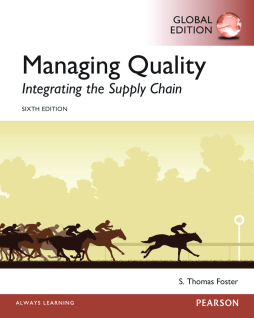
Additional Information
Book Details
Abstract
For courses in Quality Management.
Navigating Quality Management With A Unifying Framework
Foster’s Managing Quality: Integrating the Supply Chain, Sixth Edition offers students a thorough introduction to quality management by presenting a supply chain theme as the unifying framework for quality improvement. The supply chain thread enhances the integration of systems with customers, suppliers, technology, and people. The colorful, stunning text appeals to visual learners and grabs students’ attention at the outset.
The Sixth Edition elicits a theme of “currency” while offering updated vignettes and references to remain state-of-the-art. The new edition is selectively edited and enhanced with new content that maintains its scope and withstands pivotal points in each section. Managing Quality keeps a competitive advantage by sustaining and building on cutting edge, relevant topics in quality management.
Table of Contents
Section Title | Page | Action | Price |
---|---|---|---|
Cover | Cover | ||
Title Page | 3 | ||
Copyright Page | 4 | ||
Brief Contents | 6 | ||
Contents | 7 | ||
Preface | 20 | ||
Part 1 Understanding Quality Concepts | 25 | ||
Chapter 1 Differing Perspectives on Quality | 26 | ||
A Closer look At Quality 1-1: Buying Clothing in Asia | 27 | ||
What is Quality? | 27 | ||
Product Quality Dimensions | 27 | ||
service Quality Dimensions | 29 | ||
Why Does it Matter that Different Definitions of Quality Exist? | 30 | ||
Differing Functional Perspectives on Quality | 30 | ||
A Supply Chain Perspective | 31 | ||
An Engineering Perspective | 32 | ||
An Operations Perspective | 34 | ||
A Strategic Management Perspective | 34 | ||
A Marketing Perspective | 36 | ||
Quality Highlight 1-1: Quality Strategy at Hyundai | 36 | ||
A Financial Perspective | 38 | ||
The Human Resources Perspective | 39 | ||
Is Quality Management Its Own Functional Discipline? | 40 | ||
The Three Spheres of Quality | 40 | ||
Quality Highlight 1-2: Federal Express Corporation | 41 | ||
Other Perspectives on Quality | 42 | ||
The Value-Added Perspective on Quality | 42 | ||
Cultural Perspectives on Quality | 43 | ||
Arriving at a Common Understanding of Quality Using a Contingency Perspective of Quality | 43 | ||
Summary | 43 | ||
Key Terms | 44 | ||
Discussion Questions | 44 | ||
Case 1-1: FedEx: Managing Quality Day and Night | 45 | ||
Case 1-2: Graniterock Company: Achieving Quality through Employees | 46 | ||
Chapter 2 Quality Theory | 48 | ||
What Is Theory? | 48 | ||
Is There a Theory of Quality Management? | 50 | ||
A Closer look At Quality 2-1: Quality and Management Fads | 50 | ||
History of Quality Management | 51 | ||
Leading Contributors to Quality Theory: W. Edwards Deming | 51 | ||
Deming’s 14 Points for Management | 53 | ||
Leading Contributors to Quality Theory: Joseph M. Juran | 56 | ||
The Juran Trilogy | 56 | ||
Control versus Breakthrough | 57 | ||
Project-by-Project Improvement | 57 | ||
A Closer look At Quality 2-2: Juran on the Past Century of Quality | 58 | ||
Leading Contributors to Quality Theory: Kaoru Ishikawa | 58 | ||
The Basic Tools of Quality | 58 | ||
