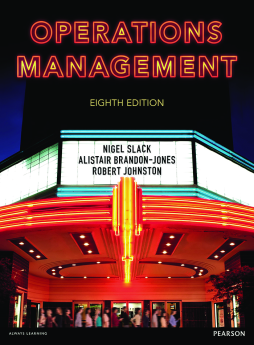
Additional Information
Book Details
Abstract
Operations management is important, exciting, challenging … and everywhere you look!
-
Important, because it enables organizations to provide services and products that we all need
-
Exciting, because it is central to constant changes in customer preference, networks of supply and demand, and developments in technology
-
Challenging, because solutions must be must be financially sound, resource-efficient, as well as environmentally and socially responsible
-
And everywhere, because in our daily lives, whether at work or at home, we all experience and manage processes and operations.
New features:
-
There are now more than 110 of the popular ‘Operations in Practice’ examples throughout the book, over 40% of which are new.
-
The importance of sustainability and Corporate Social Responsibility (CSR) has been emphasized further, and included throughout the book.
-
We have even further strengthened the emphasis on the idea that ‘operations management’ is relevant to every type of business and all functional areas of the organization.
-
Many new ideas in operations management have been incorporated, including the ‘three level’ approach to performance, the relationship between innovation, creativity and design, crowdsourcing, ideas management, business ecosystems, triadic relationships, office layout, telecommuting and organisational ‘ambidexterity’. However, we have retained the emphasis on the foundations of the subject.
-
Six of the 19 cases at the end of the chapter are new (but the old ones are still available on the web site), and provide an up-to-date selection of operations issues.
Operations Management focuses on the sustainable and socially responsible imperatives of operations management, using over 120 cases and illustrations of real-life operations around the world, including Apple, Médecins Sans Frontières, Amazon, Ecover, Dyson, Disneyland Paris, Google, The North Face, and many more.
This is 24-carat excellence'
Par Åhlström, Torsten and Ragnar Söderberg Chair of Business Administration, Stockholm School of Economics
'Operations Management is engaging and accessible, but it never dumbs-down. The book is comprehensive, but not overwhelming. Students hold on to this one; it’s a ‘keeper’.'
Michael Shulver, Birmingham Business School
'This continues to be the definitive operations Management text … written by the masters of the field!'
Dr Ross Ritchie, Lecturer in Operations Management, Loughborough University
'An essential text packed full of up-to-date examples that really bring the subject to life'
Claire Moxham, University of Liverpool Management School
'An excellent book for those studying operations management. This book provides great illustrations to seamlessly link theory with practice'
Frank Wiengarten, ESADE Business School
Operations Management by Nigel Slack and Alistair Brandon-Jones is quite simply the best text on operations management. Comprehensive, engaging and insightful, I cannot recommend this book highly enough'
Professor Andy Neely, Head, Institute for Manufacturing, Cambridge University
Carrie Queenan, University of South Carolina
Peter Race, Henley Business School, University of Reading
Table of Contents
Section Title | Page | Action | Price |
---|---|---|---|
Cover | Cover | ||
Title Page | iii | ||
Copyright Page | iv | ||
Brief contents | v | ||
Contents | vii | ||
Guide to ‘operations in practice’, examples, short cases and case studies | xii | ||
Preface | xvi | ||
To the Instructor. . . | xviii | ||
To the Student. . . | xix | ||
Ten steps to getting a better grade in operations management | xx | ||
About the authors | xxi | ||
Acknowledgements | xxii | ||
Publisher’s acknowledgements | xxiv | ||
Part One DIRECTING THE OPERATION | 3 | ||
Chapter 1: Operations management | 4 | ||
Introduction | 4 | ||
What is operations management? | 5 | ||
Why is operations management important in all types of organization? | 8 | ||
What is the input–transformation–output process? | 13 | ||
What is the process hierarchy? | 19 | ||
How do operations and processes differ? | 22 | ||
What do operations managers do? | 27 | ||
Summary answers to key questions | 31 | ||
Case study : Design house partnerships at Concept Design Services | 33 | ||
Problems and applications | 36 | ||
Selected further reading | 36 | ||
Chapter 2: Operations performance | 38 | ||
Introduction | 38 | ||
Why is operations performance vital in any organization? | 39 | ||
How is operations performance judged at a societal level? | 41 | ||
How is operations performance judged at a strategic level? | 46 | ||
How is operations performance judged at an operational level? | 48 | ||
How can operations performance be measured? | 63 | ||
How do performance objectives trade off against each other? | 66 | ||
Summary answers to key questions | 68 | ||
Case study : Operations objectives at the Penang Mutiara | 70 | ||
