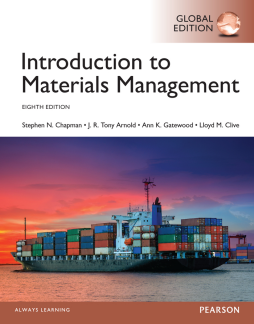
BOOK
Introduction to Materials Management, Global Edition
Steve Chapman | Ann K. Gatewood | Tony K. Arnold | Lloyd Clive
(2016)
Additional Information
Book Details
Abstract
For all courses in Materials Management, Production, Inventory Control, and Logistics taught in business and industrial technology departments of community colleges, four-year colleges, and universities.
Understand all elements of production planning and control, and how they fit together with Introduction to Materials Management.
Clearly written and exceptionally user-friendly, this text covers all the essentials of modern supply chain management, manufacturing planning and control systems, purchasing, and physical distribution. Content, examples, questions, and problems lead students step-by-step to mastery. Widely adopted by colleges and universities worldwide, this is the only APICS-listed reference text for the Basics of Supply Chain Management (BSCM) CPIM certification examination.
Table of Contents
Section Title | Page | Action | Price |
---|---|---|---|
Cover | Cover | ||
Title Page | 3 | ||
Copyright Page | 4 | ||
Contents | 5 | ||
Preface | 9 | ||
Chapter 1 Introduction to Materials Management | 13 | ||
Introduction | 13 | ||
Operating Environment | 13 | ||
The Supply Chain Concept | 16 | ||
What is Materials Management? | 21 | ||
Summary | 25 | ||
Key Terms | 26 | ||
Questions | 26 | ||
Problems | 27 | ||
Case Study 1.1: Priya’s Cakes | 27 | ||
Chapter 2 Production Planning System | 30 | ||
Introduction | 30 | ||
Manufacturing Planning and Control System | 31 | ||
Sales and Operations Planning | 35 | ||
Manufacturing Resource Planning | 37 | ||
Enterprise Resource Planning | 39 | ||
Making the Production Plan | 39 | ||
Summary | 48 | ||
Key Terms | 49 | ||
Questions | 49 | ||
Problems | 50 | ||
Case Study 2.1: Meridian Water Pumps | 54 | ||
Case Study 2.2: Williams 3D Printers | 55 | ||
Chapter 3 Master Scheduling | 57 | ||
Introduction | 57 | ||
Relationship to Production Plan | 58 | ||
Developing a Master Production Schedule | 60 | ||
Production Planning, Master Scheduling, and Sales | 65 | ||
Summary | 71 | ||
Key Terms | 71 | ||
Questions | 71 | ||
Problems | 72 | ||
Case Study 3.1: Acme Water Pumps | 78 | ||
Case Study 3.2: The MasterChip Electronics Company | 79 | ||
Case Study 3.3: Macarry’s Bicycle Company | 81 | ||
Chapter 4 Material Requirements Planning | 84 | ||
Introduction | 84 | ||
Bills of Material | 86 | ||
Material Requirements Planning Process | 93 | ||
Using the Material Requirements Plan | 104 | ||
Summary | 108 | ||
Key Terms | 108 | ||
Questions | 108 | ||
Problems | 109 | ||
Case Study 4.1: Apix Polybob Company | 120 | ||
Case Study 4.2: Benzie Products Company | 122 | ||
Chapter 5 Capacity Management | 124 | ||
Introduction | 124 | ||
Definition of Capacity | 124 | ||
Capacity Planning | 125 | ||
Capacity Requirements Planning | 126 | ||
Capacity Available | 128 | ||
Capacity Required (Load) | 131 | ||
Scheduling Orders | 134 | ||
Making the Plan | 135 | ||
Summary | 137 | ||
Key Terms | 137 | ||
Questions | 138 | ||
Problems | 139 | ||
Case Study 5.1: Wescott Products | 142 | ||
Chapter 6 Production Activity Control | 145 | ||
Introduction | 145 | ||
Data Requirements | 148 | ||
Order Preparation | 149 | ||
Scheduling | 150 | ||
Load Leveling | 155 | ||
Scheduling in a Nonmanufacturing Setting | 156 | ||
Scheduling Bottlenecks | 156 | ||
Theory of Constraints and Drum-Buffer-Rope | 158 | ||
Implementation | 161 | ||
Control | 162 | ||
Production Reporting | 167 | ||
Product Tracking | 168 | ||
Measurement Systems | 168 | ||
Summary | 168 | ||
Key Terms | 169 | ||
Questions | 169 | ||
Problems | 170 | ||
Case Study 6.1: Johnston Products | 174 | ||
Case Study 6.2: Crofts Printing Company | 176 | ||
Case Study 6.3: Melrose Products | 177 | ||
Chapter 7 Purchasing | 180 | ||
Introduction | 180 | ||
Establishing Specifications | 183 | ||
Functional Specification Description | 185 | ||
Selecting Suppliers | 187 | ||
Price Determination | 190 | ||
Impact of Material Requirements Planning on Purchasing | 192 | ||
Environmentally Responsible Purchasing | 194 | ||
Expansion of Purchasing into Supply Chain Management | 195 | ||
Some Organizational Implications of Supply Chain Management | 197 | ||
Summary | 198 | ||
Key Terms | 198 | ||
Questions | 198 | ||
Problems | 199 | ||
Case Study 7.1: Let’s Party! | 199 | ||
Case Study 7.2: The Connery Company | 200 | ||
Chapter 8 Forecasting and Demand Management | 202 | ||