Leading Contributors to Quality Theory: Armand Feigenbaum | 59 | ||
The 19 Steps of TQC | 59 | ||
Leading Contributors to Quality Theory: Philip Crosby | 60 | ||
Leading Contributors to Quality Theory: Genichi Taguchi | 61 | ||
Definition of Quality | 61 | ||
Quality Loss Function | 61 | ||
Robust Design | 61 | ||
Leading Contributors to Quality Theory: The Rest of the Pack | 62 | ||
Robert C. Camp | 62 | ||
Stephen R. Covey’s “8” Habits | 62 | ||
Michael Hammer and James Champy | 63 | ||
A Closer look At Quality 2-3: Selling Quality Fads | 64 | ||
Viewing Quality Theory from a Contingency Perspective | 64 | ||
Resolving the Differences in Quality Approaches: An Integrative View | 65 | ||
Leadership | 65 | ||
Employee Improvement | 65 | ||
Quality Assurance | 65 | ||
Customer Focus | 66 | ||
Quality Philosophy | 66 | ||
Information Analysis | 67 | ||
Strategic Planning | 67 | ||
Environment or Infrastructure | 67 | ||
Team Approach | 67 | ||
Focus of the Quality Department | 67 | ||
Breakthrough | 67 | ||
Theoretical Framework for Quality Management | 67 | ||
Summary | 68 | ||
Key Terms | 69 | ||
Discussion Questions | 69 | ||
Case 2-1: Rheaco, Inc.: Making a Quality Turnabout by Asking for\rAdvice | 70 | ||
Case 2-2: Has Disney Developed a Theory of Quality Guest Services\rManagement? | 71 | ||
Chapter 3 Global Supply Chain Quality and International Quality Standards | 73 | ||
Managing Quality for the Multinational Firm (MNF) | 74 | ||
Quality Highlight 3-1: Global Supply Chain Quality at Trek | 77 | ||
Quality Improvement: The American Way | 78 | ||
The Baldrige Performance Excellence Program | 78 | ||
A Closer look At Quality 3-1: Who Was Malcolm Baldrige? | 84 | ||
The Baldrige Process | 84 | ||
Baldrige Scoring | 86 | ||
Being a Baldrige Examiner | 86 | ||
Quality Highlight 3-2: Honeywell Federal Manufacturing & Technologies | 88 | ||
State Awards | 88 | ||
Quality Improvement: The Japanese Way | 89 | ||
Deming Prize | 89 | ||
Other Japanese Contributions to Quality Thought | 89 | ||
Lean Production | 90 | ||
Quality Highlight 3-3: The Humbling of Toyota | 91 | ||
Japanese Total Quality Control (TQC) | 91 | ||
Quality Improvement: The European Way | 93 | ||
European Quality Award | 93 | ||
ISO 9000:2015 | 94 | ||
Quality Management Principles Underlying ISO 9000:2015 | 95 | ||
Selecting a Registrar | 95 | ||
The ISO 9000:2015 Process | 96 | ||
ISO 14000 | 97 | ||
Quality Improvement: The Chinese Way | 98 | ||
Does Chinese Quality Management Exist? | 99 | ||
A Closer look At Quality 3-2: Outsourcing Woes | 100 | ||
Are Quality Approaches Influenced by Culture? | 100 | ||
Summary | 101 | ||
Key Terms | 101 | ||
Discussion Questions | 101 | ||
Case 3-1: Denver International Airport Becomes ISO 14001 Certified | 102 | ||
Case 3-2: Wainwright Industries: An Entirely New Philosophy of Business\rBased on Customer Satisfaction and Quality | 103 | ||
Part 2 Designing and Assuring Quality | 105 | ||
Chapter 4 Strategic Quality Planning | 106 | ||
Strategy Content | 106 | ||
The Importance of Time in Quality Improvement | 107 | ||
A Closer look At Quality 4-1: Bad Measurement Systems Result in Poor\rOutcomes | 108 | ||
Leadership for Quality | 109 | ||
