnetic adsorbents should co... | 183 | ||
6.3.3 Metal Recovery by Cementation | 183 | ||
6.3.3.1 Copper Cementation by Iron | 184 | ||
6.3.3.2 Silver Cementation by Iron | 185 | ||
6.4 Magnetic Separations Involving Tailored and Functionalized Magnetic Solids | 185 | ||
6.4.1 Why Magnetic Beads | 186 | ||
6.4.2 Magnetic Bead Manufacturing | 186 | ||
6.4.3 Examples of Bio-Separation Processes | 188 | ||
6.4.3.1 Affinity Chromatography | 188 | ||
6.4.3.2 MSB-Based Cell Affinity Separations | 189 | ||
6.4.3.3 Magnetic solid-phase extraction | 189 | ||
6.4.4 Magnetic Membrane Separations | 189 | ||
6.5 Final Comments | 190 | ||
References | 191 | ||
Chapter 7 - Prospects of Magnetic Nanoparticles for Magnetic Field-Assisted Mixing of Fluids with Relevance to Chemical Engineering | 198 | ||
7.1 Introduction | 198 | ||
7.2 Mixing Based on Ferrohydrodynamics (FHD) | 199 | ||
7.2.1 FHD Transport Equations | 201 | ||
7.2.2 Mixing with Static Magnetic Fields (SMF) | 202 | ||
7.2.3 Mixing with Oscillating Magnetic Fields (OMF) | 207 | ||
7.2.4 Mixing with Rotating Magnetic Fields (RMF) | 211 | ||
7.2.4.1 Comparison of RMF with OMF and SMF in Lateral Nanomixing of Ferrofluid Capillary Flows | 214 | ||
7.3 Lorentz Force-Driven Mixing | 217 | ||
7.4 Conclusion | 223 | ||
Nomenclature | 224 | ||
References | 225 | ||
Chapter 8 - Photocatalysis: Past Achievements and Future Trends | 227 | ||
8.1 Introduction | 227 | ||
8.2 Catalyst Development | 230 | ||
8.3 Photocatalytic Reactors | 246 | ||
8.3.1 Suspended Systems | 246 | ||
8.3.2 Immobilised Systems | 247 | ||
8.3.2.1 Flat Plate | 247 | ||
8.3.2.2 Honeycomb Monolith Photocatalytic Reactor | 248 | ||
8.3.2.3 Optical Fiber Photocatalytic Reactors | 249 | ||
8.3.2.4 Annular Reactors | 252 | ||
8.3.2.5 Packed-Bed Photocatalytic Reactors | 252 | ||
8.3.2.6 Microreactors | 253 | ||
8.3.3 Light Sources | 254 | ||
8.3.3.1 Solar-Based Photocatalytic Reactors | 255 | ||
8.3.3.2 Artificial Light Sources | 258 | ||
8.4 Conclusions | 259 | ||
References | 260 | ||
Chapter 9 - Photocatalytic Reactors in Environmental Applications | 270 | ||
9.1 Introduction | 270 | ||
9.2 Wastewater Treatment | 272 | ||
9.2.1 Slurry Reactors | 273 | ||
9.2.1.1 Multi-Lamp Reactor (MLR) | 276 | ||
9.2.1.2 Rotating Annular Reactor (RAR) | 278 | ||
9.2.1.3 Fountain Reactor (FR) | 279 | ||
9.2.1.4 Photocatalytic Membrane Reactor (PMR) | 280 | ||
9.2.2 Immobilized Catalyst Reactors (ICR) | 282 | ||
9.2.2.1 Parallel Plate Reactor (PPR) | 284 | ||
9.2.2.2 Microreactor | 285 | ||
9.2.2.3 Optical Fibre Reactor (OFR) | 286 | ||
9.2.2.4 Foam Reactor (FR) | 286 | ||
9.2.2.5 Spinning Disc Reactor (SDR) | 288 | ||
9.3 Benchmarking Wastewater Treatment Reactors | 290 | ||
9.4 Conclusions | 292 | ||
References | 293 | ||
Chapter 10 - Plasma-Assisted Nitrogen Fixation Reactions | 296 | ||
10.1 Introduction | 296 | ||
10.1.1 Background – Nitrogen Fixation | 296 | ||
10.1.2 Timeline of N-Fixation Process Development | 297 | ||
10.1.3 Introduction to Plasmas | 302 | ||
10.2 Plasma-Assisted Nitrogen Fixation | 303 | ||
10.2.1 Plasma Nitric Oxide Synthesis | 303 | ||
10.2.1.1 Industrial-Scale Plasma Nitric Oxide Synthesis Processes | 303 | ||
10.2.1.2 Laboratory Studies on Plasma Nitric Oxide Synthesis | 306 | ||
10.2.1.2.1\rPlasma Reactor Configurations.Various plasma types have been investigated to perform the nitric oxide synthesis. Table 10.2 summ... | 306 | ||
10.2.1.2.2\rPlasma Catalysis for Nitric Oxide Synthesis.The combination of catalyst and the plasma reactor has not been investigated thoroug... | 310 | ||
10.2.1.3 Mechanism of Plasma Nitric Oxide Synthesis | 313 | ||
10.2.1.4 Energy Efficiency of Plasma Nitric Oxide Synthesis | 316 | ||
10.2.1.5 Applications Beyond Nitric Acid | 318 | ||