Problems and applications | 72 | ||
Selected further reading | 73 | ||
Chapter 3: Operations strategy | 74 | ||
Introduction | 74 | ||
What is strategy and what is operations strategy? | 76 | ||
What is the difference between a ‘top-down’ and ‘bottom-up’ view of operations strategy? | 80 | ||
What is the difference between a ‘market requirements’ and an ‘operations resources’ view of operations strategy? | 84 | ||
How can operations strategy form the basis for operations improvement? | 92 | ||
How can an operations strategy be put together? The process of operations strategy | 98 | ||
Summary answers to key questions | 102 | ||
Case study : McDonald's: half a century of growth | 104 | ||
Problems and applications | 107 | ||
Selected further reading | 108 | ||
Chapter 4: Product and service innovation | 109 | ||
Introduction | 109 | ||
What is product and service innovation? | 110 | ||
What is the strategic role of product and service innovation? | 114 | ||
What are the stages of product and service innovation? | 119 | ||
What are the benefits of interactive product and service innovation? | 130 | ||
Summary answers to key questions | 134 | ||
Case study: Developing ‘Savory Rosti-crisps’ at Dreddo Dan’s | 136 | ||
Problems and applications | 138 | ||
Selected further reading | 139 | ||
Chapter 5: The structure and scope of operations | 140 | ||
Introduction | 140 | ||
What do we mean by the ‘structure’ and ‘scope’ of operations’ supply networks? | 141 | ||
What configuration should a supply network have? | 145 | ||
How much capacity should operations plan to have? | 149 | ||
Where should operations be located? | 154 | ||
How vertically integrated should an operation’s network be? | 156 | ||
How do operations decide what to do in-house and what to outsource? | 161 | ||
Summary answers to key questions | 164 | ||
Case study: Aarens Electronic | 166 | ||
Problems and applications | 168 | ||
Selected further reading | 169 | ||
Supplement to Chapter 5: Forecasting | 170 | ||
Introduction | 170 | ||
Forecasting – knowing the options | 170 | ||
In essence forecasting is simple | 171 | ||
Approaches to forecasting | 172 | ||
Selected further reading | 178 | ||
Part Two DESIGNING THE OPERATION | 181 | ||
Chapter 6: Process design | 182 | ||
Introduction | 182 | ||
What is process design? | 183 | ||
What should be the objectives of process design? | 185 | ||
How do volume and variety affect process design? | 189 | ||
How are processes designed in detail? | 195 | ||
Summary answers to key questions | 211 | ||
Case study: The Action Response Applications Processing Unit (ARAPU) | 212 | ||
Problems and applications | 214 | ||
Selected further reading | 214 | ||
Chapter 7: Layout and flow | 216 | ||
Introduction | 216 | ||
What is layout and how can it influence performance? | 217 | ||
What are the basic layout types used in operations? | 220 | ||
How does the appearance of an operation affect its performance? | 231 | ||
How should each basic layout type be designed in detail? | 234 | ||
Summary answers to key questions | 240 | ||
Case study: The event hub | 241 | ||
Problems and applications | 244 | ||
Selected further reading | 244 | ||
Chapter 8: Process technology | 246 | ||
Introduction | 246 | ||
What is process technology? | 247 | ||
What do operations managers need to know about process technology? | 251 | ||
How are process technologies evaluated? | 258 | ||
How are process technologies implemented? | 264 | ||
Summary answers to key questions | 271 | ||
Case study: Rochem Ltd | 272 | ||
Problems and applications | 274 | ||
Selected further reading | 274 | ||
Chapter 9: People in operations | 276 | ||
Introduction | 276 | ||
Why are people so important in operations management? | 277 | ||
How do operations managers contribute to human resource strategy? | 279 | ||
How can the operations function be organized? | 281 | ||
How do we go about designing jobs? | 286 | ||
How are work times allocated? | 300 | ||
Summary answers to key questions | 301 | ||
Case study: Grace faces (three) problems | 302 | ||
Problems and applications | 304 | ||
Selected further reading | 305 | ||
Supplement to Chapter 9: Work study | 306 | ||
Introduction | 306 | ||
Method study in job design | 306 | ||
Work measurement in job design | 309 | ||
Part Three DELIVER | 315 | ||
Chapter 10: Planning and control | 317 | ||
Introduction | 317 | ||
What is planning and control? | 318 | ||
What is the difference between planning and control? | 319 | ||
How do supply and demand affect planning and control? | 321 | ||
What are the activities of planning and control? | 327 | ||
Summary answers to key questions | 345 | ||
Case study: subText Studios Singapore | 346 | ||
Problems and applications | 348 | ||
Selected further reading | 349 | ||
Chapter 11: Capacity management | 350 | ||
Introduction | 350 | ||
What is capacity management? | 351 | ||
How are demand and capacity measured? | 354 | ||
How should the operation’s base capacity be set? | 364 | ||