Leadership Dimensions | 109 | ||
Quality Highlight 4-1: Solectron Corporation | 111 | ||
Quality and Ethics | 112 | ||
Quality as a Strategy | 112 | ||
Costs of Quality | 112 | ||
PAF Paradigm | 113 | ||
Accounting for Quality-Related Costs | 114 | ||
Lundvall-Juran Quality Cost Model | 115 | ||
Differentiation through Quality | 116 | ||
Focus through Quality | 116 | ||
Order Winners | 117 | ||
Quality as a Core Competency | 118 | ||
Quality Strategy Process | 118 | ||
Forced-Choice Model | 118 | ||
Deploying Quality (Hoshin Kanri) | 119 | ||
A Closer look At Quality 4-2: A Mature Strategic Planning Process | 119 | ||
Does Quality Lead to Better Business Results? | 120 | ||
Quality and Price | 121 | ||
Quality and Cost | 122 | ||
Quality and Productivity | 122 | ||
Quality and Profitability | 122 | ||
Quality and Sustainability | 123 | ||
Supply Chain Strategy | 123 | ||
Summary | 125 | ||
Key Terms | 125 | ||
Discussion Questions | 125 | ||
Problems | 126 | ||
Case 4-1: Mallinckrodt Pharmaceuticals: Realizing Multiple Benefits through Improved Quality | 127 | ||
Case 4-2: MidwayUSA | 128 | ||
Chapter 5 The Voice of the Customer | 130 | ||
A Closer look At Quality 5-1: Online Review of Merchandise | 131 | ||
Customer-Driven Quality | 131 | ||
The Pitfalls of Reactive Customer-Driven Quality | 131 | ||
Customer-Relationship Management | 132 | ||
Complaint Resolution | 133 | ||
Feedback | 134 | ||
Guarantees | 134 | ||
Corrective Action | 135 | ||
The “Gaps” Approach to Service Design | 135 | ||
Segmenting Customers and Markets | 137 | ||
Strategic Supply Chain Alliances between Customers and Suppliers | 137 | ||
Process-Chain-Network (PCN) Tool for Service Design | 139 | ||
The Role of the Customer in the Supply Chain | 140 | ||
Communicating Downstream | 141 | ||
Actively Solicited Customer-Feedback Approaches | 142 | ||
Telephone Contact | 142 | ||
Focus Groups | 142 | ||
Customer Service Surveys | 142 | ||
A Closer look At Quality 5-2: Misusing Surveys | 143 | ||
Passively Solicited Customer-Feedback Approaches | 146 | ||
Customer Research Cards | 146 | ||
Customer Response Lines and Web Sites | 146 | ||
Managing Customer Retention and Loyalty | 147 | ||
Customer-Relationship Management Systems | 148 | ||
A Word on Excellent Design | 148 | ||
Summary | 150 | ||
Key Terms | 150 | ||
Discussion Questions | 150 | ||
Problems | 151 | ||
Case 5-1: Irish Transport Provider: Continuous Quality Improvement through a Commitment to External and Internal Customers | 151 | ||
Case 5-2: India-based Life Insurer Improves Customer Retention through\rSix Sigma and Quality Tools | 152 | ||
Chapter 6 The Voice of the Market | 154 | ||
Gaining Insights through Benchmarking | 154 | ||
Process Benchmarking | 156 | ||
Financial Benchmarking | 156 | ||
Performance Benchmarking | 156 | ||
Product Benchmarking | 156 | ||
Strategic Benchmarking | 157 | ||
Quality Highlight 6-1: Pal’s Sudden Service | 157 | ||
Functional Benchmarking | 158 | ||
Purposes of Benchmarking | 158 | ||
Difficulties in Monitoring and Measuring Performance | 159 | ||
Commonly Benchmarked Performance Measures | 161 | ||
Why Collect All These Measures? | 163 | ||
Key Business Factors | 163 | ||