Introduction | 202 | ||
Demand Management | 202 | ||
Demand Forecasting | 204 | ||
Characteristics of Demand | 204 | ||
Principles of Forecasting | 206 | ||
Collection and Preparation of Data | 207 | ||
Forecasting Techniques | 207 | ||
Some Important Intrinsic Techniques | 209 | ||
Seasonality | 212 | ||
Tracking the Forecast | 215 | ||
Summary | 222 | ||
Key Terms | 222 | ||
Questions | 222 | ||
Problems | 223 | ||
Case Study 8.1: Northcutt Bikes: The Forecasting Problem | 229 | ||
Case Study 8.2: Hatcher Gear Company | 231 | ||
Chapter 9 Inventory Fundamentals | 233 | ||
Introduction | 233 | ||
Aggregate Inventory Management | 233 | ||
Item Inventory Management | 233 | ||
Inventory and the Flow of Material | 234 | ||
Supply and Demand Patterns | 235 | ||
Functions of Inventories | 235 | ||
Objectives of Inventory Management | 237 | ||
Inventory Costs | 239 | ||
Financial Statements and Inventory | 241 | ||
ABC Inventory Control | 246 | ||
Summary | 249 | ||
Key Terms | 249 | ||
Questions | 250 | ||
Problems | 251 | ||
Case Study 9.1: Randy Smith, Inventory Control Manager | 254 | ||
Chapter 10 Order Quantities | 257 | ||
Introduction | 257 | ||
Economic Order Quantity | 258 | ||
Variations of the EOQ Model | 262 | ||
Quantity Discounts | 263 | ||
Order Quantities for Families of Product When Costs are Not Known | 264 | ||
Period Order Quantity | 265 | ||
Summary | 268 | ||
Key Terms | 268 | ||
Questions | 268 | ||
Problems | 269 | ||
Chapter 11 Independent Demand Ordering Systems | 273 | ||
Introduction | 273 | ||
Order Point System | 273 | ||
Determining Safety Stock | 275 | ||
Determining Service Levels | 281 | ||
Different Forecast And Lead-Time Intervals | 283 | ||
Determining When the Order Point Is Reached | 283 | ||
Periodic Review System | 285 | ||
Distribution Inventory | 287 | ||
Summary | 290 | ||
Key Terms | 290 | ||
Questions | 291 | ||
Problems | 292 | ||
Case Study 11.1: Carl’s Computers | 298 | ||
Chapter 12 Physical Inventory and Warehouse Management | 301 | ||
Introduction | 301 | ||
Warehousing Management | 301 | ||
Physical Control and Security | 307 | ||
Inventory Record Accuracy | 307 | ||
Consignment Inventory and Vendor-Managed Inventory (VMI) | 313 | ||
Technology Applications | 314 | ||
Summary | 315 | ||
Key Terms | 315 | ||
Questions | 316 | ||
Problems | 316 | ||
Case Study 12.1: CostMart Warehouse | 320 | ||
Chapter 13 Physical Distribution | 323 | ||
Introduction | 323 | ||
Physical Distribution | 326 | ||
Physical Distribution Interfaces | 329 | ||
Transportation | 330 | ||
Legal Types of Carriage | 332 | ||
Transportation Cost Elements | 333 | ||
Warehousing | 338 | ||
Packaging | 343 | ||
Material Handling | 345 | ||
Multi-Warehouse Systems | 345 | ||
Summary | 348 | ||
Key Terms | 348 | ||
Questions | 349 | ||
Problems | 350 | ||
Case Study 13.1: ABC Footwear Limited | 351 | ||
Chapter 14 Products and Processes | 353 | ||
Introduction | 353 | ||
Need for New Products | 353 | ||
Product Development Principles | 354 | ||
Product Specification and Design | 356 | ||
Process Design | 358 | ||
Factors Influencing Process Design | 359 | ||
Processing Equipment | 361 | ||
Process Systems | 361 | ||
Process Costing | 363 | ||
Selecting the Process | 364 | ||
Continuous Process Improvement | 366 | ||
Summary | 376 | ||
Key Terms | 377 | ||
Questions | 377 | ||
Problems | 379 | ||
Case Study 14.1: Rory Thomas, Production Manager | 382 | ||
Chapter 15 Lean Production | 384 | ||
Introduction | 384 | ||
Lean Production | 384 | ||
Waste | 386 | ||
The Lean Production Environment | 388 | ||
Manufacturing Planning and Control in a Lean Production Environment | 395 | ||
Comparing ERP, Kanban, and Theory of Constraints | 407 | ||
Summary | 409 | ||
Key Terms | 410 | ||
Questions | 410 | ||
Problems | 411 | ||
Case Study 15.1: Murphy Manufacturing | 413 | ||
Chapter 16 Total Quality Management | 416 | ||
Introduction | 416 | ||
What Is Quality? | 416 | ||
Total Quality Management | 418 | ||
Quality Cost Concepts | 422 | ||
Variation as a Way of Life | 423 | ||
Process Capability | 425 | ||
Process Control | 429 | ||
Sample Inspection | 432 | ||
ISO 9000:2015 | 434 | ||
ISO 26000:2010 | 435 | ||
ISO 14001:2015 | 436 | ||
Benchmarking | 436 | ||
Six Sigma | 437 | ||
Quality Function Deployment | 438 | ||
The Relationship of Lean Production, TQM, and ERP | 440 | ||
Summary | 441 | ||
Key Terms | 441 | ||
Questions | 442 | ||
Problems | 443 | ||
Case Study 16.1: Accent Oak Furniture Company | 444 | ||
Readings | 449 | ||
Index | 453 |