What are the ways of coping with mismatches between demand and capacity? | 366 | ||
How can operations understand the consequences of their capacity decisions? | 373 | ||
Summary answers to key questions | 382 | ||
Case study: Blackberry Hill Farm | 384 | ||
Problems and applications | 388 | ||
Selected further reading | 389 | ||
Supplement to Chapter 11: Analytical queuing models | 391 | ||
Introduction | 391 | ||
Notation | 391 | ||
Variability | 391 | ||
Incorporating Little’s law | 393 | ||
Types of queuing system | 393 | ||
Chapter 12: Supply chain management | 398 | ||
Introduction | 398 | ||
What is supply chain management? | 399 | ||
How should supply chains compete? | 402 | ||
How should relationships in supply chains be managed? | 407 | ||
How is the supply side managed? | 412 | ||
How is the demand side managed? | 419 | ||
What are the dynamics of supply chains? | 423 | ||
Summary answers to key questions | 426 | ||
Case study: Supplying fast fashion | 428 | ||
Problems and applications | 430 | ||
Selected further reading | 431 | ||
Chapter 13: Inventory management | 432 | ||
Introduction | 432 | ||
What is inventory? | 434 | ||
Why should there be any inventory? | 437 | ||
How much to order? The volume decision | 442 | ||
When to place an order? The timing decision | 452 | ||
How can inventory be controlled? | 458 | ||
Summary answers to key questions | 463 | ||
Case study: supplies4medics.com | 465 | ||
Problems and applications | 466 | ||
Selected further reading | 467 | ||
Chapter 14: Planning and control systems | 468 | ||
Introduction | 468 | ||
What are planning and control systems? | 469 | ||
What is enterprise resource planning and how did it develop into the most common planning and control system? | 475 | ||
How should planning and control systems be implemented? | 483 | ||
Summary answers to key questions | 486 | ||
Case study: Psycho Sports Ltd | 487 | ||
Problems and applications | 489 | ||
Selected further reading | 490 | ||
Supplement to Chapter 14: Materials requirements planning (MRP) | 491 | ||
Introduction | 491 | ||
Master production schedule | 491 | ||
The bill of materials (BOM) | 492 | ||
Inventory records | 494 | ||
The MRP netting process | 494 | ||
MRP capacity checks | 497 | ||
Summary | 497 | ||
Chapter 15: Lean operations | 498 | ||
Introduction | 498 | ||
What is lean? | 499 | ||
How does lean eliminate waste? | 506 | ||
How does lean apply throughout the supply network? | 519 | ||
How does lean compare with other approaches? | 521 | ||
Summary answers to key questions | 524 | ||
Case study: Saint Bridget’s Hospital | 525 | ||
Problems and applications | 527 | ||
Selected further reading | 528 | ||
Part Four DEVELOPMENT | 531 | ||
Chapter 16: Operations improvement | 532 | ||
Introduction | 532 | ||
Why is improvement so important in operations management? | 533 | ||
What are the key elements of operations improvement? | 540 | ||
What are the broad approaches to improvement? | 545 | ||
What techniques can be used for improvement? | 554 | ||
How can the improvement process be managed? | 559 | ||
Summary answers to key questions | 566 | ||
Case study: Reinventing Singapore’s libraries | 568 | ||
Problems and applications | 569 | ||
Selected further reading | 570 | ||
Chapter 17: Quality management | 572 | ||
Introduction | 572 | ||
What is quality and why is it so important? | 573 | ||
What steps lead towards conformance to specification? | 580 | ||
What is total quality management (TQM)? | 587 | ||
Summary answers to key questions | 597 | ||
Case study: Turnaround at the Preston plant | 599 | ||
Problems and applications | 601 | ||
Selected further reading | 602 | ||
Supplement to Chapter 17: Statistical process control | 603 | ||
Introduction | 603 | ||
Control charts | 603 | ||
Variation in process quality | 604 | ||
Control charts for attributes | 608 | ||
Control chart for variables | 610 | ||
Summary of supplement | 615 | ||
Selected further reading | 615 | ||
Chapter 18: Managing risk and recovery | 616 | ||
Introduction | 616 | ||
What is risk management? | 617 | ||
How can operations assess the potential causes and consequences of failure? | 619 | ||
How can failures be prevented? | 632 | ||
How can operations mitigate the effects of failure? | 637 | ||
How can operations recover from the effects of failure? | 639 | ||
Summary answers to key questions | 642 | ||
Case study: Slagelse Industrial Services (SIS) | 643 | ||
Problems and applications | 645 | ||
Selected further reading | 645 | ||
Chapter 19: Project management | 646 | ||
Introduction | 646 | ||
What is project management? | 647 | ||
How are projects planned? | 653 | ||
How are projects controlled? | 669 | ||
Summary answers to key questions | 674 | ||
Case study: United Photonics Malaysia Sdn Bhd | 675 | ||
Problems and applications | 679 | ||
Selected further reading | 680 | ||
Notes on chapters | 681 | ||
Useful websites | 689 | ||
Glossary | 691 | ||
Index | 704 |