Business Process Benchmarking | 163 | ||
Robert Camp’s Business Process Benchmarking Process | 165 | ||
Leading and Managing the Benchmarking Effort | 166 | ||
Training | 166 | ||
A Closer look At Quality 6-1: Benchmarking at PwC | 166 | ||
A Closer look At Quality 6-2: The Legal Environment of Benchmarking | 167 | ||
Baselining and Process Improvement | 168 | ||
Problems with Benchmarking | 168 | ||
Summary | 169 | ||
Key Terms | 169 | ||
Discussion Questions | 169 | ||
Problems | 170 | ||
Case 6-1: Amgen Corporation: Using Benchmarking as a Means of Coping\rwith Rapid Growth | 173 | ||
Case 6-2: AT&T Teleholdings: Making Benchmarking a Part of the Process\rImprovement Tool Kit | 174 | ||
Chapter 7 Quality and Innovation in Product and Process Design | 176 | ||
Designing Products for Quality | 176 | ||
The Design Process | 177 | ||
Quality Highlight 7-1: Apple’s Watch: A Philosophy of Design | 179 | ||
Quality Function Deployment (QFD) | 180 | ||
Technology in Design | 185 | ||
Other Design Methodologies | 188 | ||
Organizing the Design Team | 188 | ||
The Product Life Cycle | 189 | ||
A Closer look At Quality 7-1: Ski Design | 189 | ||
Product Families and the Product Life Cycle | 190 | ||
Complementary Products | 190 | ||
Designing Products That Work | 190 | ||
A Closer look At Quality 7-2: It Takes a Scientist to Design a Winter Coat | 191 | ||
Design for Manufacture Method | 192 | ||
Design for Maintainability | 193 | ||
Designing for Reliability | 194 | ||
Quality Highlight 7-2: Designing Reliable Luxury at Vuitton | 194 | ||
Reliability Analysis Tools | 195 | ||
Failure Modes and Effects Analysis | 195 | ||
How FMEA Works | 196 | ||
Fault-Tree Analysis | 197 | ||
Failure Modes, Effects, and Criticality Analysis | 197 | ||
Product Traceability and Recall Procedures | 198 | ||
Environmental Considerations in Design | 199 | ||
Summary | 199 | ||
Key Terms | 200 | ||
Discussion Questions | 200 | ||
Problems | 201 | ||
Case 7-1: Keeping Apple’s iPhone Competitive | 203 | ||
Case 7-2: Food Processing Plant: Creating a Quality Product using Blending Improvement Methods | 203 | ||
Chapter 8 Designing Quality Services | 205 | ||
Differences between Services and Manufacturing | 206 | ||
Internal versus External Services | 206 | ||
Voluntary versus Involuntary Services | 207 | ||
How Are Service Quality Issues Different from Those of Manufacturing? | 207 | ||
A Closer look At Quality 8-1: Service Warranties: Profitable or a Rip-off—You Decide | 208 | ||
How Are Service Quality Issues Similar to Manufacturing? | 208 | ||
What Do Services Customers Want? | 208 | ||
Quality Highlight 8-1: Ritz-Carlton Hotels | 210 | ||
SERVQUAL | 211 | ||
Expectations | 211 | ||
Perceptions | 213 | ||
Gap Analysis | 213 | ||
Assessing Differences in Expectations and Perceptions by Using the Differencing Technique | 215 | ||
Designing and Improving the Services Transaction | 218 | ||
Services Blueprinting | 218 | ||
Moments of Truth | 219 | ||
A Closer look At Quality 8-2: Quality in Health Care | 220 | ||
Poka-yoke | 221 | ||
The Customer Benefits Package | 222 | ||
Service Transaction Analysis | 223 | ||
Improving Customer Service in Government | 226 | ||