10.2.1.5.1\rDirect Agricultural Fertilizer.The NO produced with lower concentrations in plasma processes can be used directly as a fertilize... | 318 | ||
10.2.1.5.2\rMedical Use.Inhaled NO has been extensively used in clinical treatment of pulmonary hypertension, high altitude pulmonary edema,... | 318 | ||
10.2.1.5.3\rIn Liquid.In a typical plasma nitric oxide process, NO is first oxidized to NO2, then NO2 is absorbed in water to form HNO3. Ins... | 319 | ||
10.2.1.5.4\rLightning.Fixation of nitrogen by lightning is of great importance to understand the environmental chemistry and evolution of th... | 319 | ||
10.2.2 Plasma Ammonia Synthesis | 319 | ||
10.2.2.1 Laboratory-Scale Efforts to Improve Plasma NH3 Synthesis Process | 319 | ||
10.2.2.1.1\rPlasma Reactor Configurations.Non-equilibrium plasmas which operate at ambient temperature are widely investigated as a promisin... | 320 | ||
10.2.2.1.2\rPlasma Catalysis for Ammonia Synthesis.As can be learnt from the above section, the surface reaction of N and H is an important ... | 327 | ||
10.2.2.2 Energy Requirement for Plasma Ammonia Synthesis | 329 | ||
10.2.2.3 Applications of Plasma NH3 Synthesis | 329 | ||
10.2.3 Hydrogen Cyanide Synthesis | 329 | ||
10.2.3.1 Conventional Hydrogen Cyanide Processes | 329 | ||
10.2.3.2 Plasma Hydrogen Cyanide Process | 330 | ||
10.2.3.3 Kinetics and Mechanism of Plasma HCN Synthesis | 330 | ||
10.3 Conclusions and Outlook | 332 | ||
Acknowledgements | 333 | ||
References | 333 | ||
Chapter 11 - Higee Technologies and Their Applications to Green Intensified Processing | 339 | ||
11.1 Introduction | 339 | ||
11.2 Spinning Disc Reactor (SDR) | 340 | ||
11.2.1 Design and Operating Principles | 340 | ||
11.2.2 Green Processing Applications of SDR | 343 | ||
11.2.2.1 Polymerisations | 343 | ||
11.2.2.2 Reactive Precipitations | 346 | ||
11.2.2.3 Catalytic/Enzymatic Transformations | 347 | ||
11.2.3 Rotor–stator SDR | 349 | ||
11.3 Rotating Packed Bed (RPB) | 349 | ||
11.3.1 Design and Operating Principles | 349 | ||
11.3.2 Green Processing Applications of RPB | 351 | ||
11.3.2.1 Absorption Processes | 352 | ||
11.3.2.1.1\rCarbon Capture Applications.Although distillation was one of the earliest applications of the RPB,40 there has been much renewed... | 352 | ||
11.3.2.1.2\rSO2 and NOx Absorption.Although the focus lately has primarily been on CO2 sequestration in order to meet environmental legislat... | 352 | ||
11.3.2.2 Reactive Precipitations | 353 | ||
11.3.3 Novel Variations of RPB designs | 353 | ||
11.4 Concluding Remarks | 354 | ||
References | 355 | ||
Chapter 12 - High-Gravity Operation in Vortex Chambers for the Generation of High-Efficiency Fluidized Beds | 360 | ||
12.1 Introduction on Fluidization in a High-G Field | 360 | ||
12.2 Rotating Fluidized Beds in a (Static) Vortex Chamber | 362 | ||
12.3 Hydrodynamic Characteristics | 363 | ||
12.3.1 Fluidization in the Tangential and Radial Direction | 363 | ||
12.3.2 Free Vortex Versus Solid Body Type Rotation and Flexibility in the Solids Loading | 364 | ||
12.3.3 Flexibility in the Gas Flow Rate | 366 | ||
12.3.4 Large-Scale Non-Uniformities and Bed Stability | 368 | ||
12.3.5 Meso-Scale Non-Uniformities | 369 | ||
12.3.6 Further Remarks on the Gas and Solids Phase Flow Pattern | 371 | ||
12.4 Design Aspects | 375 | ||
12.4.1 Design Objectives | 375 | ||
12.4.2 Gas Inlets | 375 | ||
12.4.3 Gas Outlet/Chimney | 381 | ||
12.4.4 Solids Inlet | 384 | ||
12.4.5 Solids Outlet | 387 | ||
12.4.6 Other Design Aspects | 388 | ||
12.5 Intensification of Interfacial Mass and Heat Transfer | 388 | ||
12.6 Intensification of Heterogeneous Catalytic Reactions | 394 | ||
12.7 Extensions of the Concept and Multi-Zone Operation | 396 | ||
12.8 Conclusions and Outlook | 400 | ||
References | 402 | ||
Subject Index | 405 |