A Closer look At Quality 8-3: Government Service Quality: A Stopand-\rGo Process | 226 | ||
Quality in Health Care | 227 | ||
Supply Chain Quality in Services | 227 | ||
A Theory for Service Quality Management | 228 | ||
Summary | 229 | ||
Key Terms | 229 | ||
Discussion Questions | 229 | ||
Problems | 230 | ||
Case 8-1: Google Designs Quality Services with Customers in Mind | 234 | ||
Case 8-2: UPS: Delivering the Total Package in Customer Service | 235 | ||
Chapter 9 Managing Supplier Quality in the Supply Chain | 236 | ||
The Value Chain | 236 | ||
The Chain of Customers | 237 | ||
Managing the Supply Chain | 237 | ||
Supplier Alliances | 237 | ||
A Closer look At Quality 9-1: Supply Chains Disruption and Risk\rMitigation | 240 | ||
Single-Sourcing Examples | 240 | ||
Quality Highlight 9-1: A Bumpy Ride at Boeing | 241 | ||
Supplier Development | 242 | ||
Quality Highlight 9-2: Integrating Forward along the Supply Chain: 3M\rDental Products Division | 243 | ||
Supplier Awards | 244 | ||
Supplier Relationship Management Systems (SRMS) | 244 | ||
Applying the Contingency Perspective to Supplier Partnering | 245 | ||
A Supplier Development Program: ISO/TS 16949 | 245 | ||
ISO/TS 16949 | 245 | ||
Quality Management System | 245 | ||
Management Responsibility | 246 | ||
Resource Management | 247 | ||
Product Realization | 247 | ||
Measurement, Analysis, and Improvement | 247 | ||
Building an Understanding of Supply Chain Quality Management | 247 | ||
Summary | 248 | ||
Key Terms | 248 | ||
Discussion Questions | 248 | ||
Case 9-1: AT&T: Setting High Standards for Suppliers and Rewarding Supplier Performance | 249 | ||
Case 9-2: Managing the Supply Chain at Honeywell | 250 | ||
Part 3 Implementing Quality | 263 | ||
Chapter 10 The Tools of Quality | 264 | ||
Improving the System | 264 | ||
Ishikawa’s Basic Seven Tools of Quality | 265 | ||
Process Maps | 266 | ||
A Closer look At Quality 10-1: Extended Value Stream Mapping\rof Supply Chains | 270 | ||
Check Sheets | 272 | ||
Histograms | 273 | ||
Scatter Diagrams | 274 | ||
Control Charts | 276 | ||
Cause-and-Effect (Ishikawa) Diagrams | 276 | ||
Pareto Charts | 278 | ||
The Seven New Tools for Improvement | 281 | ||
The Affinity Diagram | 283 | ||
The Interrelationship Digraph | 285 | ||
Tree Diagrams | 286 | ||
Prioritization Grid | 288 | ||
Matrix Diagram | 290 | ||
Process Decision Program Chart | 291 | ||
Activity Network Diagram | 291 | ||
Reflections on the Managerial N7 Tools | 293 | ||
Other Tools for Performance Measurement | 293 | ||
Spider Charts | 293 | ||
Balanced Scorecards | 293 | ||
Dashboards | 295 | ||
Summary | 295 | ||
Key Terms | 295 | ||
Discussion Questions | 295 | ||
Problems | 296 | ||
Case 10-1: Corporate Universities: Teaching the Tools of Quality | 299 | ||
Case 10-2: Zurich: Creating Quality Customer Care | 300 | ||
Chapter 11 Statistically Based Quality Improvement for Variables | 302 | ||
Statistical Fundamentals | 303 | ||
What Is Statistical Thinking? | 303 | ||
Quality Highlight 11-1: Statistical Tools in Action | 303 | ||
Why Do Statistics Sometimes Fail in the Workplace? | 304 | ||
Understanding Process Variation | 304 | ||
Process Stability | 306 | ||
Sampling Methods | 306 | ||
Random Samples | 306 | ||
Systematic Samples | 306 | ||
Sampling by Rational Subgroups | 306 | ||
Planning for Inspection | 307 | ||
Control Plans | 307 | ||
Process Control Charts | 307 | ||
Variables and Attributes Control Charts | 307 | ||
A Generalized Procedure for Developing Process Charts | 309 | ||
Understanding Process Charts | 309 | ||
x– and R Charts | 311 | ||
Interpreting Control Charts | 312 | ||
Using Excel to Draw x– and R Charts | 317 | ||
X and Moving Range (MR) Charts for Population Data | 318 | ||
Using Excel to Draw X and MR Charts | 319 | ||
Median Charts | 320 | ||
Using Excel to Draw Median Charts | 321 | ||
x– and s Charts | 322 | ||
Using Excel to Draw x– and s Charts | 323 | ||
Other Control Charts | 323 | ||
Moving Average Chart | 323 | ||
Cusum Chart | 324 | ||
Some Control Chart Concepts for Variables | 324 | ||
Choosing the Correct Variables Control Chart | 324 | ||
Corrective Action | 326 | ||
How Do We Use Control Charts to Continuously Improve? | 326 | ||
Tampering with the Process | 326 | ||
Process Capability for Variables | 326 | ||
A Closer look At Quality 11-1: A Justification for Meeting Standards\rin Software Quality | 327 | ||
Population versus Sampling Distributions | 327 | ||
Capability Studies | 329 | ||
Ppk | 331 | ||
The Difference between Capability and Stability | 331 | ||
Other Statistical Techniques in Quality Management | 331 | ||
Summary | 332 | ||
Key Terms | 333 | ||
Discussion Questions | 333 | ||
Problems | 333 | ||
Case 11-1: Ore-Ida Fries | 337 | ||
Chapter 12 Statistically Based Quality Improvement for Attributes | 339 | ||
Generic Process for Developing Attributes Charts | 340 | ||
Understanding Attributes Charts | 340 | ||
p Charts for Proportion Defective | 340 | ||
Using Excel to Draw p Charts | 342 | ||
np charts | 343 | ||
Using Excel to Draw np Charts | 345 | ||
c and u Charts | 345 | ||
Using Excel to Draw c and u Charts | 347 | ||
Attributes Charts Summary | 348 | ||
Choosing the Right Attributes Chart | 348 | ||
Reliability Models | 349 | ||
Series Reliability | 349 | ||
Parallel Reliability | 350 | ||
Measuring Reliability | 351 | ||
Mean Time to Failure (MTTF) | 352 | ||
A Closer look At Quality 12-1: Quality Control at GNC | 352 | ||
System Availability | 353 | ||
Summary | 354 | ||
Key Terms | 354 | ||
Discussion Questions | 354 | ||
Problems | 354 | ||
Case 12-1: Decision Sciences Institute National Conference | 358 | ||
Chapter 13 Lean-Six Sigma Management and Tools | 361 | ||
What Is Six Sigma? | 362 | ||
Organizing Lean-Six Sigma | 363 | ||
Packaging Lean with Six Sigma | 365 | ||
A Closer look At Quality 13-1: Lean/Six Sigma at Textron | 365 | ||
DMAIC Overview | 366 | ||
A Closer look At Quality 13-2: DMAIC in Action | 367 | ||
Define Phase | 367 | ||
Developing the Business Case | 368 | ||
Project Evaluation | 368 | ||
Pareto Analysis | 371 | ||
Problem Definition | 371 | ||
Measure Phase | 371 | ||
Selecting Process Outcomes | 371 | ||
FMEA | 375 | ||
Verifying Measurements | 375 | ||
Gauge R&R | 376 | ||
Using Excel to Perform Gauge R&R Analysis | 379 | ||
Analyze Phase | 379 | ||
Defining Objectives | 379 | ||
Identifying Xs | 379 | ||
Analyzing Sources of Variation | 379 | ||
Improve Phase | 380 | ||
Control Phase | 380 | ||
Taguchi Design of Experiments | 381 | ||
Robust Design | 381 | ||
Background of the Taguchi Method | 382 | ||
Taguchi Definition of Quality | 382 | ||
Quality Loss Function | 382 | ||
The Taguchi Process | 384 | ||
Using Excel to Solve Taguchi Experiments | 386 | ||
Design for Six Sigma | 387 | ||
Lean-Six Sigma from a Contingency Perspective | 388 | ||
Summary | 388 | ||
Key Terms | 388 | ||
Discussion Questions | 389 | ||
Problems | 389 | ||
Case 13-1: The Neiman-Marcus Cookie | 394 | ||
Part 4 Forever Improving the Quality System | 395 | ||
Chapter 14 Managing Quality Improvement Teams and Projects | 396 | ||
Why Employees Enjoy teams | 397 | ||
Leading Teams for Quality Improvement | 397 | ||
Employee Empowerment and Involvement | 397 | ||
A Closer look At Quality 14-1: Empowerment in Action | 399 | ||
Flattening Hierarchies for Improved Effectiveness | 399 | ||
Team Leader Roles and Responsibilities | 400 | ||
Team Roles and Responsibilities | 401 | ||
Team Formation and Evolution | 401 | ||
Team Rules | 402 | ||
Types of Teams | 403 | ||
Process Improvement Teams | 403 | ||
Cross-Functional Teams | 403 | ||
Tiger Teams | 403 | ||
Natural Work Groups | 403 | ||
Self-Directed Work Teams | 404 | ||
Virtual Teams | 404 | ||
A Closer look At Quality 14-2: Lessons from Effective Teams Outside the Business World | 404 | ||
Implementing Teams | 405 | ||
Meeting Management | 406 | ||
Conflict Resolution in Teams | 407 | ||
Saving Quality Teams from Failure: Diagnosing Problems and Intervening Before it Is Too Late | 409 | ||
Managing and Controlling Projects | 410 | ||
Qualifying Projects | 410 | ||
Project Charters | 411 | ||
Force-Field Analysis | 412 | ||
Work Breakdown Structure (WBS) | 413 | ||
Identifying Precedence Relationships | 414 | ||
Identifying Outcome Measures | 414 | ||
Identifying Task Times | 414 | ||
Activity Network Diagrams | 415 | ||
Arrow Gantt Charts | 419 | ||
Managing Multiple Projects | 419 | ||
Summary | 420 | ||
Key Terms | 421 | ||
Discussion Questions | 421 | ||
Problems | 422 | ||
Case 14-1: General Motors: Technical Problem Solving Group Drives Excellence | 424 | ||
Chapter 15 Implementing and Validating the Quality System | 426 | ||
Building Blocks for the System of Quality Improvement | 427 | ||
People | 427 | ||
Organizational Learning and Knowledge | 428 | ||
Culture | 429 | ||
Closeness to Customers | 429 | ||
Information and Finance | 430 | ||
The Three Spheres of Quality | 430 | ||
The Integrative Approach | 430 | ||
Alignment between the Quality System and Strategy | 431 | ||
Quality Highlight 15-1: Back to Basics at Ford | 431 | ||
Internal Validation: Documenting and Assessing the Quality System | 431 | ||
A Closer look At Quality 15-1: A Simple Self-Assessment Tool | 434 | ||
Quality Audits | 437 | ||
Quality Audit Process | 438 | ||
Types of Audits | 439 | ||
Qualitative and Quantitative Elements in Audits | 440 | ||
Validating the Quality System | 440 | ||
Summary | 441 | ||
Key Terms | 441 | ||
Discussion Questions | 442 | ||
Problems | 442 | ||
Case 15-1: Setting Priorities Using the Baldrige Criteria | 442 | ||
Appendix | 445 | ||
Glossary | 448 | ||
Index | 463 |